How are leaf springs designed?
A leaf spring is a basic type of spring often used for suspension in vehicles. Originally known as a laminated or carriage spring, and sometimes called a semi-elliptical spring, elliptical spring, or cart spring, leaf springs are one of the oldest forms of vehicle suspension. A Leaf spring consists of one or more narrow, curved, thin plates that are connected to the axle and chassis in a way that allows the spring to bend vertically in response to bumps or uneven road surfaces. The most common arrangement is lateral leaf springs, which run along the length of the vehicle and are mounted perpendicular to the wheel axle.
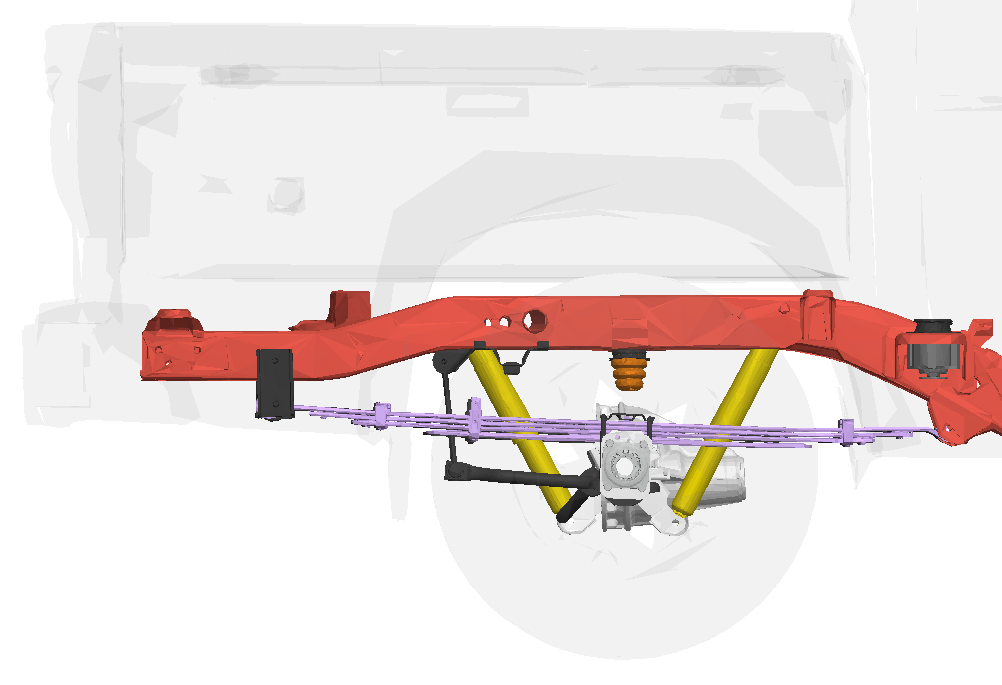
Leaf springs can perform several suspension functions, including supporting the vehicle’s weight, providing springiness, and to some extent, damping by using friction between the layers of the spring.
Just like any other component in a vehicle, leaf springs need to be replaced from time to time. There are multiple reasons why leaf springs might become defective, such as sagging, cracking, breaking, and leaning.
Leaf Spring History
The Leaf spring is the oldest type of automotive spring. They have a long history, initially appearing on carriages in France in the mid-17th century and later spreading to England and Germany by around 1750. Dr. Richard Lovell Edgeworth’s demonstrations in 1768 highlighted the superiority of sprung carriages, leading to leaf springs becoming a regular feature in the late 18th-century carriage industry. The latter half of the 19th century saw developments in steel rolling processes and alloys, making leaf spring manufacture more consistent and cost-effective.
While leaf springs were once common in automobiles, their use declined in the 1970s with the shift to front-wheel drive and coil spring-based suspension systems. However, they remain prevalent in heavy commercial vehicles, SUVs, and railway carriages due to their ability to spread loads widely over a chassis and simplify rear axle location without the need for additional components like trailing arms and Panhard rods.
How many types of leaf springs are there?
There are two types of leaf spring suspensions: mono and multi. Mono-leaf spring suspension is made up of a single piece of metal or leaf. while multi-leaf spring suspensions are made up of multiple leaves. The springs in a multi-leaf spring suspension can be oriented in either a symmetrical or unsymmetrical stack-up.
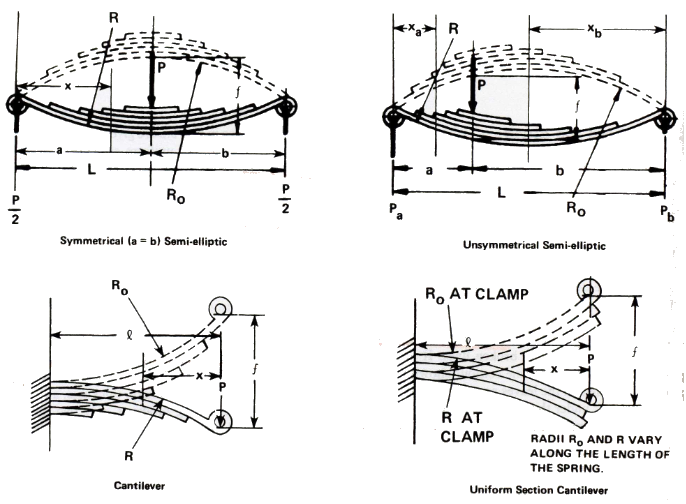
What do leaf springs do?
A Leaf spring is part of a vehicle’s suspension system and must support the entire weight of a vehicle. The automotive industry has been going away from leaf springs in recent years, however, they can still be found on the rear suspension system of many trucks or large SUVs. The main function of leaf springs is to provide comfort to the passengers by minimizing the vertical vibration caused by the nonuniformity of road geometry. Leaf springs also help to maintain the tire’s grip on the road and regulate the wheelbase lengths when it is speeding up or slowing down.

