DC Motor Design
A DC motor utilizes direct current (DC) to generate mechanical force, commonly relying on magnetic forces produced by currents in its coils. Nearly all DC motors incorporate an internal mechanism, whether electromechanical or electronic, to periodically alter the direction of current within the motor.
DC motors were initially widely adopted as they could be powered by existing direct-current lighting power distribution systems. The speed of a direct current motor can be adjusted across a broad range, achieved by either varying the supply voltage or adjusting the current strength in its field windings.
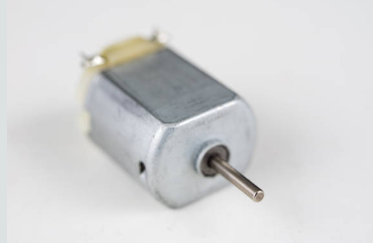
Small DC motors find applications in tools, toys, and household appliances. The universal motor, a lightweight brushed motor used in portable power tools and appliances, can operate on both direct current and alternating current. Larger DC motors can even be used in the propulsion of electric vehicles, elevators, hoists, and in drives for steel rolling mills.
What are the 3 types of DC motors?
Three primary types of direct current motors are commonly found: Series, Shunt, and Compound. These classifications are based on how the field windings are connected in relation to the armature circuit.
Armature & Field Circuit: The Dynamic Duo
Imagine a DC motor as a mini powerhouse, converting electrical DC into mechanical motion. At its core, it’s all about teamwork. The armature circuit, home to the motor’s winding coils, represents the “I’m ready to work” part of the team. It’s where the electrical current flows, generating a magnetic field.
On the other side, we have the field circuit. This is like the conductor who keeps everyone in sync – it produces a magnetic field that interacts with the one generated by the armature circuit, making the motor spin. See the circuit and equations below:
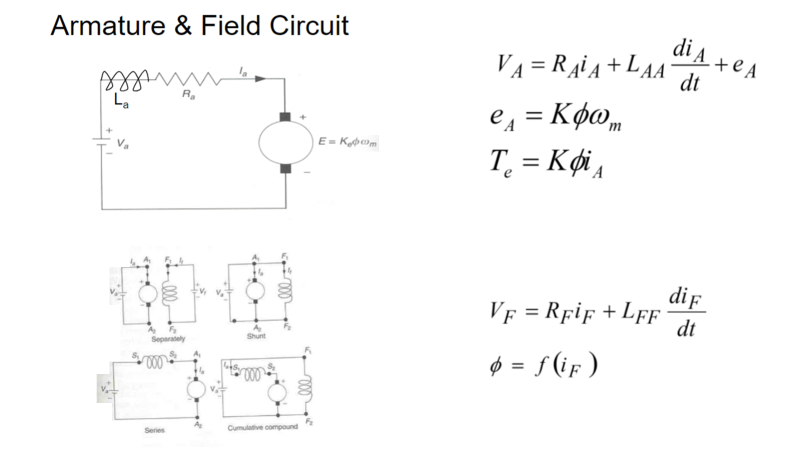
DC Motor Characteristics: More than Meets the Eye
Direct current motors come with a set of characteristics that define their behavior. From torque (the motor’s twisting power) to speed, current consumption to efficiency, these are the factors that determine how well our motor performs. Speed torque characteristics is controlled by varying armature voltage and/or field current.
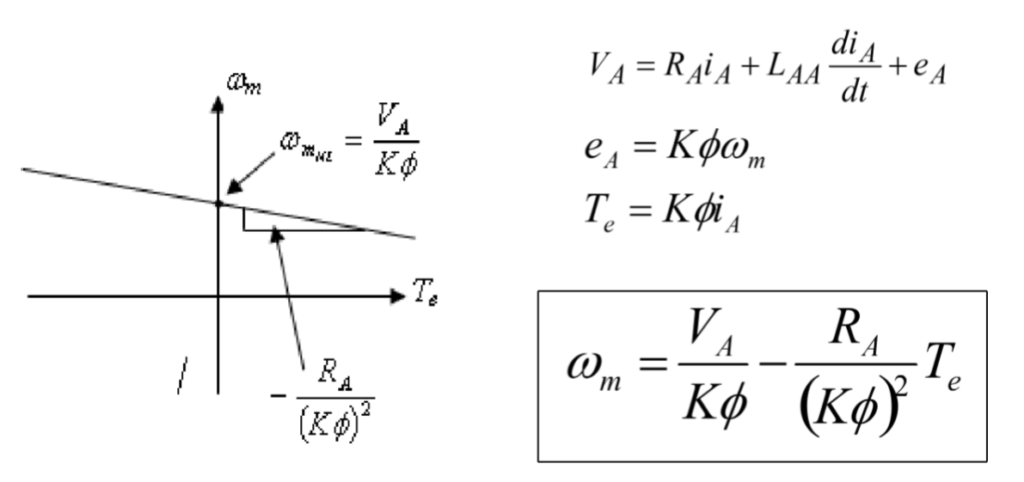
Peek into the Field Structure
Speaking of fields, let’s zoom in on the field structure in direct current motors. Picture this: the field structure is like the motor’s spine. It’s either permanent magnets or electromagnetic windings that generate the magnetic field. This field interacts with the current in the armature circuit, resulting in the rotation that does the heavy lifting – literally!
