Design of a suspension system
What are the types of suspension system?
In the automotive industry the most common types of suspension systems are the leaf springs, coil springs, torsion bars, and air springs. Of these 4 the most common in today’s automobile industry is the coil spring suspension system such as the MacPherson strut suspension system. Air spring are starting to pick up popularity especially in more expensive vehicles for the enhance drive comfort and driving performance they provide.
What is the function of a suspension system
The goal of a vehicle suspension system is to allow each wheel to maximize ride quality while constraining its movement in other directions to maintain stability and control. The suspension system does this by absorbing the energy from the tires and strategically rereouting it to body and frame of the car to remain stable. The suspension is designed to keep all four wheels as nearly upright as possible at all times, not only when traveling across uneven surfaces but also when experiencing roll moments during cornering. Jounce is the upward suspension travel (compressing of the spring and shock absorber). Rebound is the downward suspension travel (extension of spring and shock absorber).

What are the functions of a suspension system?
- Support vehicle weight.
- Keep the tires in contact with the road, especially important during cornering and while traveling over uneven surfaces.
- Control the vehicle’s direction of travel.
- Maintain correct wheel alignment, important in vehicle handling.
- Reduce the effect of shock loads with the use of springs, dampers, and bushings.
- Maintain correct vehicle ride height.

What are the components of a suspension system?
A suspension system can be broken down into three major subsystems, stabilizing bar, strut assembly, and knuckle and control arms assembly, each sub-system can be broken into sub-assemblies or components as shown below.