Where the leaf spring sits on an axle, it should be as close to the center line of the axle as possible. As the spring seat moves further away from the center line of the axle, there is an increase in axle wind-up. This is because, as the fulcrum (the point on which a lever rests or is supported and on which it pivots.) lever gets longer, it makes twisting the axle easier.
Are leaf springs better than coil springs?
Leaf springs are much sturdier when compared to coil springs. As a result, they are capable of handling higher loads with less deflection. Leaf springs are also better at spreading out the load over a larger area, whereas coil springs transfer it to a single point. That is the reason why many trucks still use leaf springs for the rear suspension system. However, this increased load-carrying capacity comes at the expense of vehicle ride comfort. The reason for the decreased ride comfort is because of the inter-leaf friction between each leaf. However, this friction is not always well controlled, leading to stickiness and irregular movements in the suspension. To address this issue, some manufacturers use mono-leaf springs.
Why leaf springs are not used in cars?
The biggest reason leaf springs are not used in cars is that they do not offer as much flexibility as coil springs. As a result, a vehicle that uses leaf springs provides a much harder and bumpier ride quality. While off-roading, a leaf spring suspension system is not as accommodating to the uneven ground as compared to a coil system. Leaf springs are still used in large commercial vehicles such as vans, full-size trucks, and SUVs. Outside of the automotive industry, leaf springs are also used by locomotives.
How leaf springs should look?
Leaf springs are primarily used on the rear of a vehicle, virtually no vehicle today uses leaf springs at the front. From a size view leaf springs appear to look like long different sizes of bowed, narrow strips of steel stacked together, which are held together using U-bolts and a center clip. However, upon further examination, the ends of leaf springs can vary from squared-off leaf springs to diamond-pointed leaf springs.

How the leaf spring is attached to the vehicle body and chassis will also vary. Below are some examples of common attachment strategies used in leaf spring designs.

How do you calculate leaf spring forces?
Leaf springs are loaded not only by vertical forces but also by horizontal forces and torques in the longitudinal vertical and transverse vertical planes. Torque in the longitudinal vertical plane (windup) is usually produced by a longitudinal force applied above or below the spring seat. To calculate the number of leaf springs and the size of each leaf spring the following steps can be followed:
- Establish the total moment of inertia for the specified rate and length
- to establish the maximum permissible leaf thickness within the specified maximum stress limit at the corresponding load.
- calculate the spring stress.
- estimate an approximate mass of steel for comparing optional designs from the preliminary calculation.
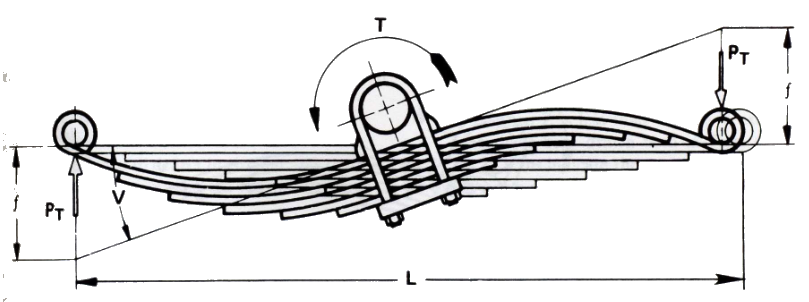
Design a symmetrical semi-elliptic light truck spring with tapered leaf ends to meet the following specifications (rate, as tested with center clamp):

