What is the metal casting process?
What is the history of casting?
Casting is the oldest manufacturing process, the first casting of metals can actually be traced all the way back to around 4000 BC: copper castings in Mesopotamia.
Around 3500 BC, Bronze casting was developed by the ancient Sumerians in western Asia. Around 1200 BC bronze casting started to appear in Greece, Africa, Mesopotamia, and other parts of Asia.
Even though the Chinese produced cast iron as early as the 6th-century bc, Iron casting wasn’t adopted and used by the western world until 1600 – 1800 AD.
What does casting mean?
Casting is the act or process of making objects or parts in a foundry by pouring molten material into a mold. This metal is then allowed to cool and solidify (solidification), taking the shape of the mold. The four main steps in casting are:
- Metal heating and melting
- Pouring the molten metal
- Metal solidification
- Heat treatment of casting

How is metal melted in foundry?
The metal is put into a electric or gas furnaces and overheat up to a beyond its melting point to transform the solid metal into a liquid state. The heat energy required is the sum of:
- Heat to raise temperature to melting point
- Heat of fusion to convert solid to liquid
- Heat to raise molten metal to desired pouring temperature
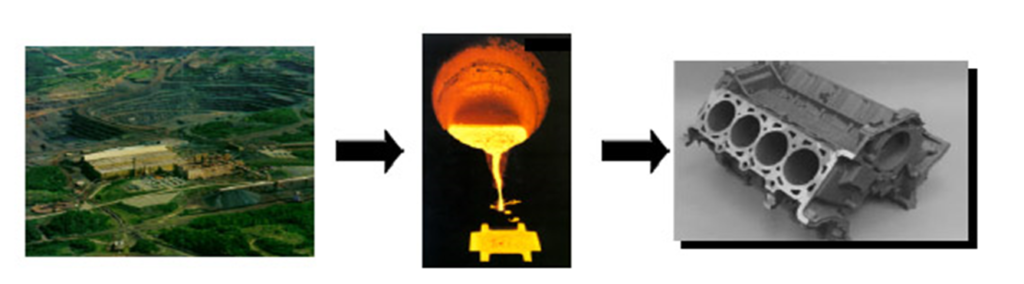
What are the advantages of the casting process?
Having high-quality molten metal is the first step in producing high-quality castings. Some of the advantages of the casting process when compared to other manufacturing processes are:
- Cost-effectiveness and fast
- Can create parts with complex internal and external geometries
- Product quality, create near-net shape components
- Parts are easy to recycle
- Can be used to create parts of a wide range of sizes
What are the disadvantages of casting?
some of the disadvantages of the casting process are:
- Mechanical properties are usually inferior to those of wrought metals
- The load-bearing capacity of a cast part is usually less than that of forged parts
- Dimensional tolerances are less than those in wrought processes
- Surface finishes can be poor
- Safety Issues (poor working environment)
- Environmental Issues
What are some general defects encountered in casting processes? Name and briefly describe three.
General flaws encountered in the casting process are the porosities that are formed within cast parts such as gas porosities, pinholes, open holes, and blowholes. There are various ways to form porosities in metal while casting. Under high temperatures, the molten metal can react to moisture present in its surroundings and trap gas vapor. The metal solidifies before the gas vapor can escape, thus resulting in a cast hole in the part. If you are casting a non-eutectic metal alloy, during the solidification process, dendrites will begin to form, these dendrites are impossible to eliminate and will also result in micro-porosities.
If your flow rate is too high while pouring molten metal into the mold, it can cause turbulence inside the mold cavity. Turbulence inside of the mold can also trap gasses, also resulting in porosities on your part. If you do not control your flow rate correctly, it is possible to not full fill your mold. This can happen with having too slow a flow rate where the metal begins to cool and solidify before completely filling the mole or because of turbulence in the flow causing excess energy loss, in both instances, premature solidification will occur.
During the casting process, it is also not uncommon to have metallurgical defects from hot tears and hot spots. Another deficiency in casting is because of metal shrinkage, which occurs during cool-down or solidification. Most metals like many other elements expand when they melt and shrink when they solidify this is known as solidification shrinkage. This shrinkage must be considered when molding a part. To achieve the requested dimensional size, molds are generally made larger to compensate for the shrinkage that may result depending on the alloy.
What are the three types of casting?
