The Birth of Lean Manufacturing
Lean manufacturing is focused on reducing time in the production system while improving response times from suppliers and customers. It’s closely related to just-in-time (JIT) manufacturing, which aligns production with demand by only producing goods that have been ordered. Both approaches aim to boost efficiency, productivity, and continuous improvement while minimizing waste for both producers and suppliers. Lean manufacturing builds on JIT by further cutting down cycle, flow, and throughput times, eliminating activities that don’t add value for customers. It also involves people outside the manufacturing process, like those in marketing and customer service.
When did foreign cars become popular in America?
Foreign cars became popular in America starting in the 1950s and 1960s. By the 1970s, Japanese manufacturers were introducing more fuel-efficient cars compared to American models, leading to increased popularity. Throughout the 1970s and 1980s, the demand for foreign cars steadily grew as American consumers sought more economical and reliable alternatives to the big 3 Detroit automakers.
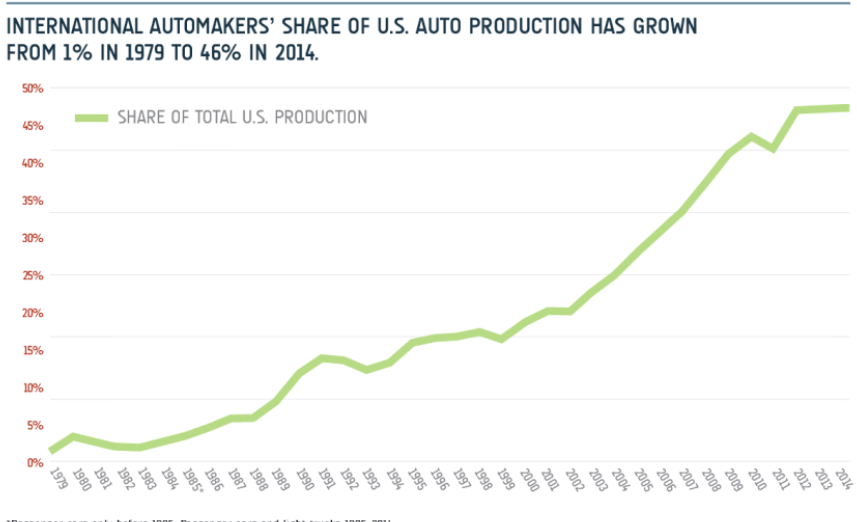
When did Toyota enter the US market?
Toyota entered the U.S. market in August 1957 thanks to Seishi Kato. This led to the creation of Toyota Motor Sales USA in 1957, marking one of Toyota’s earliest foreign ventures. Instead of focusing on high-end luxury models, Toyota introduced smaller, fuel-efficient cars like the Corolla. The first Japanese car sold in the United States was the Toyopet Crown. This vehicle signaled the beginning of Toyota’s presence in the American market. The growth of international automakers in the US has only grown. Foreign automakers have set up manufacturing facilities in the US to avoid tariffs and continue to grow their brand in the American market.
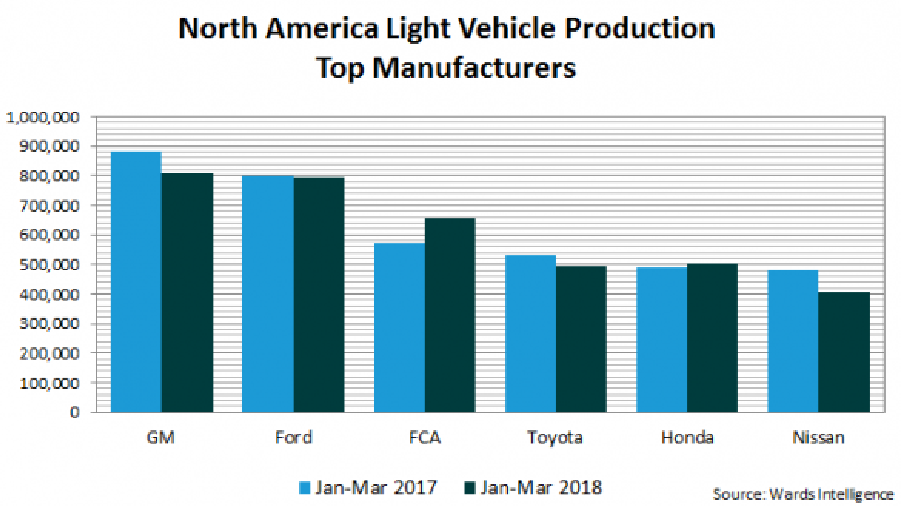
What is the origin of lean manufacturing?
