Exploring the Advantages and Challenges of Carbon Fiber in Cars
What is carbon fiber made from?
Carbon fiber is a composite material that is made of long strings of molecules attached together by carbon atoms and resin. The majority of carbon fibers produced are derived from polyacrylonitrile (PAN). The other 10% is composed of rayon or petroleum pitch. As a result, carbon fiber is a high-performance material that has been used in various industries, including aerospace, sports equipment, and automotive. Carbon fiber offers many benefits that make it an ideal material for use in cars.

What is carbon fiber-reinforced plastic?
Carbon Fiber Reinforced Polymer (CFRP) is an advanced carbon composite material that is extremely strong, lightweight, and also has great corrosion and fatigue resistance properties. CFRP is constructed of two parts: the base, or matrix, and the carbon fiber that reinforces the matrix.
Is carbon fiber good for cars?
Carbon fiber has become popular in the automotive industry due to its lightweight and high strength-to-weight ratio. Until recently, carbon fiber parts were primarily used on high-end sports cars such as the McLaren Senna, Audi R8, and Koenigsegg Agera RS because it lowers the vehicle’s weight while still being able to withstand the stresses of racing at high speeds. However, due to the price associated with the fabrication of carbon fiber, it is cost prohibitive to use on mainstream vehicles. However, recently companies like Nissan have publicly stated they have a new process that can cut the production time of carbon fiber in half and permit them to manufacture carbon fiber parts on a mass-market vehicle. Nissan currently incorporates carbon fiber on their GT-R and plans on incorporating this new technology into their new all-electric Ariya. Here are some of the benefits of using carbon fiber in cars:
- Lightweight material: Carbon fiber is about five times lighter than steel, making it an ideal material for car manufacturers who want to reduce weight and increase fuel efficiency.
- High strength-to-weight ratio: Carbon fiber is stronger than steel but lighter in weight. This property makes it an excellent material for cars because it offers the desired strength without compromising weight.
- Increased fuel efficiency: Cars made of carbon fiber are lighter, and this means they require less fuel to move. This property is essential in the automotive industry as fuel efficiency is becoming a critical factor in car design.
- Enhanced performance and handling: The lightweight nature of carbon fiber makes cars made from this material faster and more agile than those made from traditional materials. Carbon fiber also offers better handling and stability, which is essential for high-performance cars.
- Improved crashworthiness: Carbon fiber has excellent energy absorption properties, making it an ideal material for car manufacturers looking to make cars safer.

Do regular cars use carbon fiber parts?
high-end vehicles commonly feature carbon fiber parts and accessories. On some models, every body panel or even the chassis is made of carbon fiber. Some examples of carbon fiber applications in cars:
- Suspension systems: Carbon fiber suspension systems offer better handling and stability due to their lightweight and stiffness properties.
- Interior components: Carbon fiber can be used in interior components such as dashboards, steering wheels, and center consoles to give cars a sporty look.
- Wheels: Carbon fiber wheels are lighter than traditional wheels, reducing unsprung mass and improving handling and acceleration.
- Brake systems: Carbon fiber brake systems offer better stopping power and less fade than traditional brakes.
- Body panels and structural components: Carbon fiber can be used in body panels and structural components such as roofs, hoods, and doors, to reduce weight and improve crashworthiness performance.
