How comfortable are your car seats? A review of seat comfort
What is a bucket-style seat?
One of the more important interior components of a vehicle is the seat. The seat is unique because it is one of the 4 components a driver will interact with every time they drive a vehicle. Seats are in constant contact with the user while operating a vehicle, making seat durability and comfort, important features of a seat design. Seats can be designed for different uses and vary widely based on the intended vehicle. The two types of seats found in automobiles are bucket and bench seats. A bucket seat is designed for a single occupant, whereas a bench seat, is designed for numerous occupants. Most vehicles use bucket seats in the first row. A sports car – like the Corvette being a two-seater only offers buckets seats. The characteristic of the bucket seat includes the bolsters which are much higher and stiffer to prevent the driver from sliding out of the seat around tight/fast turns. In addition, the bolster also provides the seat with a much more aggressive and sporty look.

The Corvette has offered leather seats as a standard option on all its vehicles since 1977. Since the Corvette is a sports car, the seat designers are much more focused on ensuring that the driver can feel the road than adding additional comfort or more rear seat entertainment options such as other vehicles.
What car has the most comfortable seats?
Car seat comfort is one of the key attributes customers tend to focus on when purchasing a new vehicle regardless of the car market segment. However, each automotive seat is built to meet the specific customer needs of the target customer. For example, Corvette seats aren’t built for as much comfort as compared to a typical vehicle, but most Corvette owners do not use their vehicles as a daily driver or for long road trips. However, the seat comfort of the Corvette must meet the customer’s expectations based on the seats in its competitive set.
On the other hand owners of traditional sedan such as the Nissan Altima or Toyota Avalon which is used as a daily driver needs to be designed to be comfortable for longer durations since they are generally used for longer periods of time ( long road trips). However, both of those vehicles are not fun to drive and are usually considered “people movers”. Seats designed for vehicles that do take road trips, generally have more comfortable seats with lower bolsters and less dense foam. This type of seat can be found on most passenger vehicles/SUVs and Trucks. More and more common these family-oriented vehicles are integrating massaging seat features to their vehicles to enhance seat comfort and the duration a driver can sit in their vehicle prior to feeling fatigued.
The seats in police vehicles are designed for comfort similar to a passenger vehicle but the bolsters and front edge of the seat are specifically designed so the officer can get in and out easily and quickly without their gun belt getting caught on the seat. Designing a seat requires a constant balance of comfort and durability, with safety always at the forefront.
A study conducted in by the Chalmers University of Technology in Sweden examined what features and attributes of a seat tend to contribute most to a comfortable seat. The study was conducted in Germany and the 53 participants whose ages ranged from 18 -50+. Participants were asked to evaluate the seats in the following vehicles Opel Corsa, Renault Clio, Toyota Aygo, Fiat 500, Geely Haoyue, and Ford Fiesta.
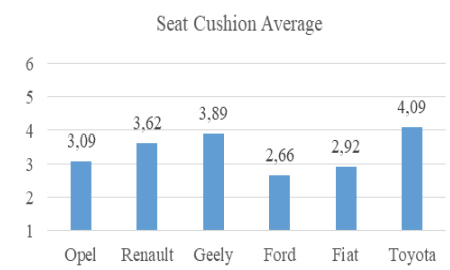
Of these competitive set of vehicles, the Toyota has the most comfortable seat followed by the Geely in a close second. The study concluded that the biggest contributors were overall seat adjustability, the height of the bolsters, and overall seat width.

What does rear-seat entertainment mean?
A rear-seat entertainment system is usually additional package auto manufacturers offer on their luxury or family-oriented vehicles. Companies such as Nissan, Subaru, and GMC put a huge emphasis on rear-seat entertainment, and integrate a big TV screen into the back of their front bucket seats. this is all with the intention of entertaining the rear passengers during road trips.

What are the advantages of bucket seats?
Each seat is designed specifically for each vehicle and the target customer or audience of the vehicle. The Corvette is no exception, the bucket seats ensure that the position of the driver always remains firm and stable, providing the driver with my confidence while on the track. At the same time, the rather narrow and recessed shape of the bucket seat allows the Corvette owner to more effectively “feel” the road. In addition, the bucket seats in the Corvette provide a rigid and sturdy construction that guarantees greater safety in unpredictable situations on the road or track. As a result, they also provide better protection for the occupant in the event of an accident. Moreover, the Corvette’s bucket seats are much lighter than standard seats. Seat designers look at any way to reduce complexity and additional parts which is important since sports cars such as the Corvette, try to minimize the mass of the vehicle as much as possible.

