Battery Thermal Management 101
Why are battery thermal management systems important? In the electrifying world of modern technology, where portable gadgets have become an integral part of our daily lives, the role of lithium-ion batteries cannot be overstated. These compact powerhouses efficiently store and release energy, but hidden within their sleek exteriors is a complex interplay of heat and power that requires meticulous understanding.
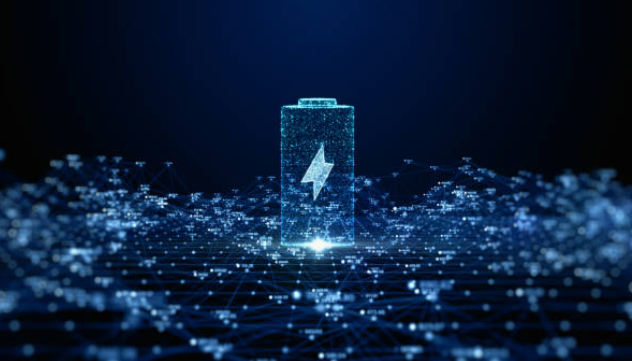
However as the world transitions towards electric vehicles, the need for good battery thermal management is getting more and more attention. Both EV startups like Tesla, Rivian, and Lucid and traditional automotive giants such as Hyundai, Volkswagen, and General Motors are wholeheartedly adopting the EV trend. The primary driving forces behind this shift are climate change concerns and the uncertainty behind conventional fossil fuels, such as gasoline. Nevertheless, a significant challenge in the widespread adoption of EVs lies in effectively addressing thermal management issues.

The electronics industry is no stranger to the problems regarding the accumulation of heat in portable gadgets, with temperature alone being responsible for approximately 42% of all electronic malfunctions. The Samsung Galaxy Note7 is still banned from airplanes due to the risk of fires and explosions. However, the size of the battery is much larger in an EV compared to a smart device thus magnifying the necessity for excellent battery thermal management. In this article, we embark on a journey into the heart of Li-ion batteries, delving into the fascinating realm of thermal models.
The Consequences of Thermal Runaway in Battery Thermal Management Systems:
Before delving into the complexities of thermal models, let’s first examine the significance of comprehending the thermal behavior of Li-ion batteries. Among the potential pitfalls in battery technology, thermal runaway stands out as a particularly alarming scenario.
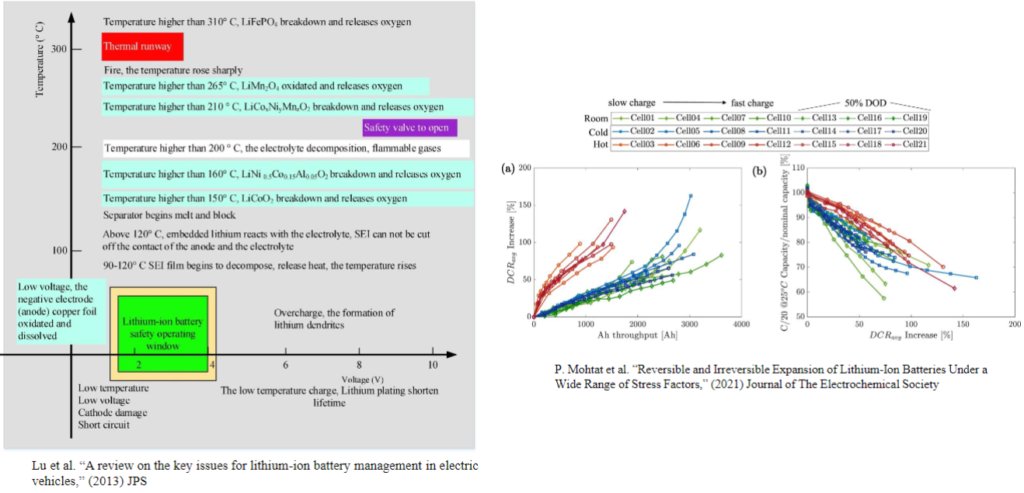
What is a battery thermal Runaway?
A battery thermal runaway occurs when one exothermal process sets off a chain reaction, ultimately leading to an unmanageable rise in temperature. This escalation can lead to the battery’s destruction or, in more severe instances, even a fire. A comprehensive thermal model is the key to preventing such disasters and optimizing battery performance.