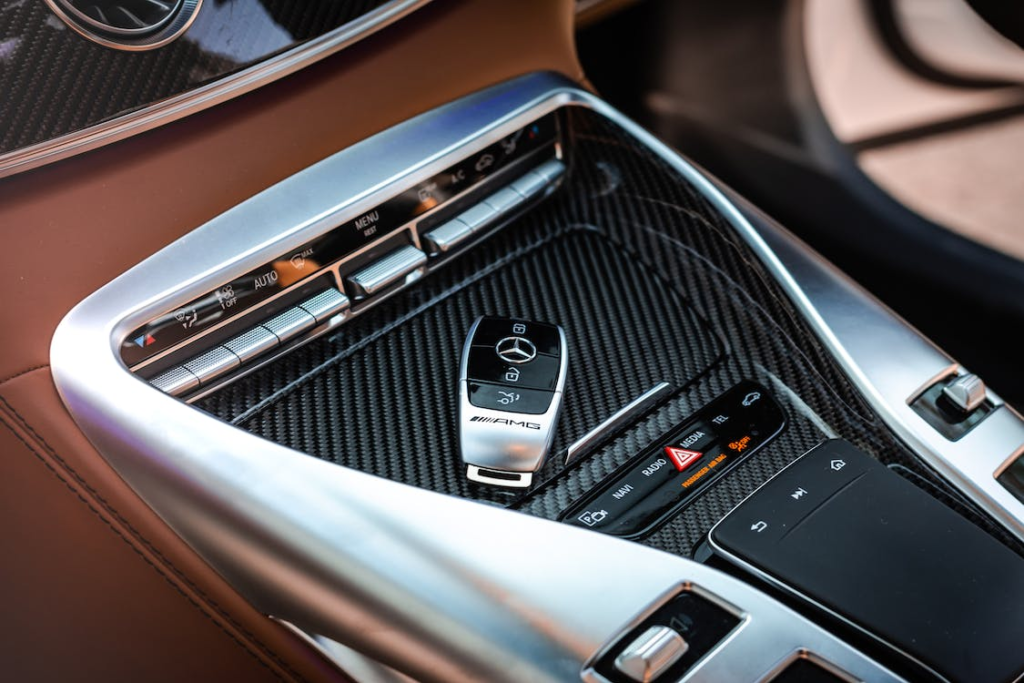
Example of Carbon fiber roof design
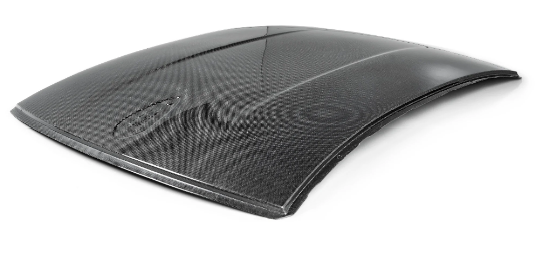
The biggest reason why carbon fiber is not mainstream in cars is cost. For example, while designing a roof, automakers are constantly making tradeoffs between the energy absorbed by a roof system and roof system mass to determine the best design solution. In order to have an optimum design for a roof crush test, the strength-to-weight ratio (SWR) of the vehicle is crucial. Even though a traditional roof does not add much structural benefit it can however add noticeable mass. A traditional metal roof panel provides high energy absorption however new studies have shown that if you sandwich a carbon fiber roof panel with a polypropylene foam core, you can achieve a better SWR achieving weight reduction of the roof system. [8]
After optimizing this design it was found that the ideal construction of this sandwich carbon fiber reinforced plastic (CFRP) would consist of a face-sheet thickness of 0.8mm with a foam core with a density of 70 kg/m3. When the roof crush analysis was conducted on a sandwich CFRP roof panel, it was observed that the new roof panel significantly contributed to a reduction in the roof panel mass, as much as 68% mass reduction. The sandwich CFRP roof was able to meet its crashworthiness targets and lightweight requirements proving that it can meet the performance of a traditional metallic roof panel.[2] [8] This reason a CFRP roof panel is able to meet the same performance as a traditional roof is due to the fact that a portion of the strength of these CFRP panels comes from an increase in the resistance to elastic local buckling and local deformation such as crushing and folding. [7]
In the past several automakers have looked at using a carbon fiber roof panel, but the automakers ran into problems. Primary causes by the unfilled resin and voids at the corner section of the roof panels fabricated by the conventional prepreg compression molding (PCM) process. These voids can act as stress risers and lead to cracks in the panel which could lead to water leakage in a roof. However, current advances in technologies in the molding of CFRP are making a lightweight roof panel using CFRP plausible. [4] New technology such as vacuum-assisted resin transfer molding (VA-RTM) is a process in which resin is pushed through a square opening into a mold using an induced pressure gradient. The VA-RTM process with a porous mold led to straight specimens of CFRP with low void content and good mechanical properties, when contrasted to a specimen made with the conventional process. [4] Studies are currently being conducted using CFRP roof panels fabricated by the VA-RTM process, the results show that the defects found are minimal if any. However, a few voids were found. The overall, void content of the CFRP roof panels manufactured by the VA-RTM process was lowered by around 3% when compared to the CFRP manufactured by a traditional process. [4] When a bending test was conducted to compare the energy absorption of the VA-RTM roof panel to a traditional roof panel, the results showed that the energy absorption of the CFRP roof panels had improved performance and could absorb up to 36% more energy than a traditional roof panel. [4][7]
Finally, by forming the two 0.8mm face sheets of the sandwich CFRP using the VA-RTM technology instead of a traditional PCM it is possible to reduce the defect rate and complete the forming and curing process in a single mold. This solves issues that were previously plaguing the CFRP roof, such as the porosities and the cost of manufacturing CFRP parts. The VA-PCM process can be used to produce automotive roof panels at reduced equipment and total process costs while improving mechanical properties and reducing part porosity [4]. Even though the cost for a CFRP roof is not as economical as a traditional roof currently since these technologies are new, there is still great potential to reduce the cost of manufacturing to make it much more feasible for mass production. [2]
Why carbon fiber is not used in cars?