Sport Car Seat (bucket seat) Attributes:
Below are the vehicle attributes and sub-attributes, along with requirements and design challenges that come along with the attributes. There were a couple of attributes that don’t apply to the driver posture, position, and seat for the Corvette bucket seat. These attributes are Vehicle Dynamics, Security, Emissions, and Communication and Entertainment.
Vehicle Attribute | Sub-attribute | Requirements | Design Challenges | |
1 | Package | Occupant Seating package, Entry and Exit, Luggage/Cargo Package, Fields of View, Powertrain Package, Suspensions and Tire Package, Other Mechanical and Electrical Package | – Seat must fit all occupants (1% female, up to 99% male) within the front seat space -ingress egress durability | – Seat must fit through the door opening, for installation purposes -Trim cover must withstand ingress egress motion for 25,000 user cycles without creating any rips or tear in the material -in vehicles with multiple rows, the 2nd (or 3rd row) must have enough leg/knee room for occupant comfort -seat trim cover sew lines can’t diminish seat quality during ingress egress -All moving components must have 5-10mm clearance to any other component -seat must be designed so it can anchor into flooring (interdisciplinary interface) |
2 | Ergo | Locations and Layouts, Hand and Foot Reach, Visibility and Legibility, Posture Comfort, Operability | -Hand/Foot Reach -Elbow room -Comfort curves -H-Point -torso angle | -Seat adjustability (fore/aft, up/down, seat recline) to allow comfort for people of different shapes and sizes. These features must be packaged within the seat (no overflow into undesignated areas) -Appropriate seat height so the user can see over the steering wheel |
3 | Safety | Front Impact, Side Impact, Rear Impact, Rollover, and Roof Crush, Air Bags and Seat Belts, Sensors and ECMs, and Other Safety Features (Visibility, Active Safety) | -Airbag -Sled crash testing – Head Restraint -Buckle/ and retractor | – Airbag must package in the seat and not be visible to the customer (and still function) – Head restraint must not block occupant visibility – Seat belt/buckle must package in the seat and keep occupant safe in a crash |
4 | Styling and Appearance | Exterior – Shape, proportions, stance, etc., Interior – Configuration, Materials, Color, Texture, etc. | – Appeal to customer -New and exciting | – Create new and exciting seats while still meeting all other design constraints (comfort, cost, weight, safety, etc) -Trim cover material must be durable enough to withstand typical user wear and tear (specifically focusing on cushion bolster). -Material must be semi-water/sweat resistant -Seat trim stitch lines must not impact user comfort (Can’t be felt while sitting in the seat), while also effectively keeping the trim snugly secured to the seat structure. |
6 | Performance and Drivability | Performance Feel, Fuel Economy, Long Range Capabilities, Drivability, Manual Shifting, Trailer Towing | – keeping the driver in place | – Comfortable seats while driving around tight corners and up/down steep elevated surfaces – Bolster design to prevent any sliding around in seats around tight corners/up and down hills |
7 | Noise, Vibrations, and Harshness (NVH) | Road NVH, Powertrain NVH, Wind Noise, Electrical, and Mechanical Systems NVH, Brake NVH, Squeaks and Rattles, Passerby Noise | – seat vibrations/squeaks/ must not be heard by the user while driving the vehicle (excluding functioning the seat, moving it fore-aft, or reclining the seat) | – All components in the seat must be packaged in a way that they won’t rub and in turn make noise. -Any for/aft vertical power or manual seat adjustments must move at a speed appropriate for the user (still while being quiet) |
8 | Interior Climate Comfort | Heater Performance, Air-conditioning Performance, Water Ingestion | – heat/vent features must function for 25,000 cycles without failure – surface area? | – Heat/Vent durable trim covers – Heat/Vent features must be packageable in the seat footprint -Heat/Vent features must not be visible to the customer |
9 | Weight | Body System Weight, Chassis System Weight, Powertrain Weight, Electrical System Weight, Fuel System Weight | – Seat must weigh the minimum without compromising seat integrity. | – Seat components must weigh as minimally as possible, while still maintaining seat functions and requirements. Consider part thickness, number of parts, part material, structure design |
10 | Costs | Cost to the Customer, Cost to the company | – Seats must be cheaper than they are sold for (including material, labor, and ED&T), returning a profit | – Seat needs to “turn a profit” while still maintaining the highest quality -Additional seat functionality adds cost to the customer |
11 | Customer Life Cycle | Purchase and Service Experience, Operating Experience, Life Stage Changes, System Upgradability, Disposal and Recyclability | – Seat must withstand general wear and tear for at least 25,000 cycles without compromising quality | – All seat components must be designed so they are serviceable. Take apart/install parts without compromising part durability, or function for at least 500 cycles |
12 | Product and Process Complexity | Commonality, Reusability, Carryover, Product Variations, Plant Complexity, Tooling, and Plant Life Cycle Changes | – Minimal seat complexity, while still making customers happy | – Maximum similarities between driver and passenger seat design. -Minimal trim covers colors/materials. -Minimize fastener sizes. If possible use the same modules/electronic features in both seats, even if they don’t have the same level of functionality (Ex: same driver seat module and passenger seat module, even if the passenger seat doesn’t have the same adjustability features that the driver seat does). -reuse parts from past model years or other programs (within the same company) if possible, to reduce ED&T, and complexity in the plant -maximize seat similarities between different trim levels of Corvette (same plastics, fasteners, head restraints, etc) -tolerances must be considered for all parts, to improve ease of assembly for operators -Minimizing the # of electrical connectors to reduce labor time for seat install |
How do you measure torso angle?
The purpose of this procedure is to measure the torso angle of a vehicle without the H-point machine. The H-point is the theoretical location where that the hip bones and upper leg portion of a human body rotate about To conduct the torso angle procedure the following materials will be required:
- a protractor
- string
- a deadweight/mass