The origins of Lean manufacturing can be traced back to the Japanese company Toyota. The Toyota Production System (TPS) began to take shape in the early twentieth century. Key figures in the development of TPS included Sakichi Toyoda, Kiichiro Toyoda, Eiji Toyoda, and manufacturing engineer Taiichi Ohno.
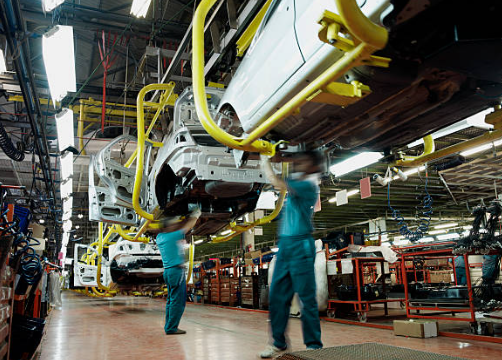
Lean manufacturing has its roots in the Toyota Production System (TPS) from the post-war 1950s and 1960s. Also known in the U.S. as “The Toyota Way” , Toyota’s system was based on just-in-time inventory management and automated quality control. Toyota engineer Shigeo Shingo identified seven types of waste (muda in Japanese). These included: excess inventory, overproduction, over-processing, unnecessary transportation, excess motion, waiting periods, and defective products.
The term “Lean” was coined in 1988 by businessman John Krafcik in his article “Triumph of the Lean Production System”. It was further defined in 1996 by researchers James Womack and Daniel Jones. They outlined five key principles: specify value by product, identify the value stream for each product, ensure value flows without interruption, let customers pull value from producers, and strive for perfection.
What is Kaizen’s theory?
Kaizen theory is the fundamental philosophy behind lean manufacturing. The term “Kaizen” is Japanese and means “change for the better” or “continuous improvement”. It represents a Japanese business philosophy focused on processes that continuously enhance operations and involve all employees. Kaizen emphasizes that productivity improvements are achieved through a gradual and methodical process.
What are the 5 principles of Kaizen?
- Kaizen Attitude: Embracing a mindset of continuous improvement and fostering a culture where everyone is committed to making small, incremental changes.
- PDCA Cycle (Plan, Do, Check, Act): A systematic process for implementing improvements, where you plan a change, execute it, check the results, and act on what is learned to make further improvements.
- Systemization and Systemic Approach: Develop a structured and organized method to ensure that improvements are consistent and sustainable across the entire organization.
- The Necessity of Continuous Learning: Encouraging ongoing education and training for employees to adapt to new methods and technologies that support continuous improvement.
- Implementing Continuous Improvement for Operational Excellence Enterprise-Wide: Applying the principles of continuous improvement across the entire organization to achieve operational excellence in all areas.
Which of the following are the benefits of lean manufacturing?
Lean manufacturing offers several benefits, including reduced waste, improved quality, increased productivity, lower costs, shorter lead times, improved customer service, and enhanced employee satisfaction. By streamlining and organizing business processes, lean manufacturing helps eliminate wasted time, effort, and money. For instance, companies can use lean systems to purchase only the exact amount and type of materials needed to produce a product. Removing unnecessary steps and equipment allows companies to develop higher-quality services and products.
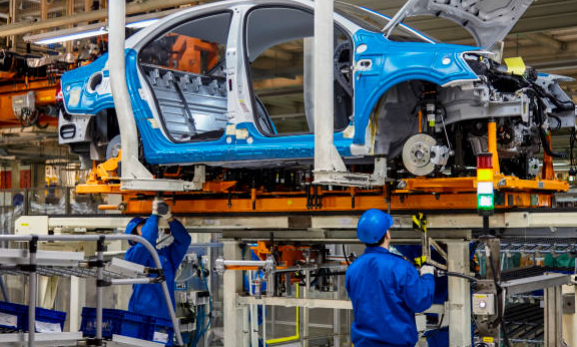
Additionally, lean manufacturing enables companies to produce more goods in less time by eliminating non-value-adding activities and improving workflow. This approach can lead to lower production costs, which in turn increases profits. Lean manufacturing can also significantly reduce lead times, sometimes by as much as 99%, by streamlining the production process. With major inventory and production issues resolved, companies can better focus on meeting customer demand. While delivering great products to the market more effectively. Furthermore, lean manufacturing also provides all workers with more responsibility. This fosters a relationship of trust that can enhance company culture and boost employee morale.