- The stabilizing bar sub-assembly main function is to reduce the vehicle’s body roll. The main component of this sub-assembly would be the sway bar which acts as a torsion bar.
- The strut assembly’s main function is to maximize vehicle ride quality and comfort. It does this by reducing vertical acceleration to the cabin of the vehicle. The main components of this sub-assembly are the coil spring and the shock absorber or strut.
- The knuckle and control arm sub-assembly main function is to enable steering. The other key function of this sub-assembly is to allow the chassis and wheels to move together while the car is moving.
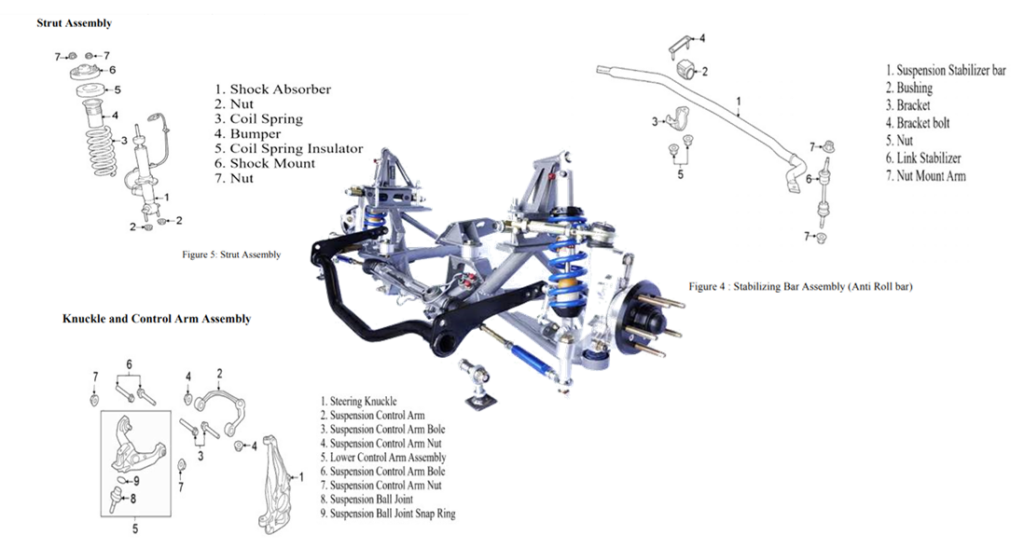
Decomposition Tree – Suspension System
To see how a suspension system interacts with the rest of the vehicle, a decomposition tree can be constructed. A “Decomposition is a useful step in managing larger systems in the product development process. The product can be decomposed into many systems, systems into subsystems, and subsystems into components. The decomposition of the product into its lower-level entities also requires a careful cascading of attribute requirements from the product level to lower-level entities. It should be noted that each lower-level entity exists to serve at least one or more functions necessary for the product to meet its requirements.” [1]
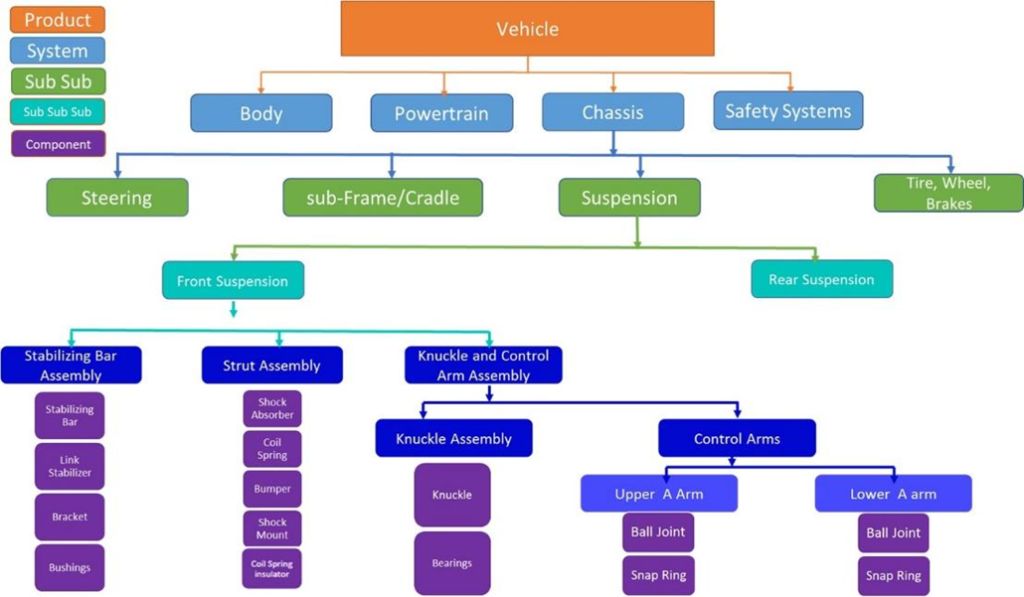
Evaluation of the suspension system
In order to have a successful product in the market you must address all of the customer needs. Customer needs are mainly obtained by clinics and surveys. For this project, the team created a survey to understand the needs of our customers. A total of 68 potential customers were surveyed to understand what their biggest concerns and needs were with regard to a suspension system. Below are summaries of the voice of the customer.


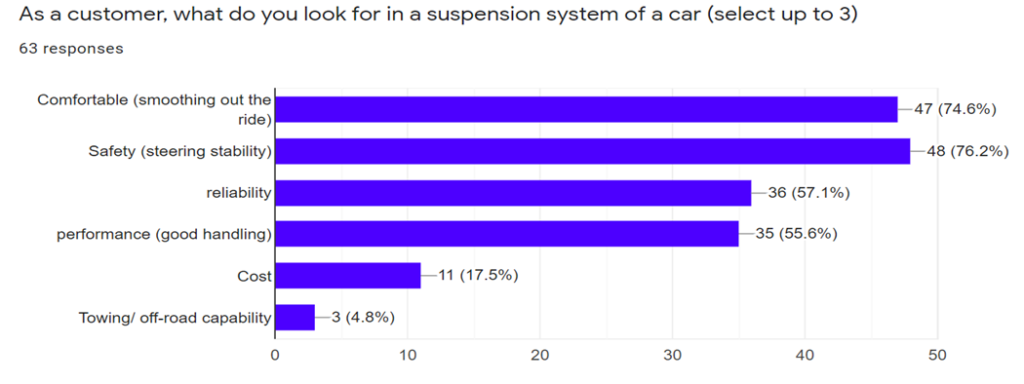
What are the customer needs of a suspension system?