The three main casting processes are permanent mold (die casting), expendable pattern and mold (Investment casting), and expendable mold/ permanent pattern (sand casting). Of these three expendable mold/permanent pattern sand casting.

What are the two types of casting molds?
The casting mold type process is subdivided into two main categories:
- Expendable mold processes –mold must be destroyed to remove casting
- non-expendable casting/Permanent mold processes – mold can be used many times to produce many castings.
What are examples of expendable mold?
Expendable mold casting is a type of casting process that uses a non-reusable mold. Several examples of expendable mold casting are sand, plastic, shell, plaster, and lost foam/lost wax casting. As part complexity increases, the likelihood of using expendable molds increases. It is very common to use expendable mold for small production runs of specialized castings for example pump housings. It is also common to use expendable mold for mass production of intricate components for example engine blocks and cylinder heads.
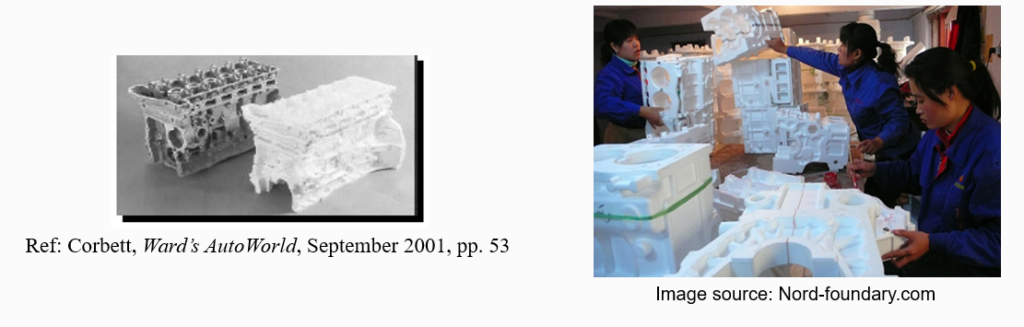
What are the types of permanent mold casting?
Unlike expendable mold, a permanent mold casting uses a mold material that is used repeatedly. Permanent mold casting is better for consistent production volumes due to the mold being made from tool steel to withstand high casting temperatures. There are four main types of permanent mold casting: gravity, slush, low-pressure, and vacuum.
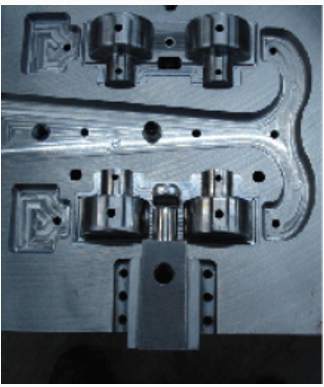
What automobile parts are cast?
Internal combustion engine vehicles (ICEs) have more casted parts when compared to electric vehicles (EVs). Many of the cast parts in an ICE vehicle are part of the powertrain system such as the pistons, engine blocks, valve covers, transmission housing, and rear differential housing. However other systems such as the chassis also use cast parts such as the metal rim, brake rotors/disk/ drums. The electrical system uses cast parts in alternator housing. Some companies are also starting to make large parts of the body structure out of cast parts to reduce the number of parts in the body-in-white.

Which casting process is used in automobile industry?
The automotive industry relies on casting for manufacturing a wide range of part. Following are the commonly used casting processes in automotive applications:
- Sand Casting
- Die casting
- Lost Wax casting
- Lost Foam casting
- Cosworth Casting Squeeze casting
What are the different parts (features) of a casting mold?
Cross section of a typical sand mold illustrating various features. The typical sand casting mold contains two parts, the drag (bottom), and the cope (top). The molten metal is poured into the cup or pouring basin. The mold contains many features (open/blind riser and vents) to ensure that the mold cavity is completely full thus ensuring a high-quality part.