Thermal Impact on a Battery Management System
Understanding the thermal impact on the Battery Management System (BMS) is crucial due to its influence on various critical processes. Ion transport, electron transfer, diffusion, heat transfer, mass transfer, mechanical expansion, and chemical reactions within the battery are all temperature-dependent. Failures in inverters and battery chargers often occur due to thermal effects, primarily stemming from mechanical and material issues rather than electrical faults.
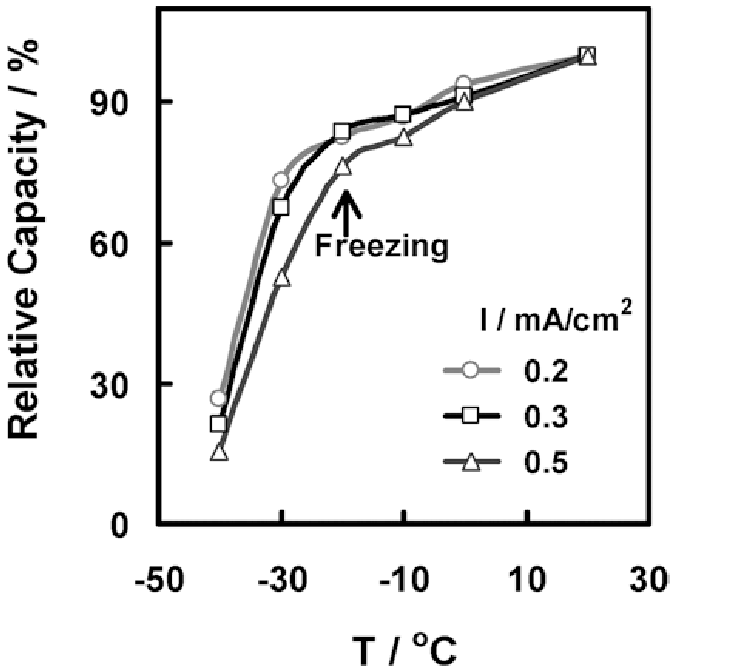
Temperature plays a significant role in every aspect of battery performance, including power and energy availability, system efficiency, charge acceptance, safety, reliability, and overall life cycle and calendar life. Thermal management is essential, particularly in automotive applications, where maintaining a Safe Operating Area (SOA) necessitates effective cooling or heating of an EVs battery.
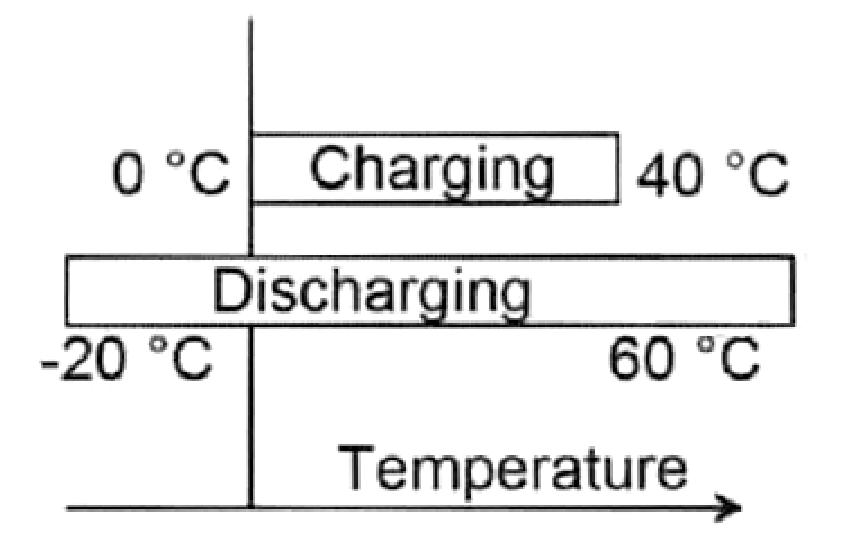
Modeling Approach of a Battery:
To comprehend the thermal behavior of Li-ion batteries, engineers and researchers employ sophisticated modeling techniques. Various approaches for deducing battery parameters include electrochemical methods, mathematical formulations, circuit-oriented techniques, and data-driven analyses.
