Crashworthiness 101
Crashworthiness refers to a structure’s ability to reduce the number of fatal and serious injuries that occur in an impact/ accident. Most commonly assessed in aviation and automotive safety. Various criteria determine crash safety, depending on impact type and vehicle. Evaluation can be performed through finite element analysis which is a form of computer-aided engineering (CAE) that uses computer models (e.g., RADIOSS, LS-DYNA, PAM-CRASH, MSC Dytran, MADYMO) to run static and dynamic test.
Evaluations can also be performed using hardware/ running physical experiments, or in retrospective by analyzing crash outcomes. The prospective assessment considers factors like deformation patterns, acceleration, and injury probability predicted by human body models. Injury probability relies on criteria, and mechanical parameters correlating with injury risk, with the Head Impact Criterion (HIC) being common. Post-impact, crashworthiness is gauged by real-world injury risk, often using regression or statistical methods to account for other influencing factors. For this article, we are going to focus primarily on automotive crashworthiness.
Who regulates crashworthiness in the US?
Crashworthiness focuses on occupant protection and the governing bodies who regulate crashworthiness in the US are: The National Highway Traffic Safety Administration (NHTSA), the Federal Aviation Administration (FAA), the National Aeronautics and Space Administration (NASA), and the Department of Defense (DoD). Each of these organizations has taken the forefront in advocating for crash safety in the United States. Each entity has formulated its official safety regulations and engaged in extensive research and development within the field. They are also responsible for developing and upgrading test procedures for evaluating motor vehicle/aviation safety.
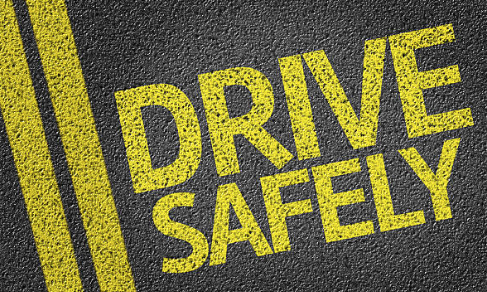
What are the different types of crash testing to understand a vehicle’s crashworthiness?
In the late 1970s, the National Highway Traffic Safety Administration (NHTSA) started assessing and publishing crashworthiness data on the passenger vehicles sold in the United States. These ratings were based on the performance of a vehicle in pre-defined simulated crashes, in which crash test dummies would mimic the dynamic behavior of the human body [3].
The dummies were equipped with sensors that would then provide an estimation of how safe they were in a vehicle. The Federal Motor Vehicle Safety Standards (FMVSS) dictate the standard crash standards and minimum performance levels all automakers must comply with to sell vehicles in the United States.
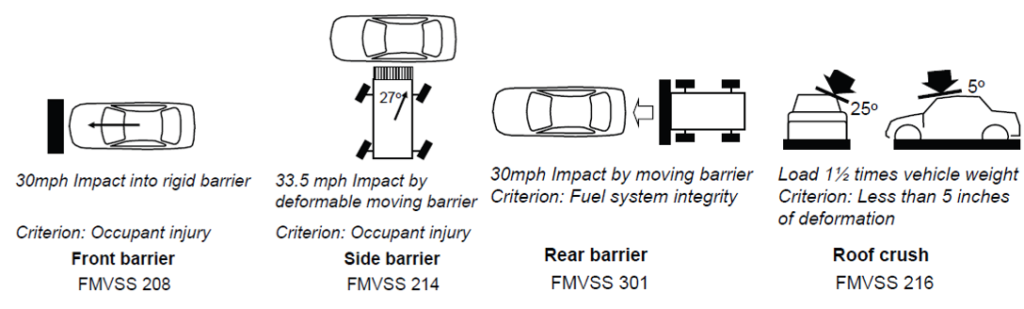
These standards were endorsed by the National Highway Traffic Safety Administration (NHTSA) in 1966 and apply to all passenger vehicles with a gross weight rating of under 10,000 Lbs. These standards are intended to protect vehicle occupants in the event of a crash. These standard tests can be categorized into four major types: front impact (FMVSS 208), side impact (FMVSS 214), rear impact (FMVSS 301), and roll-over resistance (FMVSS 216).
The New Car Assessment Program (NCAP): evaluates vehicles beyond the minimum government standards. The NCAP evaluation is based on the probability of injury for a specific test, measured with a star scale ranging from one star – the higher probability of injury, to five stars – the lower probability of injury.