Mold Terminology:
- Cavity
- Well
- Gating System
- Sprue or Downsprue
- Runner
- Gates
- Riser
- Parting Line
- Flask/Cope/Drag
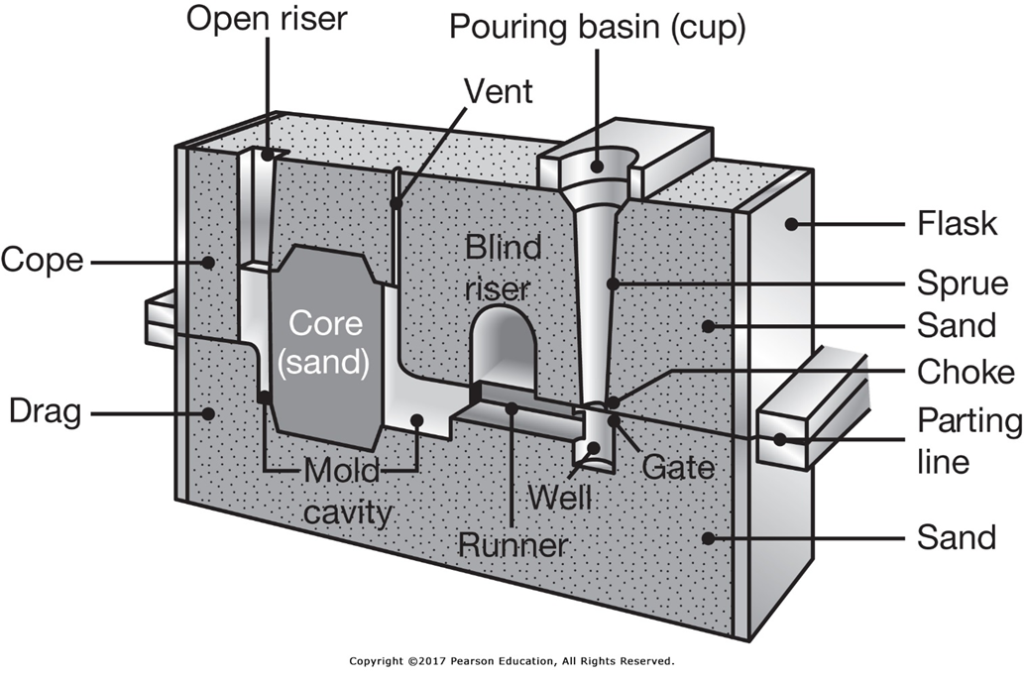
What are the parts of sand cast part?
The parts of a sand cast part are:
- Casting
- Top Riser
- Gate
- Side Riser
- runner
- well
- sprue
- pouring cup/basin
All risers are waste metal that is separated from the casting and will be re-melted to make more castings. To minimize waste in the unit operation, it is desirable for the volume of metal in the riser to be a minimized.
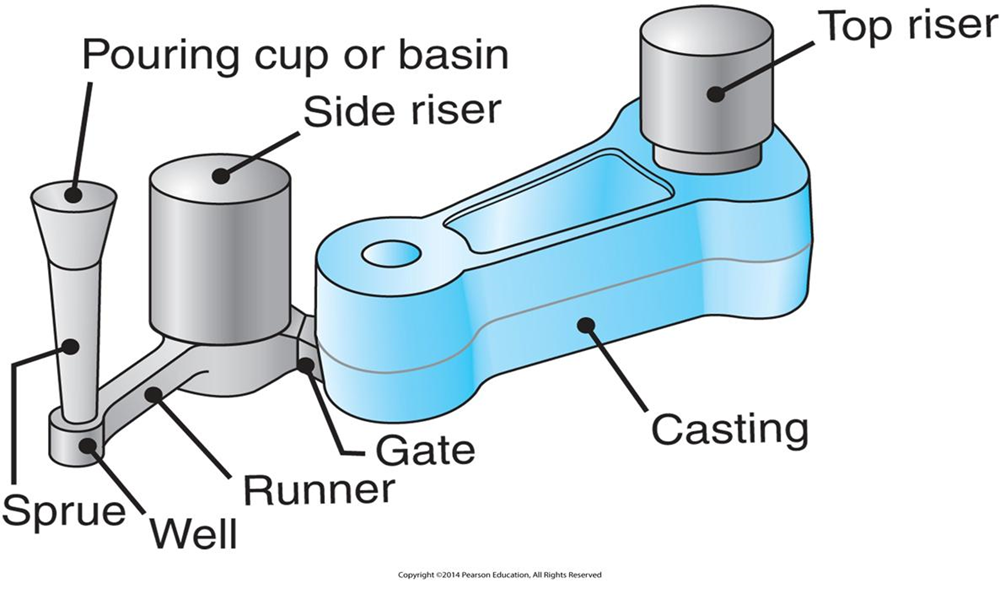
What is sand casting? List limitations, advantages, and disadvantages.