While carbon fiber offers many advantages, there are some challenges associated with using this material in cars:
- High cost of production: Carbon fiber is expensive to produce, and this makes cars made from this material more expensive than those made from traditional materials.
- Difficulty in repairing: Carbon fiber is challenging to repair in case of damage, and this can make repairs more costly.
- Limited availability: Carbon fiber is not widely available, and this can make it difficult for car manufacturers to produce cars using this material on a large scale.
- Concerns about environmental impact: Carbon fiber production requires a lot of energy and generates waste that can harm the environment. In addition, there are concerns with the end of Line (EOL) recyclability of CFRP due to the fact that these composites are very difficult to recycle.
- Conducts heat /electricity: The main component of carbon fiber is carbon, and its molecular structure is similar to graphite. Thus, it behaves like metal because its electrical conductivity is extremely high.

Can carbon fiber be used for a car frame?
Although most cars have steel bodies in white structures, automakers are starting to experiment with alternative lightweight materials such as carbon fiber. The main obstacle carbon fiber must overcome before becoming adopted on a mass market scale is cost. However, as companies like Nissan continue to experiment with carbon fiber, the cost of this technology will continue to drop, making it even more feasible for more vehicles. Not every part of the body in white will lend itself to adopting carbon fiber as an alternative to steel parts. Nonetheless, there are still many parts in which carbon fiber is an excellent alternative primarily the exterior class A closures of a vehicle such as the exterior roof panel. If production cost continues to drop for carbon fiber components, incorporating this technology into the roof system would enable a lighter-weight system without jeopardizing the structural integrity and engineering requirements of the roof system.
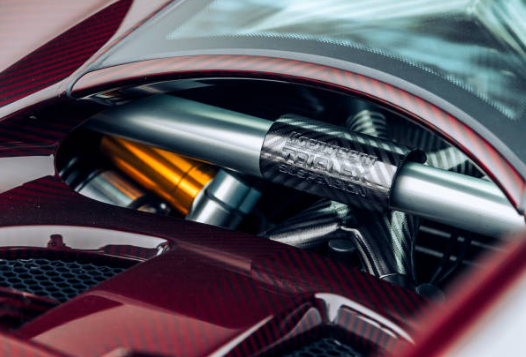
Future of carbon fiber in the automotive industry
The implementation of advanced materials into the automotive industry really depends on many factors such as cost, availability, manufacturing technology, and mostly a necessity. The current projections are that automobiles made in 2040 on average will be made with 17% carbon fiber, which is a huge jump from where we currently stand. In the future, as the applications widen and manufacturing technology improves to accommodate the high energy-intensive CFRP manufacturing, the cost will be reduced to $5-7/lb compared to the $10-12/lb available today.