Customer needs cannot directly be used to design a product. Each customer needs to be associated with a functional target, some of the needs will have a strong relationship with engineering requirements and some others will have a low impact or even zero impact.
What are the requirements of good suspension system?
The first step to building a QFD for a suspension system is to list the main customer needs and define the weight of each of those: 5 to the most important and 1 to the less important.
Comfortable: Customer are looking for a smooth ride and looking for the suspension system to absorb any type of bumps. They want the suspension system to be quite and to enable to vehicle to feel quick on its feet.
Safety: Customers have a expectation that the suspension system will not fail when braking and will allow the weight of the vehicle to transfer correctly in sharp corners.
Performance: Customers are looking for a vehicle that is enjoyable to drive without sacrificing comfort. The suspension system should also be reliable regardless of the road conditions and the weather.
Reliable: Customer expectation is that the suspension system will require the minimum service.
Cost: The cost of the services and maintenance of suspension systems needs to be low and affordable.

Function Requirements for a suspension system

Engineering requirements are listed at the top of the quality house; for each requirement, it is important to assign a direction of improvement for the new system. For the 2026 MY Toyota Sequoia we will focus on improving the suspension travel for a better ride and each of the components related to safety and durability. The customers’ voices let us know that the main requirement is to have a safe and durable suspension system.
Cost: Cost needs to be taken into consideration at all times when designing components, the selection of materials and how they are assembled could have a negative or positive impact on the final cost of the product. This must all be done while still maintaining a high quality of the suspension.
Torque steer & handling: customer needs calls for performance and comfort in the suspension system. In order to provide a good driving experience, the components and characteristics that have the biggest influence are wheel size, ground clearance, shock absorbers, and struts, roll center height, and geometry packaging.
Safety: Each component and system will have an effect on the overall vehicle. For this project, we will focus on optimizing the brake size, the off-road tire tread, and the ABS Sensors.
Durability: In order to provide a cost-effective and reliable suspension system we need to consider the best materials for the application as well as the type of coating given the different weathers and terrains that the vehicle will be exposed to.
Load Leveling: Full-size SUVs are mainly used to tow big loads as well as long trips, spring sizes will play a significant role in this requirement. There are 4 parameters which automotive engineers can play with when designing a spring.
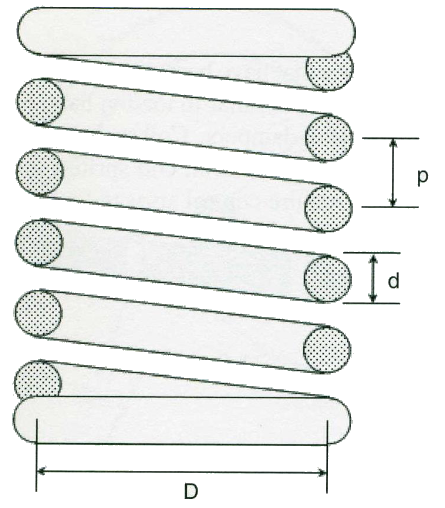
- Mean coil diameter, D: the center-to-center distance of the wire across the coil
- Wire diameter, d
- Pitch, p: the distance between successive coils on an uncompressed spring
- Active coils: the number of coils not touching the support
QFD Complete
Once the functional requirements and customer needs are defined, we can compare our product with the main competitors. In the horizontal plane, we will grade each vehicle based on the customer reviews, while the vertical plane considers the specific functions.