Sand casting is the most widely used casting process. This is a casting process in which sand is used as the mold material. During sand, casting metals are superheated and then poured into a mold that has the desired shape cavity to cool down and solidify.
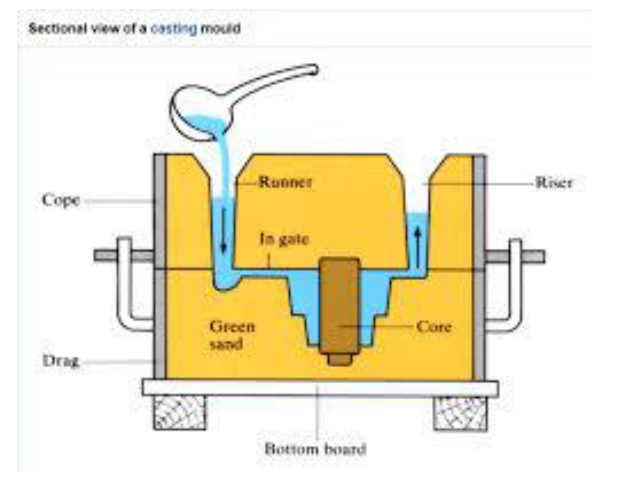
- Advantages:
- Nearly all cast alloys can be poured into sand molds
- Most metals/ metal alloys can be cast using sand casting
- (Design Flexibility) size and weight of the material can range widely.
- Able to cast complex shapes
- (Low tooling cost) tooling cost is much lower than other forms of casting
- Short lead times
- Nearly all cast alloys can be poured into sand molds
- Disadvantages:
- (Poor surface finish) due to sand wall surface texture
- (Low dimensional accuracy) because of solidification shrinkage and surface finish
- Unavoidable defects
- Low material strength due to high porosity
- Secondary machining operations are usually required if a better surface finish or tighter tolerances are required.
What is shell molding? List limitations, advantages, and disadvantages.
This is an expendable mold casting process, which uses resin-covered sand to create the mold. In this casting process, both ferrous and non-ferrous materials can be cast using shell casting. Compared to sand casting this casting process has lower labor costs associated with it in addition to higher productivity and dimensional accuracy.

- Advantages:
- (high-accuracy rough castings) More dimensional accuracy compared to sand casting which reduces post-processing machining costs.
- (good surface quality) It can produce very smooth surfaces
- No gas inclusion occurred because of the high permeability of the shell
- Thin wall thickness and complex castings
- Less manpower and molding skill requirements
- Disadvantages:
- Economical only for mass production
- It cannot produce complicated shapes
- Production cost is high because of pattern cost
What is investment casting? List limitations, advantages, and disadvantages.
Investment casting is also known as lost wax casting and is one of the oldest known metal casting techniques. In this process, molten metal is poured into the cavity created by wax patterns. The metal casting is then removed by breaking the refractory material. This is a precision casting technique as it
can make highly accurate and complex shapes. Like shell casting, both ferrous and non-ferrous materials can be cast using investment casting.
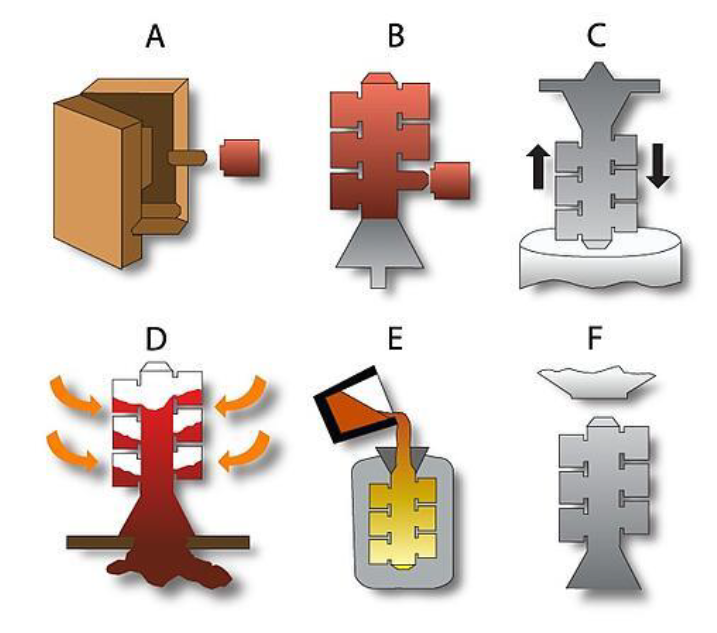
- Advantages:
- Can easily make parts which complex and intricate shapes
- Excellent surface finish can be achieved
- A draft on the wall is not required
- Tight dimensional tolerances
- very low porosity can be achieved
- cores are not needed
- Capability to cast thin walls.