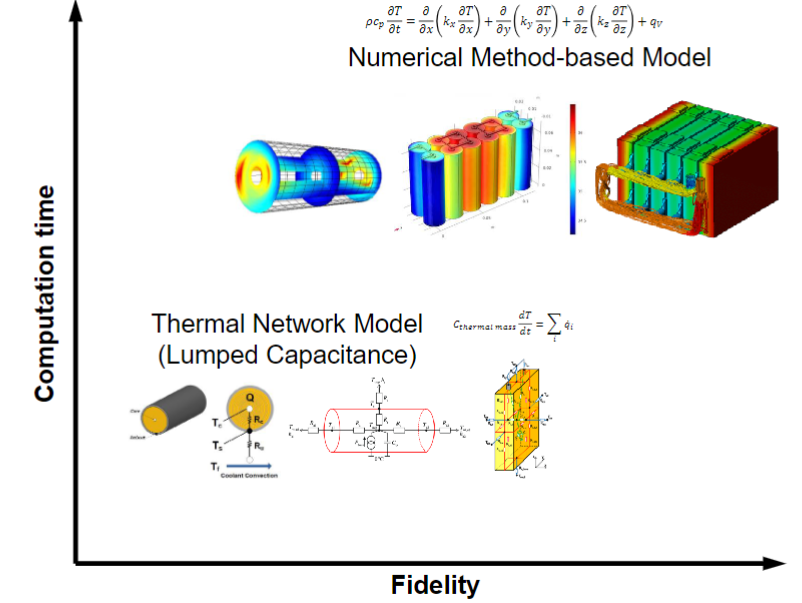
To streamline computations, the SP model was devised specifically for situations involving low-rate charge and discharge. These models simulate the complex interactions between electrical, thermal, and chemical processes within the battery, providing valuable insights for design optimization and safety enhancement.

constant discharge

temperatures matches battery modeling
Battery Thermal Management: Thermal Network Model:
One commonly used approach is the Thermal Network Model, which represents the battery as a network of interconnected thermal elements. The thermal network approach is derived from energy balance
equations.

Each element corresponds to a specific component of the battery, such as the anode, cathode, and electrolyte. By modeling these components individually, engineers can analyze the temperature distribution and heat flow within the battery during operation.
The Importance of Thermal Conductivity in Battery Thermal Management
Thermal conductivity is a material property that defines a material’s capacity to conduct heat. A material with a high thermal conductivity, as seen in most metals, will heat up rapidly compared to a material with low thermal conductivity, such as wood. The unit of measurement for thermal conductivity is W/mK (Watts per meter Kelvin).
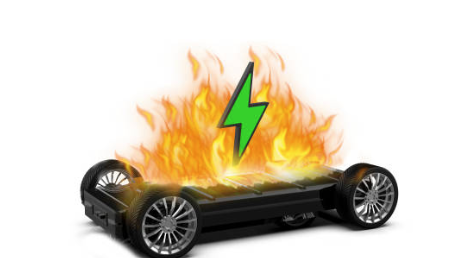
In the context of electric vehicles, thermal conductivity plays a pivotal role in effective thermal management. Materials with high thermal conductivity facilitate the swift dissipation of generated heat from the battery pack. Conversely, materials exhibiting low thermal conductivity can function as thermal barriers, impeding the spread of fires to other parts of the vehicle. Various techniques exist for battery thermal management, with the use of phase change materials becoming increasingly prevalent.
Using Phase Change Material for Battery Thermal Management
The concept of utilizing phase change material (PCM) for the temporary storage of heat energy is firmly established and finds application in various fields, particularly in stationary civil and energy engineering. This principle could potentially aid in minimizing cooling requirements for automotive battery packs and alleviating peak loads, allowing for the implementation of more compact battery thermal management systems. The critical factor for a successful application in the automotive sector lies in the careful selection of material, considering factors such as transition temperature, high specific heat of fusion, and thermal conductivity.

Thermal properties of a batteries
The reaction of batteries to external temperature variations and internal heat generation significantly relies on the thermal material properties of the cells, specifically the specific heat capacity and thermal conductivity.

Obtaining information about these values is crucial for designing an effective battery thermal management system, although it can be challenging to get this information. The precise values for specific cells are strongly influenced by factors like form factor, casing material, and thickness. These values can be derived either through calculations based on individual components and their respective mass fractions or through experimental determination.

In thermal analysis of batteries, capturing the nuances of cell behavior involves using Finite Element Analysis (FEA) to model non-electrochemical hardware. This includes estimating resistances of components based on their geometry and materials. By applying voltage drop, the current density in each component can be calculated, allowing for the estimation of resistive heating (I2R) within the cell.