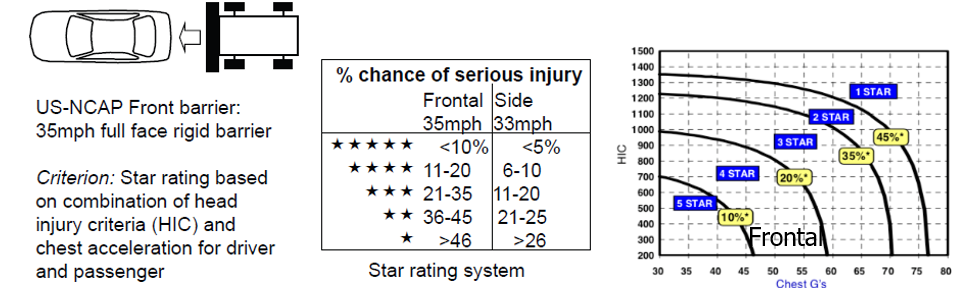
What is the difference between IIHS and NHTSA?
The Insurance Institute for Highway Safety (IIHS) is a private organization that is funded by insurance companies. NHTSA is a government agency that is responsible for keeping drivers safe while operating a motor vehicle. NHTSA issues FVMSS based on laws from Congress that automakers must comply with.
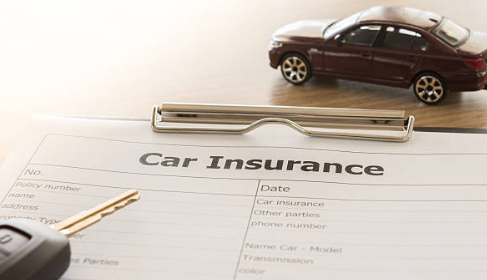
The Insurance Institute for Highways has a more extensive crash testing program when compared to NHSTA. IIHS usually evaluates both a vehicle’s crash performance and driver-assistance features. Both IIHS and NHSTA are widely respected in the automotive industry, and automakers do their best to an on the “top safety pick” list.
What is meant by crashworthiness?
Crashworthiness by itself is not a characteristic or feature that can be measured or quantified. The crashworthiness of a vehicle can be assessed however by how well it can protect the lives of its occupants in the event of a collision regardless of the collision type or collision configuration.
The main objective of the BIW is to redirect the impact kinetic energy in such a way as to reduce the intrusion into the safety cage of a vehicle (passenger compartment). Designing a vehicle to manage these loads effectively and safely is the goal for all automakers and is a key strategy to prevent significant injury to all occupants during a car crash [1].
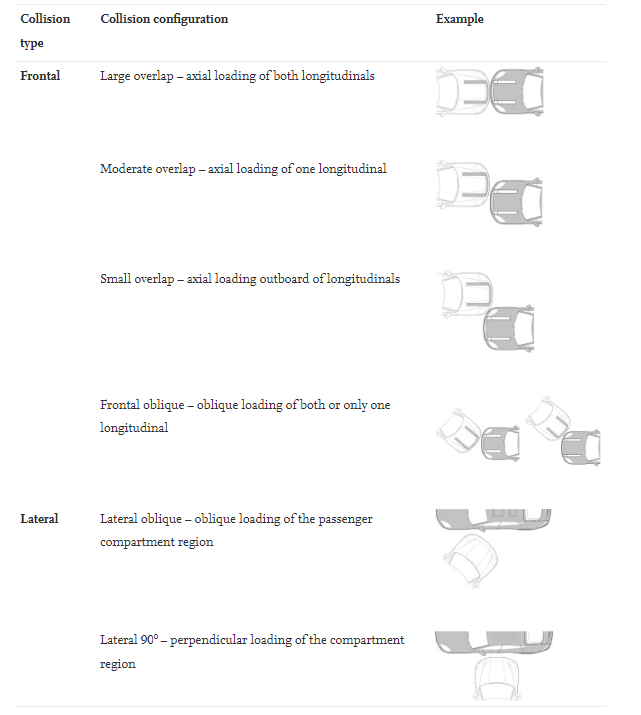
What is the difference between crashworthiness and crash avoidance and mitigation?
The Crashworthiness of the BIW can be defined as a passive safety device. A passive safety system or device is any device that is intended to keep an occupant safe after an accident has already occurred. The BIW intends to react to a collision and redirect loads to keep occupants safe.