Torso angle evaluation:
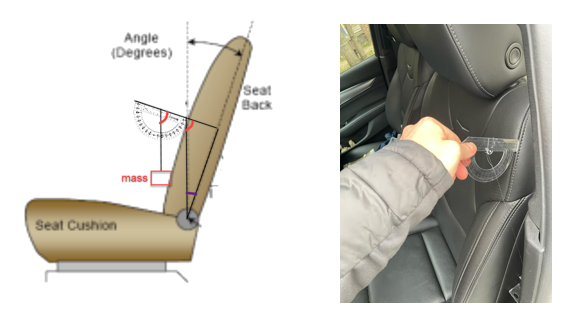
- set the angle of the driver’s side seat to 10 degrees. Remember that the angle measured on the protractor is the complementary angle of the seat back angle automakers design.
- set the driver-side seat to 20 degrees
- have a participant sit on both the driver’s and the passenger’s side and tell you which seat is preferred.
- adjust the passenger side seat to 30 degrees and repeat step 3
- repeat steps 3 and 4 for the 40 and 50-degree comparison.
- adjust the driver-side seat to 20 degrees.
- set the passenger side to 30 degrees.
- repeat steps 3
- repeat step 5
- continue this process until at least 10 comparisons have been completed.
Evaluation Findings:
Thurstone’s Method of Paired Comparison:
A sample of the torso angle questionnaire can be seen below, in this questionnaire, the participants are being asked if they prefer the seat back angle on the row over the column:

The number of subjects preferring the torso angle in the column over the torso angle in the row divided by the number of participants:

the proportion of preferred responses (pij):
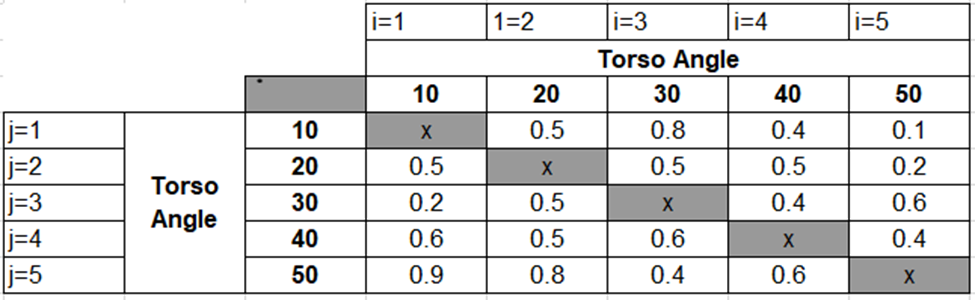
Z values corresponding to Pij:

Scales Values Graphed:
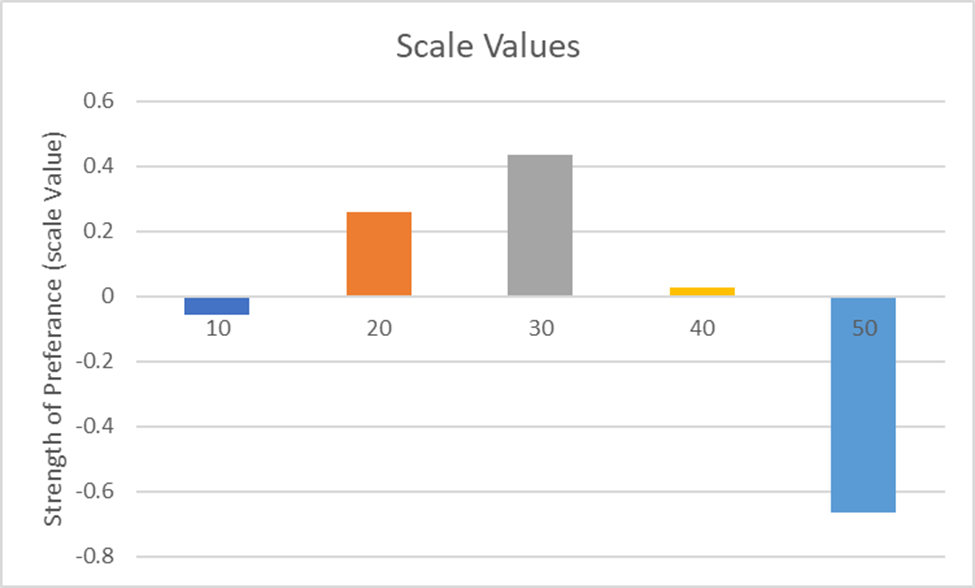
What is a comfortable seat angle?
When it comes to automotive seat design, the typical design torso angle is around 22 degrees. The torso angle of a seat used in a truck is generally larger than that of a smaller sedan/ crossover or sports car so the exact value of the ideal torso angle can slight fluctuation depending on the vehicle type. However, after conducting our experiment our values were closer to 30 degrees. After reviewing our evaluation procedure it can be concluded that our method of measuring torso angle was not the most accurate. By placing our protractor at the outside of the upper bolster of the seat, we are measuring the torso angle of the upper bolster, rather than the seat back. See the image below, for reference. The issue with this way of measuring torso angle is the bolster comes forward and might sit at a slightly different angle than the centerline of the seat back. However, that was the only place we could place the protractor based on the equipment we had. The best way to measure the torso angle would have been to use an SAE mannequin/ 3D H-point machine.
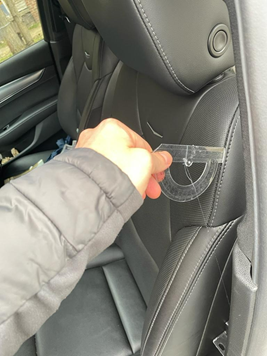
Another issue with this measurement location is the variation from vehicle to vehicle. We measured our torso angles in multiple different vehicles, all of which could have different shaped/angled upper bolsters. Another unaccounted-for variable in our torso angle measurements was the different participants which participated in this study. To be the most accurate, this measurement should be completed with a 50th percentile person. Even though the seat packaging is designed to accommodate the 95th percentile male. Seat comfort is designed to accommodate the largest number of people (male and female). This is why a torso length of a 50th-percentile person should be used. The measurement location and participant height/weight differences most likely explain why our “ideal” torso angle is about 10 degrees larger than what the automotive companies use.
If we had more time and resources a more accurate way of measuring the torso angle is using a 3D H-point machine with a probe. This allows you to use a 50th percentile person’s height and weight, as well as gives you easy locations to take these measurements on. In the image below you can see the manikin has a designated H-point pivot point, which can be used along with the probe to determine the 3D location of the H-point. This same idea is applied when finding the back angle. The torso angle is read on the back angle quadrant of the 3D H-point machine. This machine helps get an accurate and consistent measurement each time.
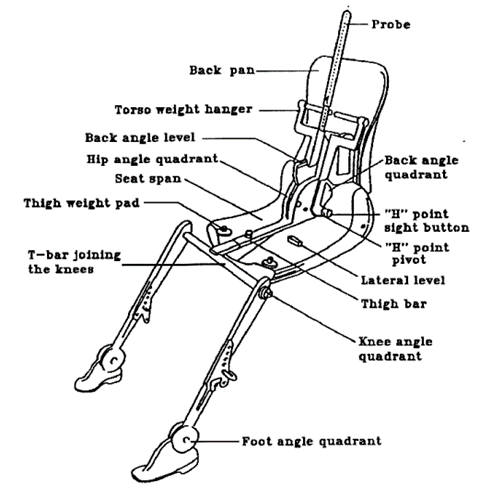
How do you test a car seat?
There are many other tests that can be conducted on a seat to get a better understanding of driver posture, position, and seat. One of these tests is ingress/egress where a robot moves a manikin butt form across the outboard seat cushion/back bolsters replicating a user getting in and out of the seat to understand wear patterns on the seat over time. This test is repeated upwards of 50,000 cycles to represent a lifetime of wear on a seat. Another test is sled crash testing, where a buck is used to simulate a crash. A buck is a mockup of an actual vehicle, usually consisting of the BIW, the steering wheel, restraints (seat belt/buckle, airbags, etc) as well as a seat and dummy occupant. The purpose of sled testing is to understand what happens to the occupant during a crash. The ideal scenario is the seat belt/buckle keeps the occupant constrained to the seat, the head restraint prevents whiplash while the airbags diminish the impact to the occupant. The final test we could have completed was H-point testing. This generally requires a 3-D H-point machine. This procedure is very complex and involves setting the manikin in place correctly, adding the weight in the correct order, and waiting time between testing and a probe to collect the exact 3-D dimensions of the H-point in a given coordinate system. This test is generally completed multiple times with slight design changes in between to reach an ideal design position.