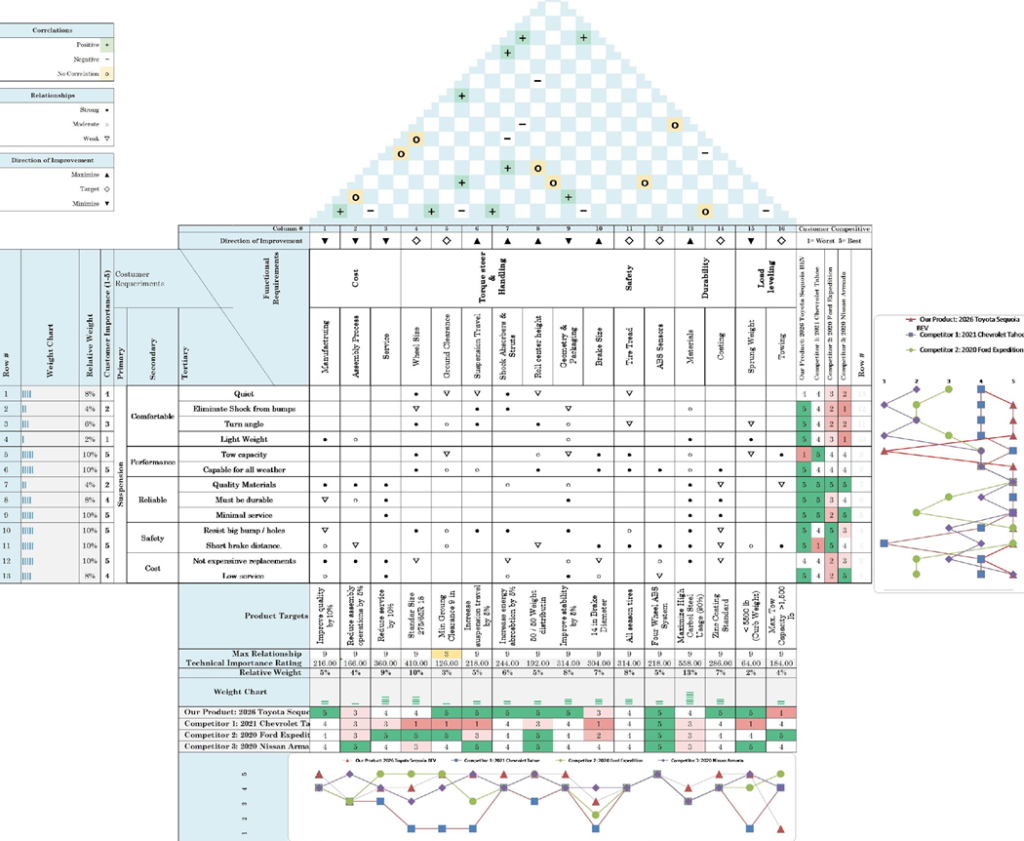
QFD Results and Observations.
Based on this exercise we can determine that the main three functional specifications to achieve our customer needs are: Material selection, wheel Size, and service. Material selection has a strong relationship with cost, durability, and cost, the three main concerns of our customers also; material selection is one of the unique requirements that have a relationship with all the customer needs. Packaging the correct wheel size will determine the performance of our vehicle as well as the comfort.
The next requirements are the ones that scored the lowest in the exercise and have the least impact on the customer’s needs: Sprung weight, Assembly Process, and Towing. While towing is one of the main reasons why someone will buy a Large SUV it will not have the biggest impact on the suspension performance, however, is still a requirement that needs to be considered while designing the vehicle.
Requirements Cascade Table
The next table illustrates how the vehicle requirements are cascaded into requirements for the suspension system. The first column presents the vehicle attributes, and the second and third sub-attributes. Columns 4 to 9 present requirements for the suspension system. The requirements of the suspension system are developed to meet the sub-attributes requirements listed in each row. For this exercise, columns 8 and 9 are subsystems that may not be a part of the suspension system itself but are components and subsystems that have a big influence on their design and performance.