An example of this would be crush initiators on a mid-rail in the front engine compartment. These crush initiators force the BIW impact beams to fail in a predetermined way and thus limit the deformation into the occupant safety cage.
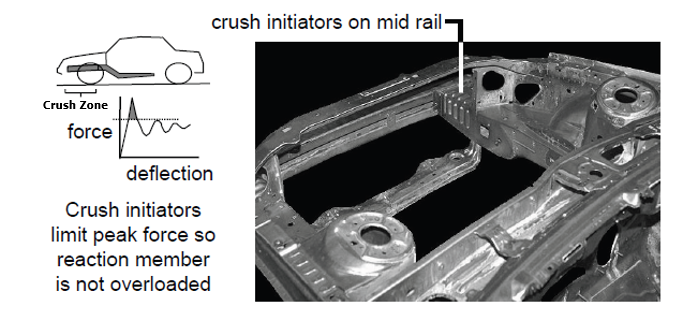
However, there are other passive safety features in a vehicle outside the BIW such as airbags and seat belts. On the other hand, active safety features or crash avoidance and mitigation features are features on a vehicle that attempt to avoid collisions altogether. These are more electronic and software-related systems such as adaptive cruise control, lane keep assist, or electronic stability control to name a few.
What determines a vehicle’s crashworthiness?
A vehicle’s crashworthiness is determined by it efficiency of its structural load path. The biggest factor in a good structural load path is good BIW geometry which enables the vehicle to absorb impact energy. Contrary to current belief, a stronger structural member is not always desirable for crashworthiness.
If the structural members are too strong/stiff in the crush zone, then these structural elements will not absorb the intended energy in the crush zone which could result in increased injury for the occupant. That is why proper sizing of a beam is critical for good energy absorption, an efficient design will generate an approximately square wave over a large distance by using controlled failure mechanisms. The image below shows a desirable accordion crush pattern.
How beam design affects a car’s crashworthiness
For small loads, the column is under simple compressive stress (Figure A). As the compressive load increases gradually frame damage is observed as the elastic buckling load of the walls is reached and the structural members begin to buckle (Figure b).
As the load continues to increase past the ultimate load of the buckled walls, a load is reached where the corners of the section cripple, and the load drops (Figure c). Once the crippled corner bottoms out, the load begins to increase again (Figure d). This process repeats itself, forming an accordion pattern and a load-deformation curve that oscillates about an average crush force (Figures e & f).
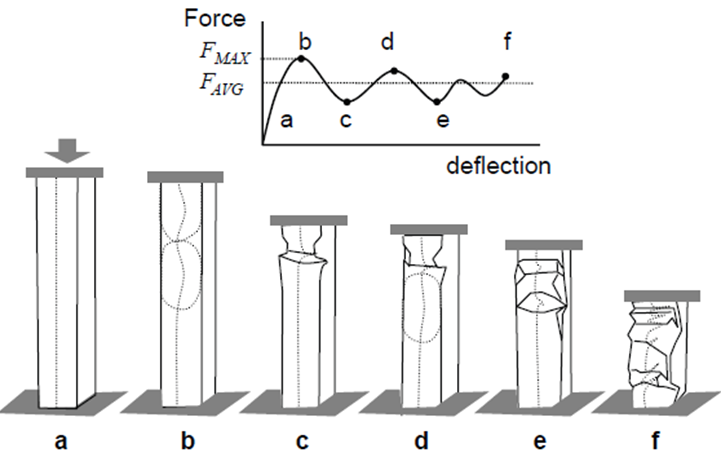
Weld flange design impact energy absorption and crashworthiness
The position of the weld flange can also affect the average crush force of a structural member. Ideally, the weld flanges are in the center of the box section. Depending on the packaging of a vehicle and the specific cross-member this might not be an obtainable design.
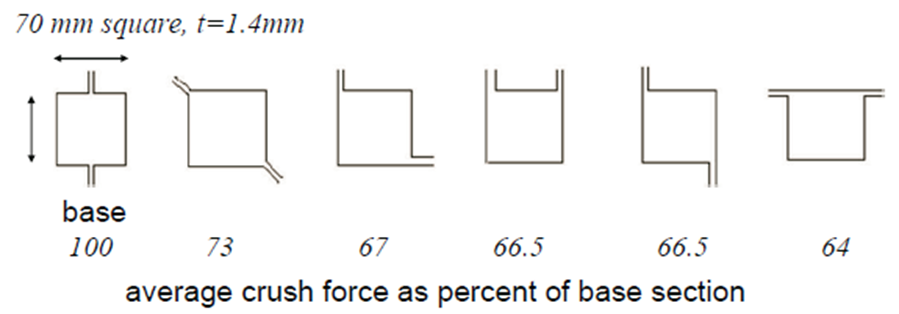
The shape of the cross-section across a load-carrying member also impacts the load-carrying capacity. There is also a much bigger impact when these members are dynamically tested vs statically tested.