What are the tradeoffs in design (bucket seat)?
When designing a seat for driver posture and position there are many trade-offs. The first one is bolster height vs comfort. Usually, a sports car has higher bolsters to create a sporty, or cool look. These seats are not going to be as comfortable on a long car ride, compared to a typical family car which has lower bolsters that naturally fit our body shapes better. Another trade-off is seat trim material (leather vs durability). Generally, soft real leather is considered the highest quality seat trim material and is wanted by most high-end customers. These softer materials don’t withstand standard wear and tear over time as well as rougher materials do. Often automotive companies use vinyl for trim covers, because to most people they look the same as leather but have much more durable properties (as well as being much cheaper). Similar to trim covers, the foam under them is also important. A dense foam will help withstand user wear and tear, while initially not appearing as comfortable as a seat with less dense, more squishy foam.
An important seat design trade-off is complexity. Customers generally want a larger range of different trim covers, but this adds to cost by increasing manufacturing complexity. The seat manufacturers require more time to sort out these different trim covers, as well as engineering development and tooling for these new unique trim covers. The seat structure is generally the heaviest part of the seat because it is made out of steel. The structure has to withstand all the force on a seat over long periods of time, in all use cases. By using a heavier material, like thicker pieces of steel, the seat will be more durable. This in turn increases the weight of the vehicle as a whole, which is not the desired outcome due to decreased fuel efficiency. Also, the increase in part thickness will increase the part cost. The seat structure is not the only situation that deals with the trade-off of part weight vs durability, this is also evident in all seat fasteners, plastics, trim covers, foam, etc.

Another important trade-off when designing a seat has to do with the craftsmanship. Craftsmanship in the context of the seat is the attention to detail in a seat and how “well built” it is; which all plays into customers’ perceived quality of the seat. This means no exposed unfinished metal, no visible wires, nothing visible under the seat from a user’s eyeliner, no visible zippers, no puckers in the trim cover, straight stitch lines, etc. The craftsmanship can also include things other than visibility imperfections. If a seat squeaks when functioning, it could be perceived as poorly made. Fixes to this could include adding foam between parts to prevent a squeak. In general to improve craftsmanship many companies will add parts to cover what shouldn’t be shown or spend more time and money on a design that performs well over time. Craftsmanship and cost/weight/manufacturing time are trade-offs when designing a seat.
The final trade-off is seat functionality. Seat customers usually push to have the largest number of functions on their seat, for example, reclining, massage, headrest adjustment, adjustability of the seat positions forward and back, heat, vent, lumbar adjustment, rear seat entertainment, etc. Adding each of these power adjustable functions to a seat adds cost, weight, manufacturing time, and complexity to a seat. However, if a seat didn’t have any of these functions many customer wouldn’t be interested in buying the vehicle. On the other hand if the seat have too many functions, the MSRP of the vehicle starts to go way up and the customer won’t be able to afford the cost of the seat.

Reference:
- https://encrypted-tbn2.gstatic.com/images?q=tbn:ANd9GcRmo5-CQt_7wiN5MUqN7ULy63PKpuc7v2hpqi32qHcoLJRdRnbJ
- https://hmr.araiindia.com/Control/AIS/413201592535AM4_7_AIS_021_Amd_2.pdf
- https://www.sciencedirect.com/science/article/pii/S2212827121009185