What are the differences between Mass Manufacturing and Lean Manufacturing
Mass Manufacturing, pioneered by Henry Ford and the assembly line, focuses on producing goods in large-sized lots. The goal is to maximize the number of products manufactured in each lot, with the assembly line operating continuously without stopping. This approach aims for high volume and low cost per unit. However, it can lead to issues such as overproduction, high inventory levels, and inefficiencies in the production process.
On the other hand, Lean Manufacturing seeks to reduce waste and maximize productivity by improving assembly line processes. It emphasizes continuous improvement, efficiency, and flexibility. Lean Manufacturing aims to produce goods in smaller, more efficient batches, reducing inventory levels and streamlining operations. This approach enables companies to respond quickly to changes in customer demand and market conditions.
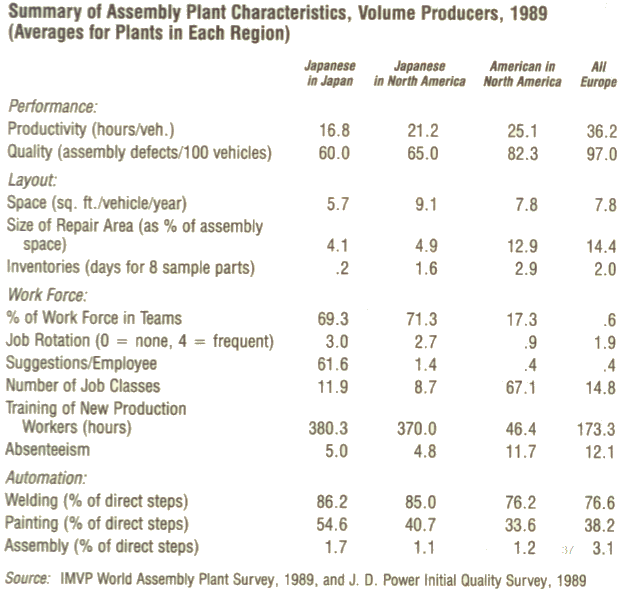
The Japanese automakers’ adoption of Lean Manufacturing enabled them to achieve greater efficiency and effectiveness than their American counterparts. Japanese automakers spent an average of 16.8 hours per vehicle and had only 60 assembly defects per 100 vehicles, compared to American automakers in the US, who required 25 hours per vehicle and had 82 defects per 100 vehicles.
How does lean manufacturing affect quality?
Lean manufacturing has a significant impact on quality in several ways. First, it prioritizes cutting wasted costs and resources, eliminating anything that does not add value to the operation. This focus on efficiency has a trickle-down effect, reducing costs and improving both quality and production time.
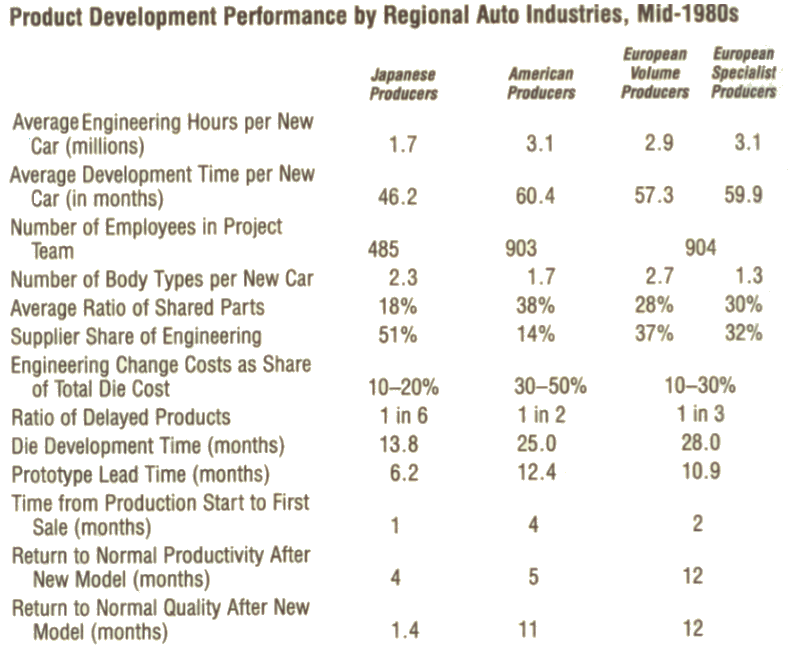
Additionally, lean manufacturing allows automakers to adapt to new product changes and technologies more quickly. It is not uncommon for there to be spikes in quality issues following a new generation vehicle or new vehicle technology or manufacturing techniques. However, Japanese automakers, who embrace lean principles, can return to normal quality levels in less than two months. In comparison, American automakers take around 11 months, and European automakers take about 12 months to address quality issues and return to normal production levels. This demonstrates the effectiveness of lean manufacturing in maintaining and improving quality standards.