Additionally, the heat of electrochemical reactions in the core (active parts) is considered. Heat transfer boundary conditions are applied to the cell’s exterior, enabling the prediction of temperature distribution within the cell based on current density and the associated heat generation distribution.
Heat Generation Rate:
Understanding the heat generation rate within a Li-ion battery is paramount for predicting its thermal behavior. The bulk heat generation rate is the product of the current and the difference between the enthalpy potential and the cell voltage:
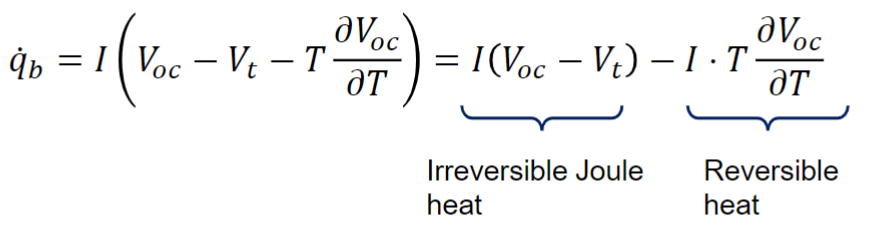
The heat generated results from reversible and irreversible processes during charging and discharging cycles. Reversible heat generation is associated with entropy change during electrochemical reactions, while irreversible heat generation stems from resistive losses and other non-idealities in the battery.
Reversible Heat Generation:
The reversible heat generation in Li-ion batteries is a fascinating aspect that arises from the thermodynamics of electrochemical reactions. As the battery charges and discharges, the chemical reactions occurring at the electrode interfaces contribute to the overall heat exchange. Modeling this reversible heat generation provides valuable information about the efficiency of the battery and its performance under different operating conditions. The entropy change can be determined by monitoring OCV while changing temperature.
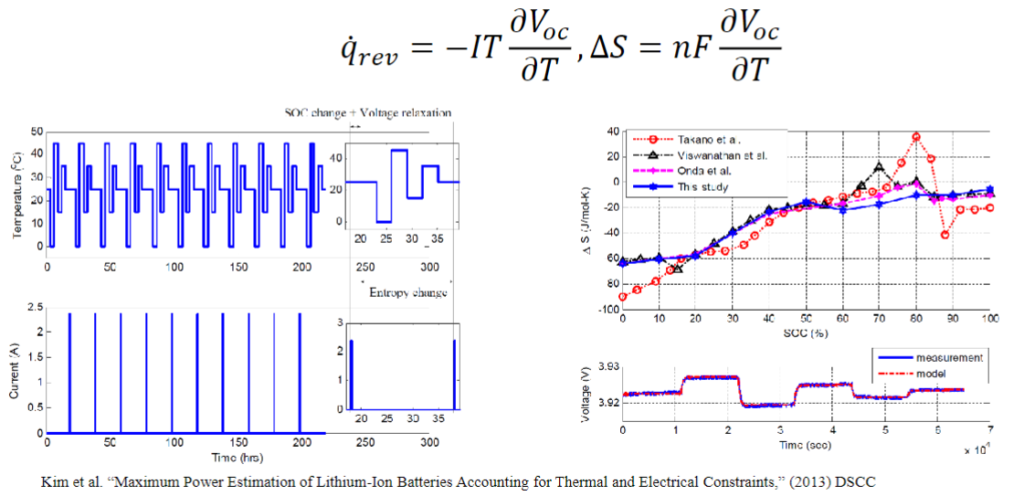
The entropy change can significantly influence heat generation in EV or PHEV applications.