- Low material waste
- Disadvantages:
- It is expensive due to the number of steps required (Labor Cost)
- Individual patterns are required for each casting.
- Limited casting dimensions.
What is a hot chamber die casting? List limitations, advantages, and disadvantages.
Hot chamber casting also known as gooseneck casting is a die-casting process that uses alloys with low melting temperatures. During this process, metals like zinc and magnesium are first superheated. The molten metal is then forced and pressured into a pre-shaped mold through a “gooseneck” metal feed system, while still under pressure the molten metal can cool.
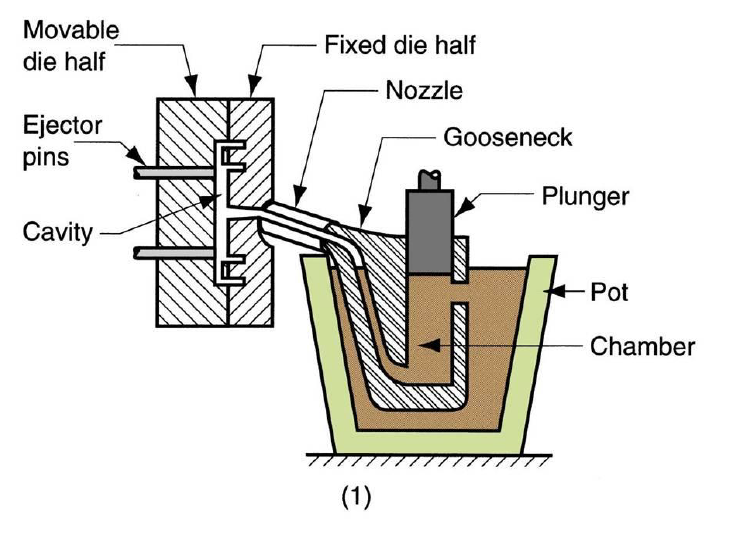
- Advantages:
- Good dimensional accuracy
- Good surface finish
- Economical for mass production
- Fine-grain structure and superior mechanical properties are achieved.
- Fast cycle times
- the convenience of melting the metal directly in the chamber/machine
- Disadvantages:
- It is an expensive process
- The cost of dies and other components is high
- A skilled worker is required
- parts must be symmetric
- small crystals are left behind which negatively affects the elasticity
- This casting process only works with metals that have low melting points
What are the common defects of casting?
In die casting the most common defects are mis-runs, porosity, heat tears, cold shuts, and misalignment. Some of the common causes for these defects are cold dies, low metal temperature, dirty metal, lack of venting, excess lubricant, turbulence during pouring, and misalignment of the cope to drag.
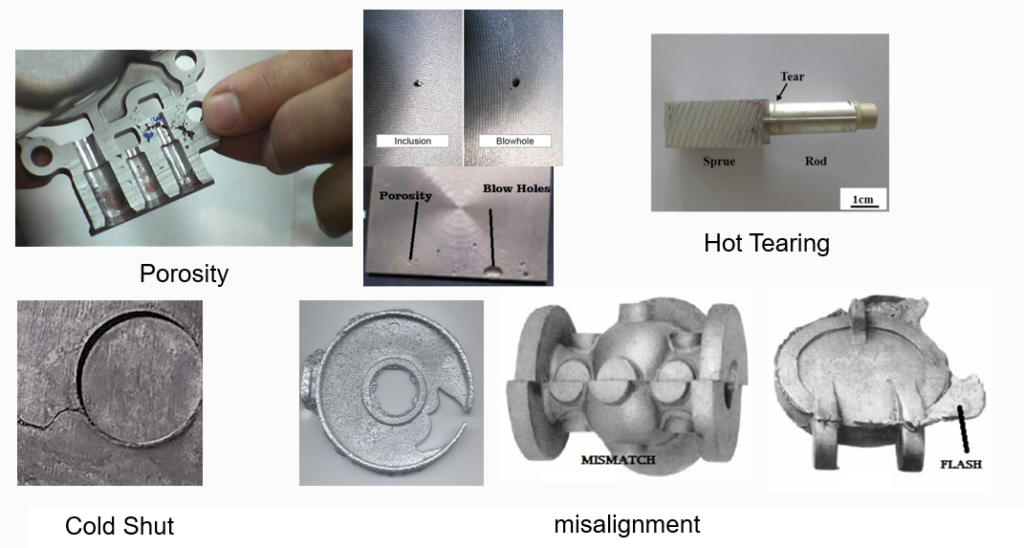
What are the different types of porosity in castings?