Companies use lean manufacturing to boost efficiency by receiving goods only as needed for production, reducing inventory costs and waste while increasing productivity and profit. However, this requires accurate demand forecasting, as any delays in the supply chain can negate the benefits. It can also put stress on workers due to inflexible conditions. Successful implementation depends on consistent outputs, high-quality processes, and reliable suppliers.
The joint venture between GM and Toyota
The joint venture between GM and Toyota, known as New United Motor Manufacturing, Inc. (NUMMI), was established with mutual goals in mind. Toyota aimed to build cars in the United States to avoid import restrictions from Congress and to learn how to work with American workers. They chose the Fremont plant, notorious for having the worst workforce in the US auto industry at the time. Meanwhile, GM sought access to quality small cars and wanted to learn about Toyota’s production system and management philosophies, collectively known as The Toyota Way, which had made Toyota a leader in the automotive industry.
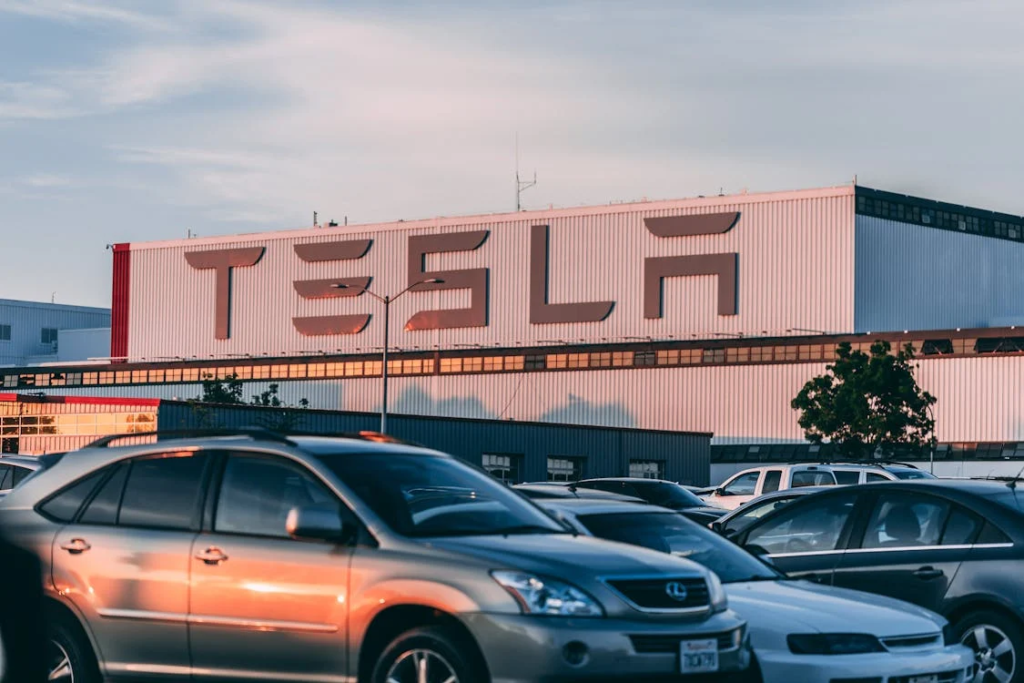
GM also wanted to reactivate an idle plant and workforce; the Fremont facility had been a GM plant from 1962 to 1982 but was closed due to issues with quality, productivity, absenteeism, and worker safety. The collaboration resulted in the creation of NUMMI, which manufactured vehicles sold under both brands. One notable product of this joint venture was the Pontiac Vibe, a compact car sold by Pontiac from 2002 to 2010, which was jointly developed with Toyota and mechanically similar to the Toyota Matrix.