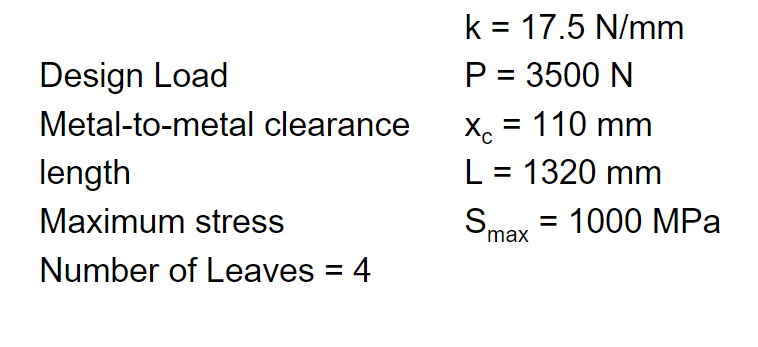
Solution:
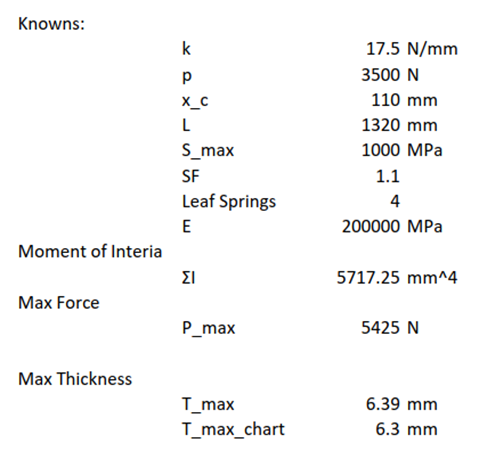
Step 1: Find the required total moment of inertia
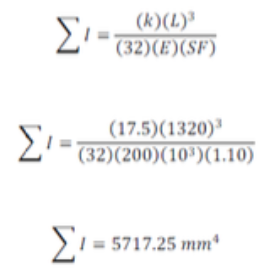
Step 2: Find the maximum permissible leaf thickness

Leaf thickness should not exceed 6.39mm and limited to the total number of leaves 4
Step 3: 5 leaf springs were selected from the spring design manual SAE 1995


Since having 4 common leaf springs would not meet design specifications, springs were mixed and matched to determine the best combination.
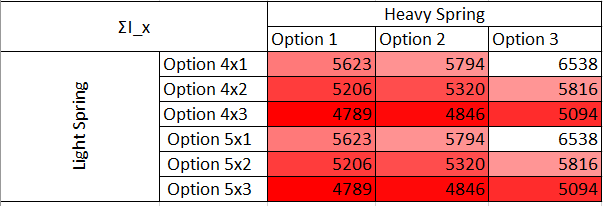
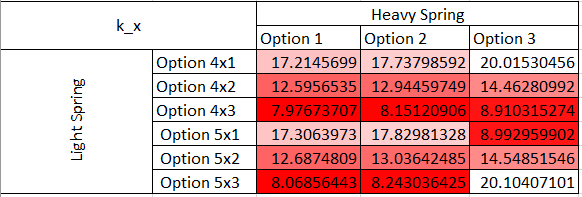
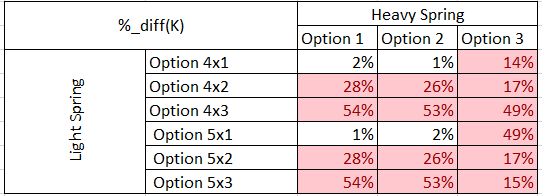
Step 4: Select the top four combinations which are the closest to meeting design specifications:


Option C is the best: it has the lowest mass and the K value is 1% of 17.5N/mm
Option C is 3 leaf springs size 6.3mm x 75mm and 1 leaf spring 6.3mm x 56mm.