Porosity in a die casting occurs during the solidification process. Porosities can be classified as one of the three following types:
- Macroshrinkage
- Gas Porosity results when there is an air pocket that forms because air or gas is entrapped in the metal as it solidifies
- Microshrinkage porosity (microporosity) can be caused by metal shrinking away from thick sections and toward thin sections, leaving voids in the center
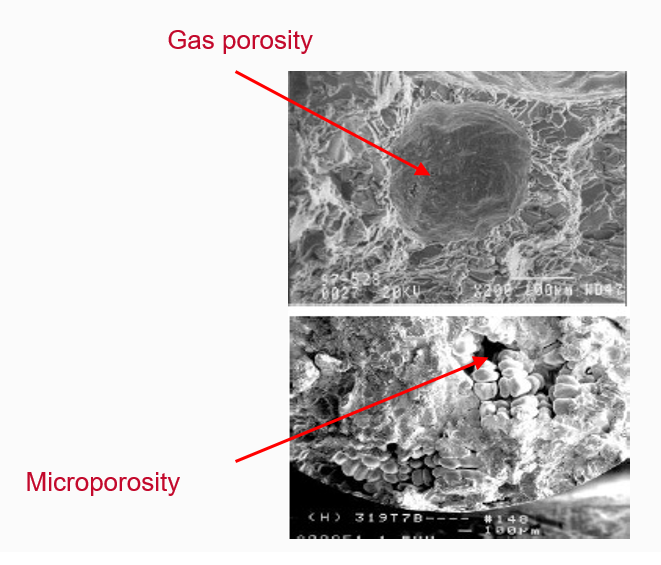
Why chills are used in casting?
Chills are metallic objects used in castings to eliminate porosity caused by shrinkage during the solidification process. If the thickness of the casted part has a varying thickness, the area that is the thickest will take the longest to cool, usually resulting in porosity defects. As a result, chills are strategically placed, at the thickest area of the casting to increase the cooling rate in the area.
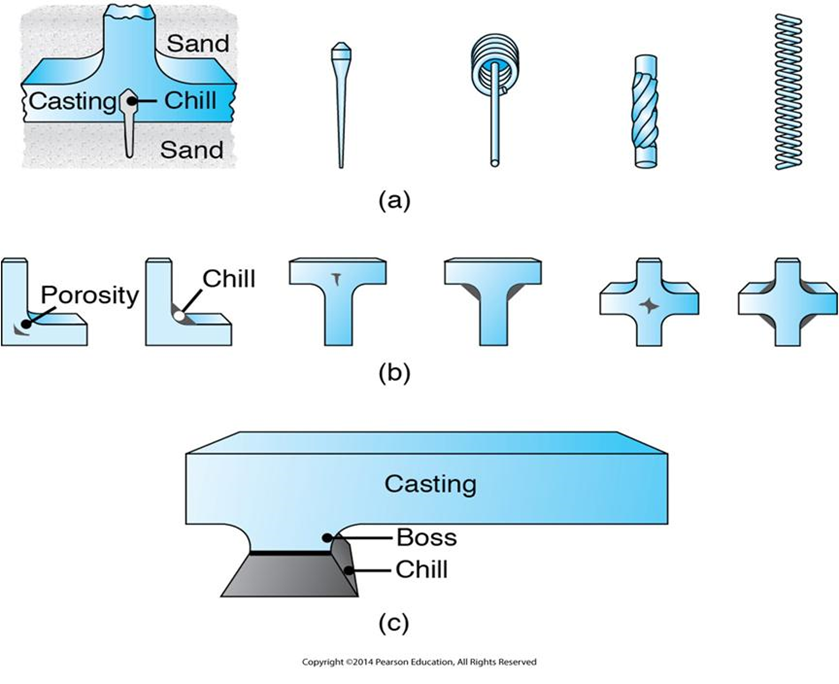