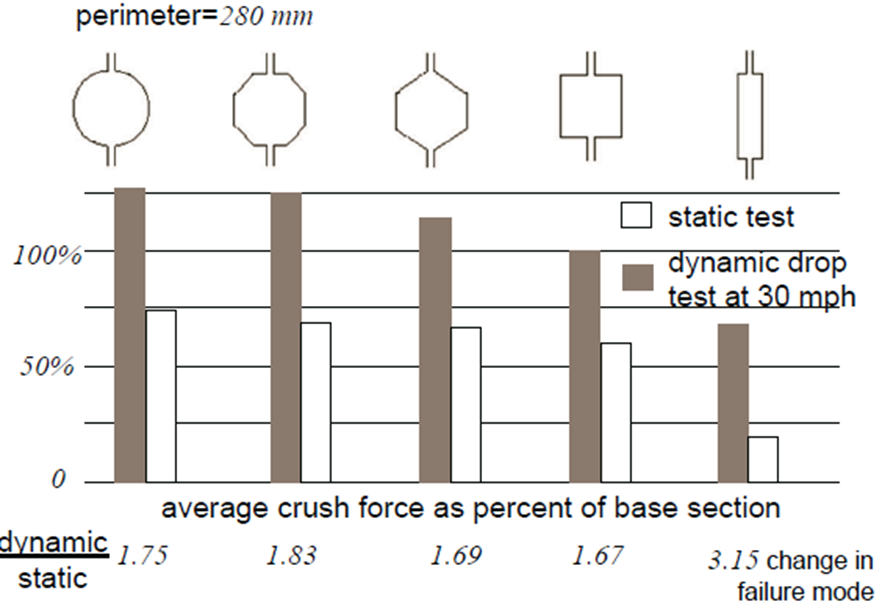
Automakers do not develop new vehicle architecture (platform) very frequently; it is very time-consuming and expensive. As a result, when they do, they must keep in mind the philosophy of how vehicle loads and crash energy will be managed and how all the major components and subsystems will be “packaged” within the allotted space.
It is much easier for a vehicle to achieve the 5-star crash safety rating when the vehicle is designed on an architecture that can carry and distribute load via a good structural load path. In other words, an inefficient BIW design will not magically become efficient just by implementing the greatest materials that are on the market. However, excellent material selection can turn a good BIW design into an exceptional design. Below is a typical breakdown of the function of various elements in a typical automotive structure design.
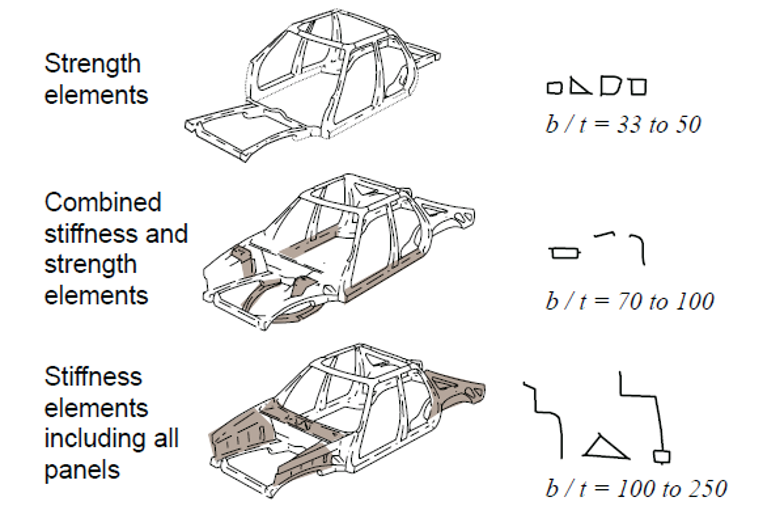
What is the most serious type of crash?