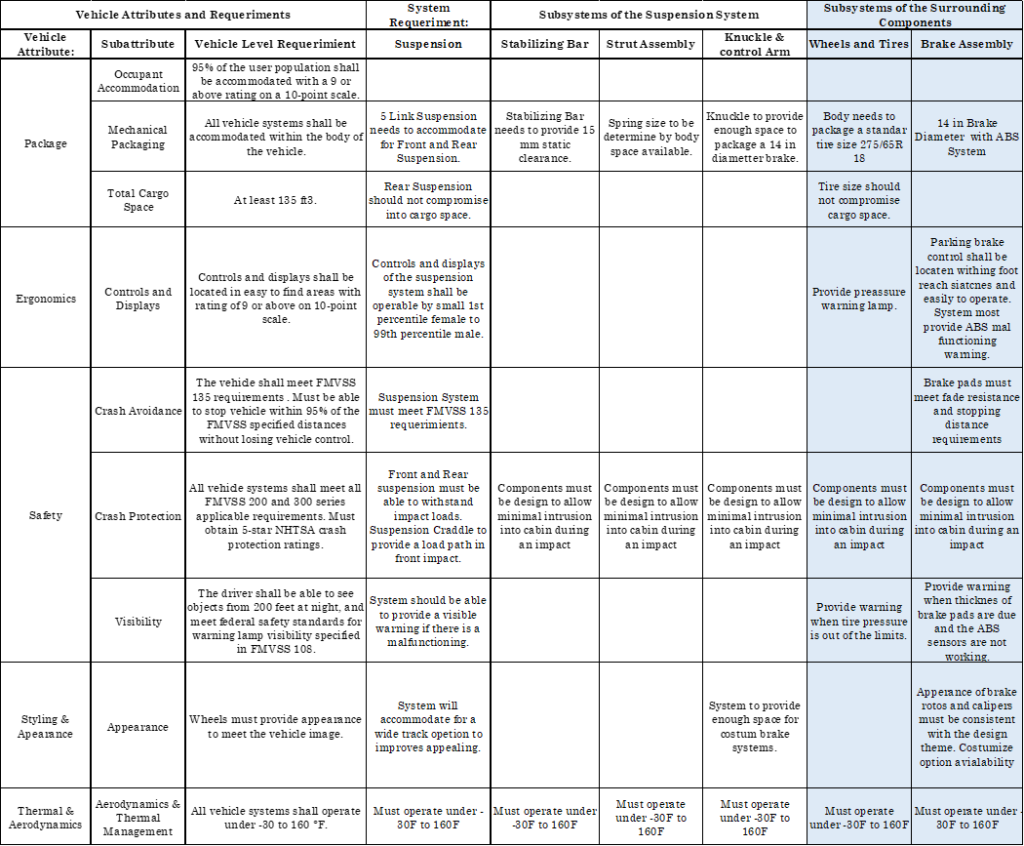

Interface Diagram for a front suspension system
Using an interface diagram allows a complex system with multiple components to be simplified and broken down into a flowchart that helps visualize how various systems, subsystems, and components interface with each other. There are many potential interfaces and for the interface diagram below the following naming convention was used: Functional [F], Physical [P], Spatial [S], Material Flow [M], and Information Flow [I].