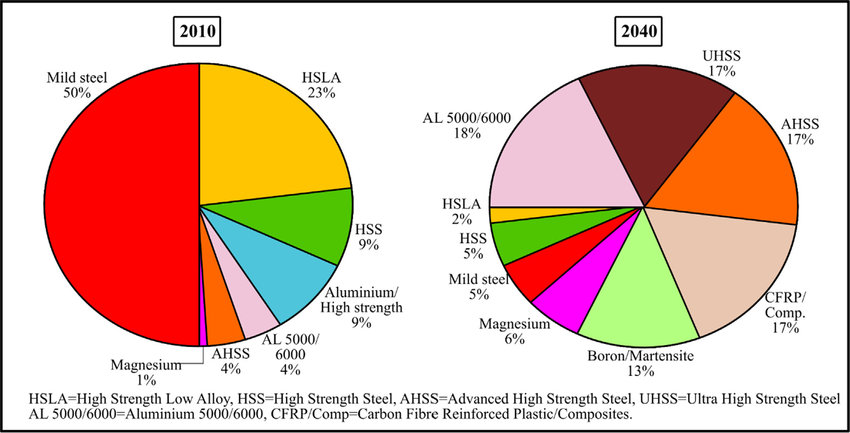
Summary/Conclusions
Carbon fiber is a high-performance material that offers many benefits in the automotive industry. While there are challenges associated with using carbon fiber in cars, the advantages outweigh the drawbacks. As a result, the future of carbon fiber in the automotive industry is promising. Car manufacturers are investing in research to find ways to reduce the cost of production and make carbon fiber more accessible. The increased adoption of carbon fiber in mainstream cars will make it easier for car manufacturers to produce cars using this material on a large scale. There is also potential for new applications of carbon fiber in cars, such as batteries, which can lead to the development of lighter and more efficient electric cars.
References
- C.D. Horvath, Chapter 2 – Advanced steels for lightweight automotive structures, Editor(s): P.K. Mallick,In Woodhead Publishing in Materials, Materials, Design, and Manufacturing for Lightweight Vehicles (Second Edition), Woodhead Publishing, 2021, Pages 39-95, ISBN 9780128187128, https://doi.org/10.1016/B978-0-12-818712-8.00002-1 (http://www.sciencedirect.com/science/article/pii/B9780128187128000021)
- Cui, A., Xu, X., Sun, W., Yang, W., Huang, X., & Liu, T. (2020). Study on crashworthiness optimization of carbon-fiber sandwich panel structure with polypropylene foam core. [基于耐撞性的碳纤维/聚丙烯泡沫夹芯板结构优化研究] Qiche Gongcheng/Automotive Engineering, 42(6), 840-846. doi:10.19562/j.chinasae.qcgc.2020.06.020
- Konrad M. Dobbertin, et all, The relationship between vehicle roof crush and head, neck and spine injury in rollover crashes, Accident Analysis & Prevention, Volume 58, 2013, Pages 46-52, ISSN 0001-4575,
- https://doi.org/10.1016/j.aap.2013.04.020. Jeong-Min Lee, Byung-Min Kim, Dae-Cheol Ko, Development of vacuum-assisted prepreg compression molding for production of automotive roof panels, Composite Structures, Volume 213, 2019, Pages 144-152, ISSN 0263-8223, https://doi.org/10.1016/j.compstruct.2019.01.092. (http://www.sciencedirect.com/science/article/pii/S0263822318315009)
- Mahmood, H. F., & Baccouche, M. R. (1996). Design of automotive body structure for roof crush. American Society of Mechanical Engineers, Applied Mechanics Division, AMD, 218, 25-32. Retrieved from www.scopus.com
- Muthuraju, K., & Lakshmankumar, A. (2020). Experimental studies of different thick steel sheets and variable clearance in MIG brazing. Paper presented at the IOP Conference Series: Materials Science and Engineering, , 912(3) doi:10.1088/1757-899X/912/3/032078 Retrieved from www.scopus.com
- M.R. Bambach, Fibre composite strengthening of thin steel passenger vehicle roof structures, Thin-Walled Structures, Volume 74, 2014, Pages 1-11, ISSN 0263-8231, https://doi.org/10.1016/j.tws.2013.09.018. (http://www.sciencedirect.com/science/article/pii/S0263823113002401)
- Soroosh Borazjani, Giovanni Belingardi, Development of an innovative design of a composite-sandwich based vehicle roof structure, Composite Structures, Volume 168, 2017, Pages 522-534, ISSN 0263-8223, https://doi.org/10.1016/j.compstruct.2017.02.015. (http://www.sciencedirect.com/science/article/pii/S0263822317302052)
- UK project develops carbon/flax hybrid automotive roof, Reinforced Plastics, Volume 60, Issue 1, 2016, Page 6, ISSN 0034-3617, https://doi.org/10.1016/j.repl.2015.12.067. (http://www.sciencedirect.com/science/article/pii/S0034361715008796)
Definitions/Abbreviations
BSO Body side outer
CFRP Carbon fiber reinforced plastic
HSS High strength steel
SWR UVW Strength to weight ratio Unloaded vehicle weight
VA-RTM Vacuum-assisted resin transfer molding