A head-on collision or frontal impact crash is the most dangerous type of crash in a vehicle. The combination of the force acting on the occupants which is a result of the front impact can lead to serious injury and even death. Chest injuries are common during a front-end collision, primarily in elderly occupants. Older passengers suffer proportionally more severe chest injuries in low/moderate-speed impacts when compared to young and middle-aged occupants.
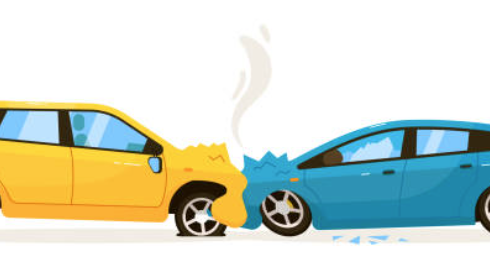
What is a frontal impact test important for a vehicle’s crashworthiness?
A frontal impact test (FMVSS 208) is intended to simulate a high-speed head-on collision, where two vehicles collide with each other. A passenger test vehicle traveling at 30 mph crashed into a fixed barrier to simulate a front-end collision. The purpose of this test is to evaluate any injuries that might have occurred to the occupant’s head, neck, chest, and legs.
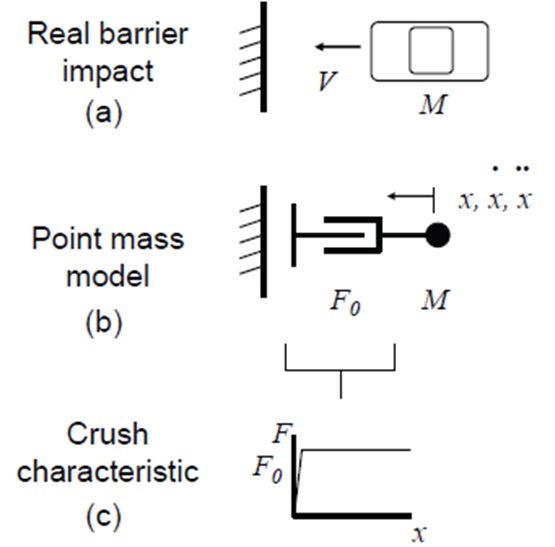
Ideally, the passenger compartment or safety cage should see minimal deformation to prevent any injury to the occupants. To achieve this automakers design the crush zone to deform upon impact and generate the forces to decelerate the vehicle in the desired manner. The frame damage that a vehicle experiences is necessary to counteract the crushing force and help protect the vehicle occupants.
Using internal best practices and computational analysis software (CAE) automakers can size structural elements to achieve desired targets for managing typical crush force. Even though the federal requirement is a vehicle must protect an occupant in the event of a 30mph head-on collision it is common practice for auto manufacturers to overengineer the structural members in the crush zone (safety factor), thus providing some additional protection for all occupants.

What is a crush zone?
The crush zone or crimple zone, Δ, is the area forward of a passenger compartment or cabin zone. The crush zone is comprised of rigid and partially rigid subsystems that are intended to absorb the crash energy.
- Rigid subsystems within the crush zone: for example the engine and transmission
- Partial Rigid subsystems: the radiator is assumed to crush to 50% of its original thickness.
The primary load-carrying member in the motor compartment is the body-in-white (the impact beam carries about 50% of the loads). Even though the target is for there to be no intrusion into the passenger compartment. In practice, some intrusion in the amount of 50-120mm can occur into the toe pan area without increasing the likelihood of injury to the occupants.
Below are two graphs that show how the force is distributed in the front motor compartment of a vehicle. It can also be observed that once the BIW structure/chassis and powertrain are engaged (~30msec) the vehicle experiences the most significant drop in velocity.