How did NUMMI change its culture?
NUMMI changed its culture through several key strategies. Firstly, the decision to transform the troubled Fremont Assembly into the new NUMMI plant was significant. Despite resistance, the leadership of the UAW union insisted on re-hiring the same union leadership that had overseen GM’s worst workforce. Toyota agreed, believing that their system could turn things around.
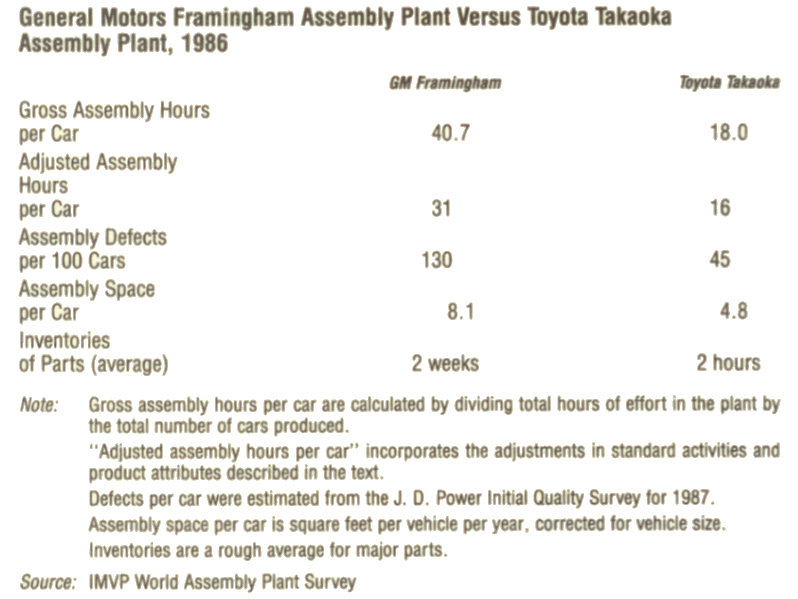
Secondly, the implementation of the stop-the-line, or andon, system on the assembly line was crucial. This system, where any worker could stop the production line to address quality issues, became emblematic of the new culture. All GM and NUMMI personnel underwent training in Japan, where they learned and worked with the stop-the-line system or a variation of it. This approach instilled a sense of responsibility and empowerment among workers, fundamentally changing the culture at NUMMI.
Was NUMMI a success?
Yes, NUMMI was a resounding success. It quickly became competitive with Japan’s plants, setting a high standard among American auto plants. NUMMI brought new practices and methodologies to the United States, revolutionizing car manufacturing. The transformation was remarkable; from being GM’s worst plant, NUMMI reduced assembly defects to just 45 per 100 cars compared to 135 at GM Framingham. Additionally, the time taken by workers to assemble a vehicle was reduced to 19 hours, a significant improvement from the 31 hours at GM Framingham.
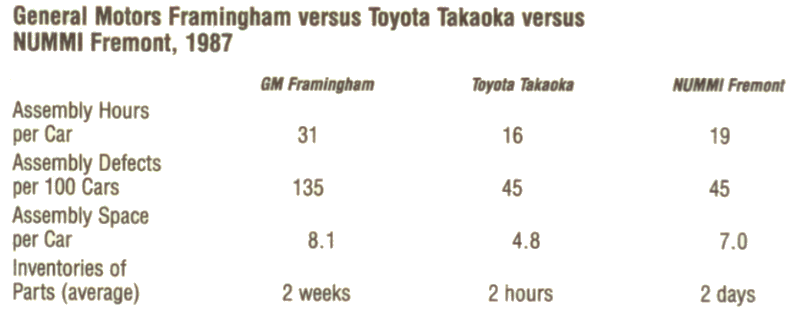
Conclusion
In conclusion, the birth of lean manufacturing represents a significant shift in industrial philosophy, emphasizing efficiency, waste reduction, and continuous improvement. Originating from the Toyota Production System in the 1950s and 1960s, lean manufacturing has evolved into a global phenomenon, impacting industries worldwide. Its core principles, including eliminating waste, improving quality, and involving employees in the improvement process, have revolutionized how companies approach production. As we look to the future, lean manufacturing will continue to drive innovation, helping businesses become more competitive and sustainable in an ever-changing marketplace.