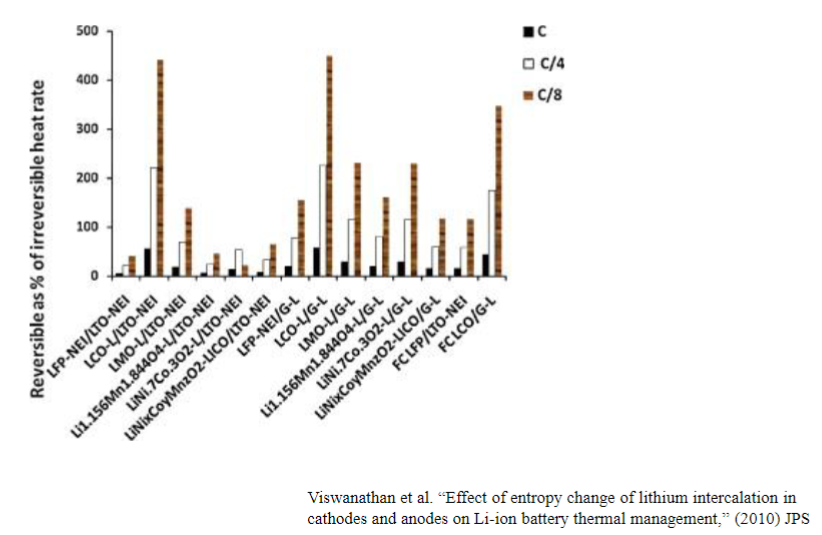
Heat Transfer: Conduction and Convection:
To predict the actual temperature increase of a cell under a specific load scenario, a simplified heat balance between the cell and its environment can be constructed. This entails taking into account all pertinent heat sources and sinks. Heat transfer within a Li-ion battery occurs through two main methods: conduction and convection.
Heat Transfer: Conduction
In battery packs, individual cells are interconnected through a mechanical casing and linked by current collectors, resulting in thermal flux through conduction. While it generally has a minor role during regular operations, this aspect can become influential in extreme ambient conditions, such as cold winter operations. Heat transfer rate via conduction occurs in plane walls of the battery, such as electrodes and separator. Thermal resistance depends on geometry (𝐿/𝐴), and thermal conductivity (𝑘).
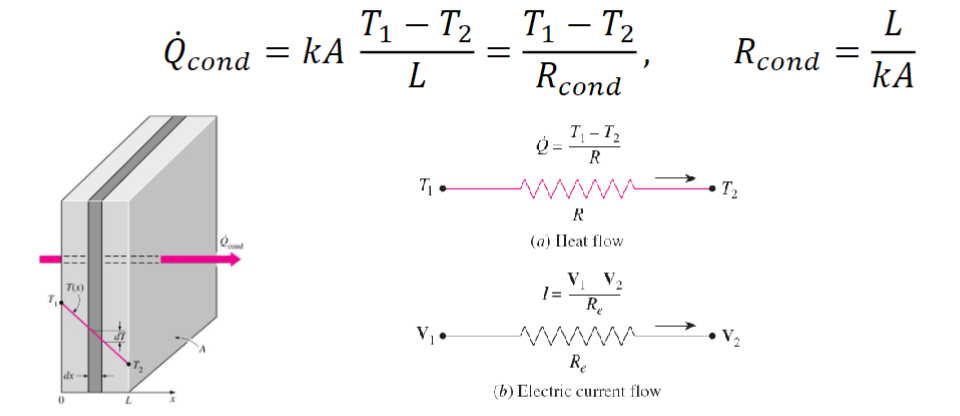
Heat Transfer: Convection
The majority of battery thermal management systems for commercial batteries depend on convection for controlled heat dissipation. The distinction between forced or natural convection is based on whether the surrounding medium is actively propelled. The cooling or heating effect is achieved using gaseous or liquid media, such as air or water. The quantity of heat transferable through convection is contingent on factors such as the temperature differential, the heat capacity of the medium, flow velocity, media viscosity, contact area (A), and numerous other contributing factors.
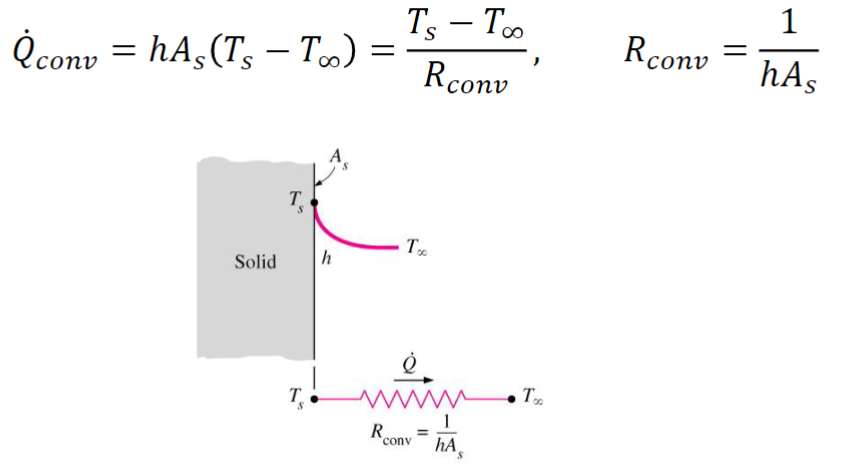
Effective modeling of these heat transfer mechanisms is crucial for optimizing thermal management strategies.