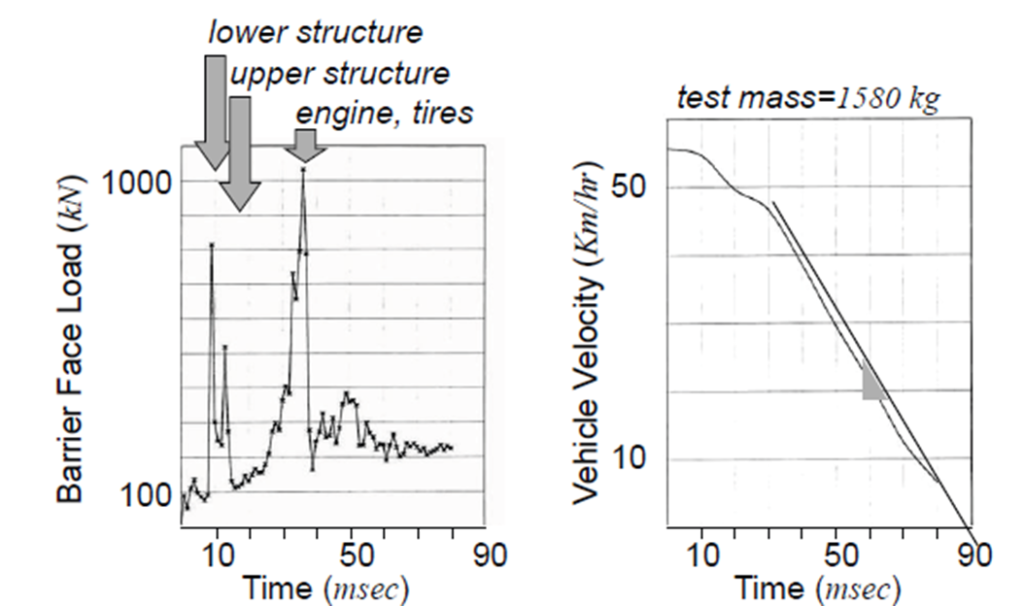
What happens to a vehicle during a front-end collision?
Upon hitting an object or another vehicle with the front end of your car your vehicle, the crash energy loads must transfer into the crush zone. Depending on the severity of the accident, the BIW might be pushed reward to the point where the vehicle’s chassis and powertrain are engaged to help carry the load. However, whenever this does occur it usually causes significant damage to the engine/transmission and front suspension. The load distribution of a BIW during a front barrier impact can be seen below:
- 20% of the force is generated by the upper structure load path just under the top of the fender
- 50% of the force is generated by the mid-rail structure (impact beam)
- 20% by the lower cradle
- 10% by the hood and fenders
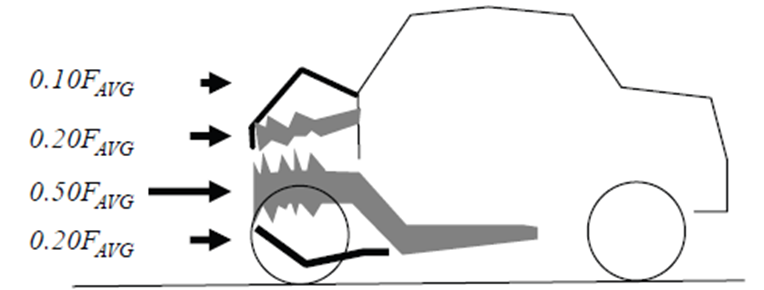
Front-end collision Time Step
A pictorial representation of how the vehicle deforms during a head-on crash can be seen below. The initial velocity of the vehicle is approximately 55 km/h (34.17 MPH) and a full frontal rigid barrier crash is simulated over the first 75ms. The BIW was designed to simulate the deformation behavior of the front motor compartment of a unibody midsized vehicle.
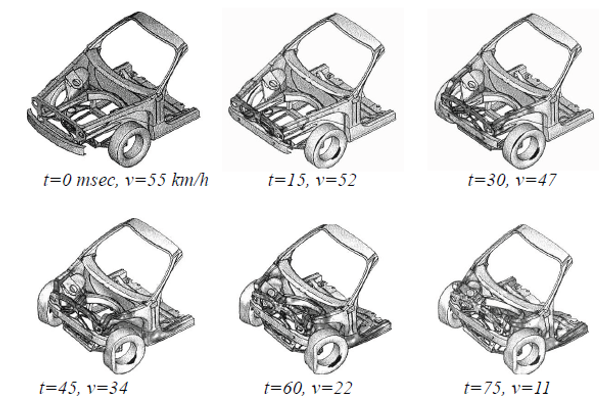
- At t=0, the vehicle is moving at velocity V=VO, and the front bumper is just touching the barrier face.
- t=15 msec, the bumper has collapsed and the motor compartment mid rails and side rails are being loaded.
- At t=30 msec, the mid rails have begun to crumple in an accordion fashion, and the powertrain (engine/transmission) has just touched the barrier and begun to decelerate.
- At t=45 msec, the mid rails and upper rails continue to crumple, the powertrain has decelerated to zero velocity and the wheels have impacted the barrier (engaged the vehicle chassis).