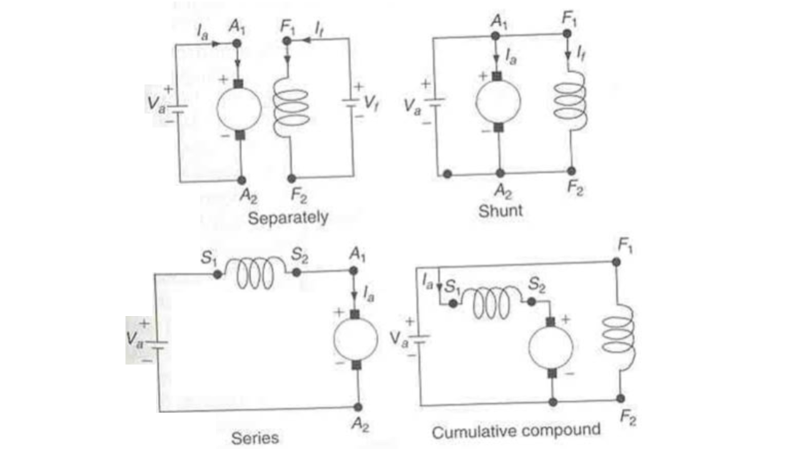
Mastering the Speed Control
Imagine having a remote control for a DC motor’s speed – that’s what speed control is all about. This is where our modeling starts to shine. By adjusting the voltage or current flowing through the motor, we can make it go faster or slower. It’s like finding the perfect rhythm for a dance – the right moves at the right time make all the difference.
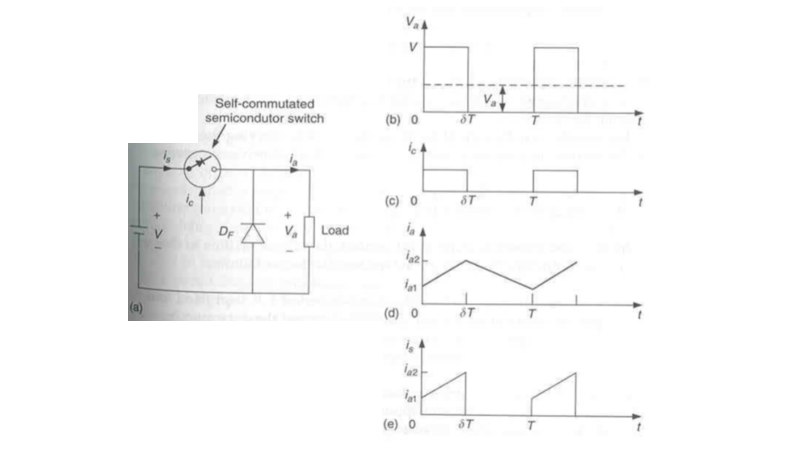
Modeling the Marvel: Equations at Play
Now, let’s understand the mathematical models that encapsulate the behavior of DC motors. These models are like blueprints that predict how the motor will behave under different circumstances. They take into account factors like the motor’s electrical and mechanical properties, allowing engineers to simulate and fine-tune performance before even building the physical motor. Modeling of DC machines can be modeled using different tools, such as Matlab/Simulink and Simplorer. The advantage using Matlab is that it is supported by dSPACE – a rapid prototyping tool.
Inputs, Outputs, and Parameters: The Control Panel
Imagine you’re baking cookies. The type of flour, sugar, and chocolate chips you use determine how delicious the cookies turn out. Similarly, in the DC motor world, we have inputs (like voltage and load torque) that we can tweak to get desired outputs (such as current and angular speed).
Inputs and Outputs of a DC Motor
- Inputs
- Va, voltage
- TL, load torque
- Outputs
- ia, current
- ω, angular speed
Parameters of a DC Motor
The parameters of a DC motor, like resistance and inductance, play a pivotal role in this delicate balancing act. Below is a full list of paramaters engineering play with to design a direct current motor:
• La, Stator (Armature) inductance
• Ra, stator resistance
• KT, torque constant
• KE, emf constant
• B, shaft damping constant
• J, inertia
How do you calculate motor output current and angular speed?

Is DC better than AC motor?
Which Motor Packs a Greater Punch: AC or DC? AC motors are generally regarded as more potent than their DC counterparts since they can produce higher torque by leveraging a more robust current. Nevertheless, DC motors are typically more efficient and extract better performance from the energy they receive. The advancement of power electronics has facilitated the replacement of DC motors with AC motors in many applications.
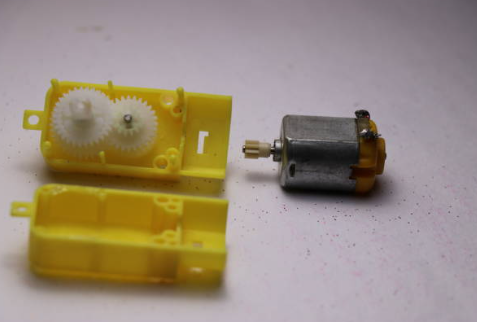
What is the disadvantage of DC motor?
The drawbacks of these motors are primarily associated with sparking during operation, making them unsafe for use in environments where fire hazards exist. This sparking also results in high levels of EMI (electromagnetic interference) and contributes to the brushes wearing out over time.
Can DC motor generate electricity?
Design engineers may be surprised to learn that both Brushed DC and Brushless DC (BLDC) motors can function as generators. A brushed motors are well-suited for generator applications that call for a DC voltage output, whereas a brushless motors are more suitable for applications requiring AC voltage.
Conculsuion
In conclusion, exploring the intricacies of a DC motor reveals a fascinating world where electrical currents transform into mechanical motion. From understanding the basics of armature and field circuits to delving into the nuances of speed control and modeling, the journey through the inner workings of these motors is nothing short of enchanting. As we unravel the magic behind direct current motors, we gain a deeper appreciation for the engineering marvels that power countless devices and industries, reminding us of the remarkable blend of science and ingenuity that drives technological progress.