Thermal Resistance Network:
A key concept in Li-ion battery thermal modeling is the thermal resistance network, which quantifies the resistance to heat flow through different battery components. This network allows engineers to identify potential hotspots and optimize the design to ensure uniform temperature distribution. By minimizing thermal resistance, the risk of thermal runaway can be mitigated, enhancing both safety and performance.
The thermal resistance is characterized by the ratio of the temperature difference (dT) to the heat transfer (Q). This concept bears resemblance to Ohm’s law, where electrical resistance is determined by the ratio of the voltage drop across a resistor to the current flowing through the resistor.
Serial configuration Example

Parallel configuration Example

Parallel + serial configuration Example
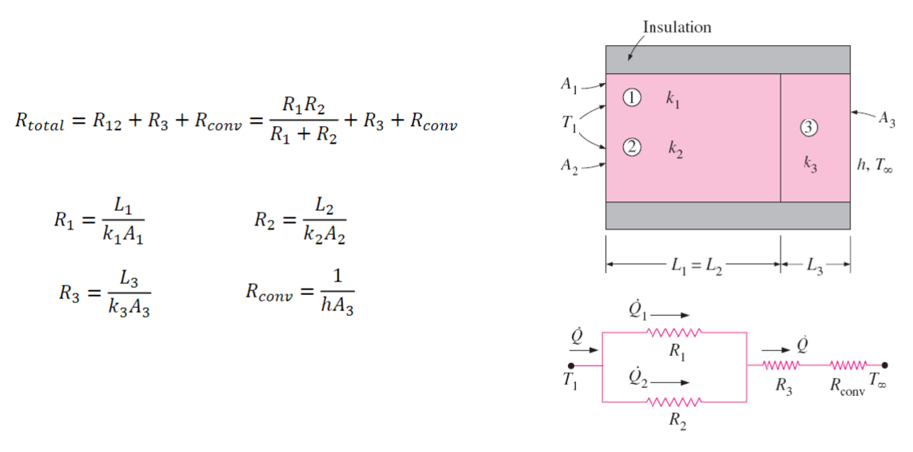
Indirect liquid-cooled systems for Battery Thermal Management
Leveraging the cooling system currently already used by numerous vehicles, an indirect liquid cooling system is also applicable for regulating battery temperature. In this system, a liquid coolant circulates between the battery pack and a heat sink. The cells do not come into direct contact with the coolant but are connected to the coolant circuit through conductive materials, such as aluminum.
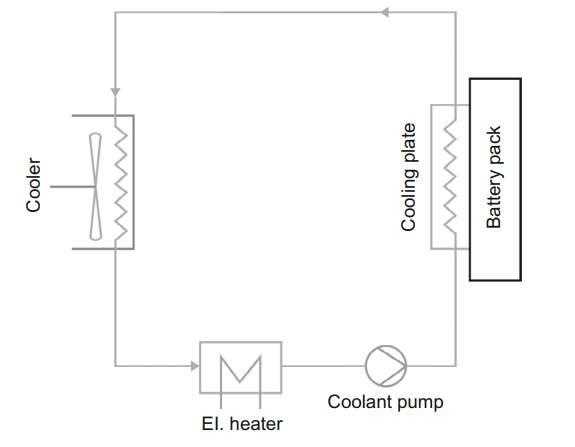
Depending on ambient temperatures and power requirements, the heat sink can be a straightforward radiator or an evaporator integrated into a refrigerant cycle. The most versatile systems incorporate both circuits and dynamically switch between them, utilizing the air cooler for standard operation and the chiller exclusively during peak loads or high ambient temperatures. Such systems are used in by companies such as Chevrolet and Tesla.