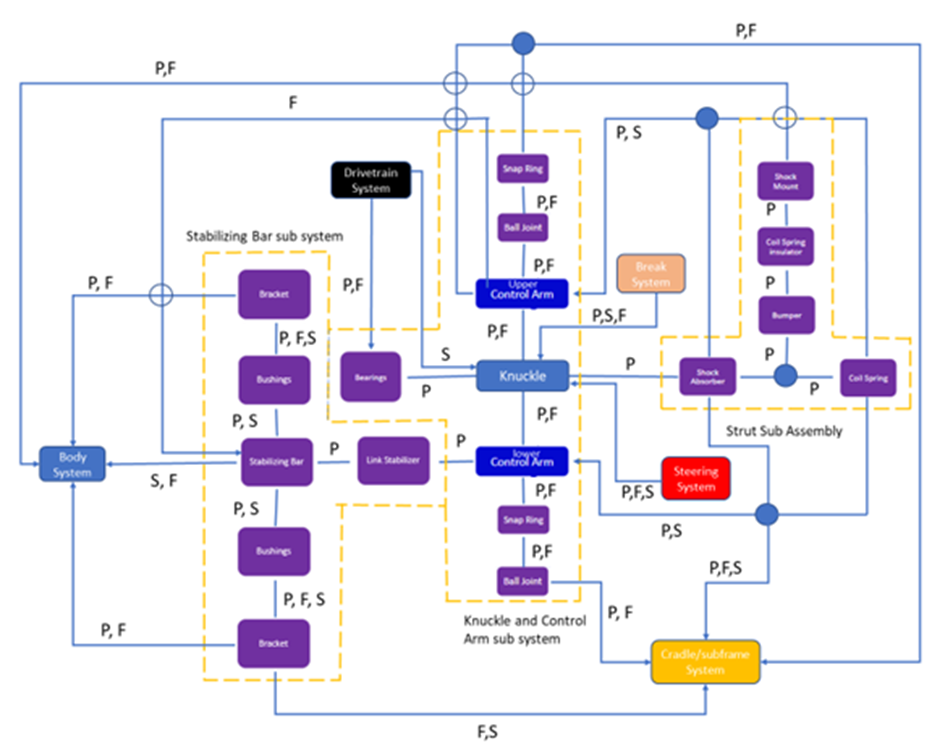
Interface Matrix for a front suspension system
The interface matrix shows how the components in each subsystem of the rear suspension interact with each other. The relationships are described between the components with the following descriptions: physical interface (P), spatial-packaging interface (S), electrical interface (E), material flow (M), information flow (I), functional interface (F), and no relationship (0).


Interface Requirements
There are multiple requirements for the interfacing of the suspension subsystems that must be met in order to ensure a quality build and optimal performance. These will vary based on the type of interface as well as other general requirements for the proper function of each subsystem. The requirements are listed in the chart below.
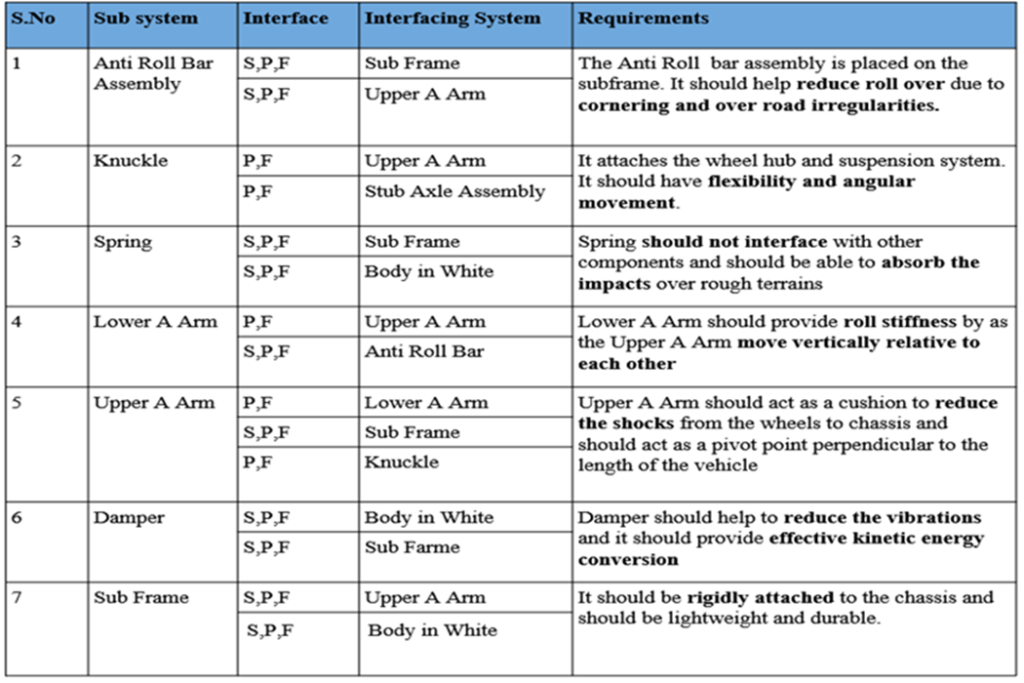
Trade-Offs when designing a suspension system
A few design trade-offs were noted during the analysis of the suspension system.
- The suspension system must be able to interface with the body, so the mass of the vehicle is properly sprung. However, the body must also be designed to fit other vital components such as motors, circuits, wires, seats, etc. This will all limit room for the suspension, which will affect the overall design of the suspension system.
- The durability and materials used to construct the suspension system will be limited by the weight of the suspension. Adding more/heavier materials will add to the overall weight of the vehicle, which will impact both performance and mileage.
- The cost of the materials and components must be considered. Lightweight and high-strength materials are expensive, and some corners will likely need to be cut to save costs.
- The size of the tires, as well as the design and materials of the tires, will influence the suspension design. Not only will the suspension need to be set up for the proper size of tires, but the tires will also have their own spring constant alongside the springs in the suspension. This will likely affect what kind of springs will need to go into the suspension. Below are the 4 different types of coil springs commonly found in automobiles.
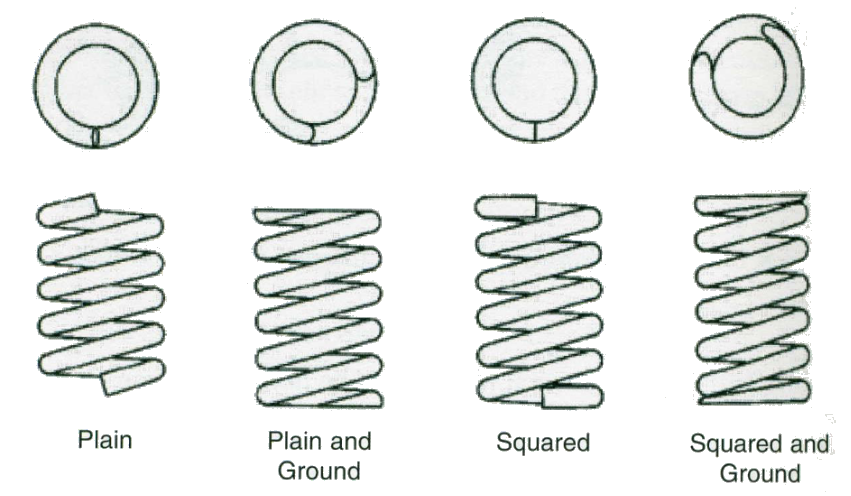
Observations and Insights
One of the most notable things we noticed during our study of the suspension system was how integral it is to the overall build of the vehicle. The system must interface with numerous other systems, notably the body, frame, and brake systems, so as to keep the vehicle stable and properly suspended from the ground during vehicle operation. In addition, we gained a lot of insights into our customers’ needs thanks to the market survey we created. The fact that we were able to get a large number of results from a broad age demographic allowed us to determine what our philosophy should be when designing the suspension system for the vehicle. This was also helpful in designing the requirements cascade, showing us the targets we need the vehicle to meet.
References
- Automotive Product Development: A Systems Engineering Implementation, by Vivek D. Bhise. ISBN: 978-1-4987-0681-0. Publisher: CRC Press, Boca Raton, FL: CRC Press, 2017. (APD)
- Goodarzi, Avesta, and Amir Khajepour. Vehicle Suspension System Technology and Design. vol. 2, Morgan & Claypool Publishers, San Rafael, California, 2017.
- Liu, Honghai, et al. Handbook of Vehicle Suspension Control Systems. vol. 92, The Institution of Engineering and Technology, Stevenage, 2013.
- https://www.svtperformance.com/threads/griggs-sla-front-suspension-anyone-install-this-kit.1151345/ Accessed October 08,2020