Example: Chevrolet Bolt
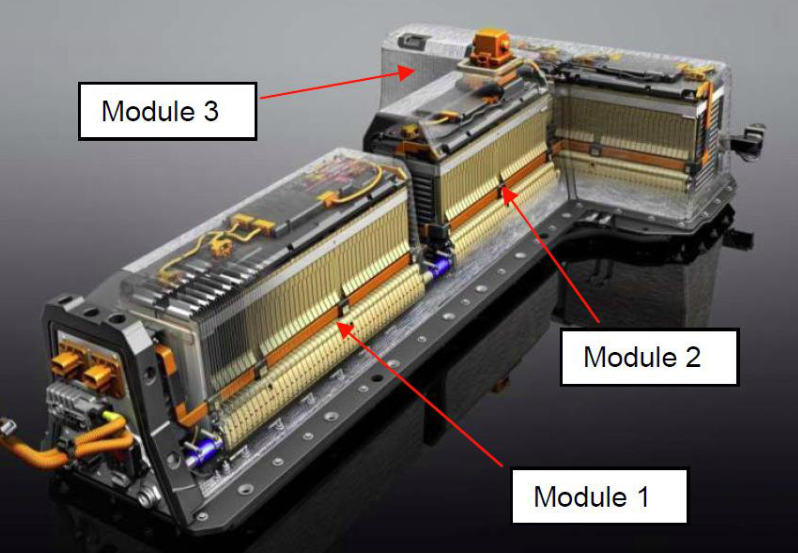

The Chevrolet Volt battery pack features a distinctive T-shape design, housing 288 LG “P1” flexible pouch cells. Each cell measures 13 x 18 x 0.64 cm and contains 17 negative electrodes made of carbon-coated copper and 16 positive electrodes coated with lithium manganese oxide. The cells use lithium hexafluorophosphate (LiPF6) dissolved in a carbonate solution as the electrolyte.
The battery pack includes circuit boards known as “Voltage Temperature Submodules (VTSMs),” positioned atop each module. To regulate temperature, cooling fins are integrated within the battery stack, with one side of each cell pouch in contact with a cooled plate. A glycol/water coolant circulates through the system, capable of both cooling and heating as needed.

Battery Thermal Management: Liquid Cooling Tube
The Liquid Cooling Tube, also referred to as liquid-cooling tubing or serpentine tubing, is crafted from thermally conductive metals, commonly copper or aluminum alloys. These metals undergo extrusion and corrugation to form an internal structure featuring a specific number of channels closely aligned with the surface of the battery cells. This serpentine tubing serves as a crucial component in indirect liquid cooling systems, functioning as a heat exchanger. The circulation of coolant within the channels facilitates the dissipation of heat generated.
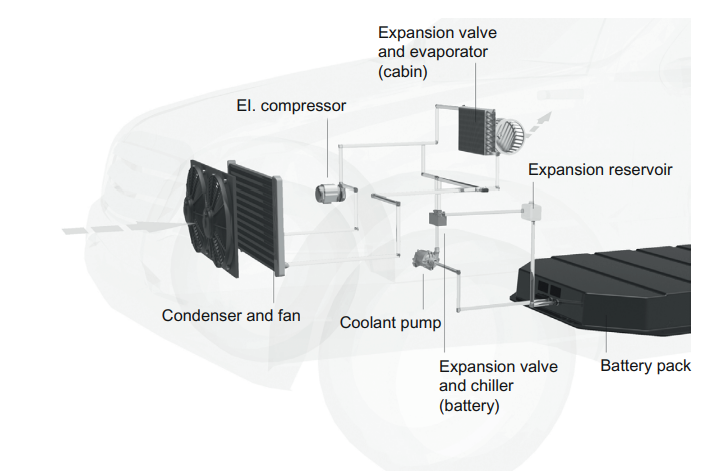
Typically, one to two rows of battery cells are positioned between each pair of serpentine flat tubes. This design effectively expands the heat exchange area on the battery’s side, resulting in a more uniform temperature distribution among individual cells during operation. Consequently, it helps minimize the temperature difference across the entire battery pack.
Conclusion:
As we navigate the intricate world of Li-ion battery thermal models, we uncover the critical role they play in ensuring the safety and efficiency of these ubiquitous power sources. From the consequences of thermal runaway to the intricacies of heat generation, heat transfer, and thermal resistance, every aspect of the model contributes to a deeper understanding of battery behavior. The journey into the heart of Li-ion batteries’ thermal models is not only an exploration of technology but also a commitment to the safe and sustainable future of energy storage.
References:
C. Huber, R. Kuhn, 13 – Thermal management of batteries for electric vehicles, Editor(s): Bruno Scrosati, Jürgen Garche, Werner Tillmetz, In Woodhead Publishing Series in Energy, Advances in Battery Technologies for Electric Vehicles, Woodhead Publishing, 2015, https://doi.org/10.1016/B978-1-78242-377-5.00013-3