- Finally, at t=90 msec, the vehicle has decelerated to V=0 with the motor compartment crumpled by some deformation, Δ.
What happens to the kinetic energy of a car when it crashes?
During a car crash, the kinetic energy of the vehicle is converted primarily into the work done by the body-in-white to slow down the vehicle. Some of the energy is also converted into heat and sound energy.
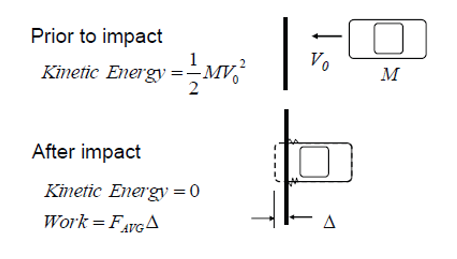
What is the physics behind a car accident?
Several laws of physics can be applied during a car accident. Newton’s first law of motion, an object in motion will remain in motion unless acted upon by another force. The only reason why the velocity or direction of a car changes during an accident is that it encounters another vehicle or object on the road.
This change in the velocity of both vehicles results in changing the momentum (mass x velocity) of the two objects. However, the law of conservation of momentum states that the change in momentum of both vehicles or objects must be equal to zero.
Using Newton’s second law of motion (F=MA) you can calculate the crash forces that the BIW must absorb. Using the second law of motion you can also construct a basic kinematic model and the resulting behavior of a vehicle in a front-end collision.
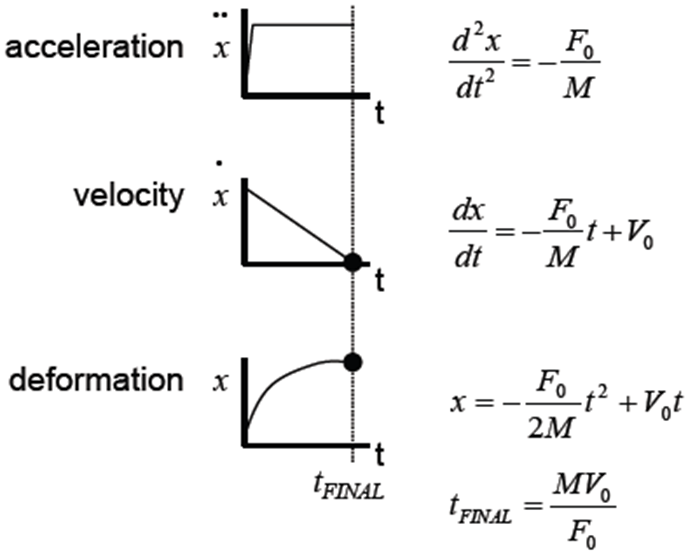
Is your car safe?
It’s important to consider that even though the velocity of the vehicle will begin to drop immediately after the crash, the occupants inside of the vehicle will continue to travel at the same speed for up to 20msec until they collide with the seat belt or airbag.
In general, a lower peak cabin acceleration correlates with a reduced likelihood of occupants getting injured during a front-end collision. As a best practice, automotive engineers design the BIW so that the g-force on the occupant during a front-end collision is under 20g.
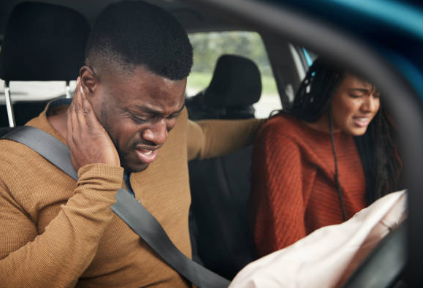
What happens to your body in a front-end collision?
The graph below shows the relationship between the acceleration and displacement of a vehicle during a car crash and how it correlates to the head acceleration of the occupants. The more square-shaped the curve is on the acceleration v displacement graph, the lower the likelihood of the occupants experiencing a head injury. The head restraints /headrests can help limit the rearward movement of an occupant’s head to help diminish the head injury during a crash.
In general, a lower peak cabin acceleration is less injurious. Crush initiators in the crumple zones help get the acceleration as uniform as possible thus reducing the likelihood of injury. These characteristics for cabin acceleration are directly related to front structure requirements since the inertia loads need to be reacted by the BIW. A steep vehicle acceleration during a front-end collision increases the likelihood of whiplash, head and neck trauma, brain injuries, and back and spinal cord trauma.
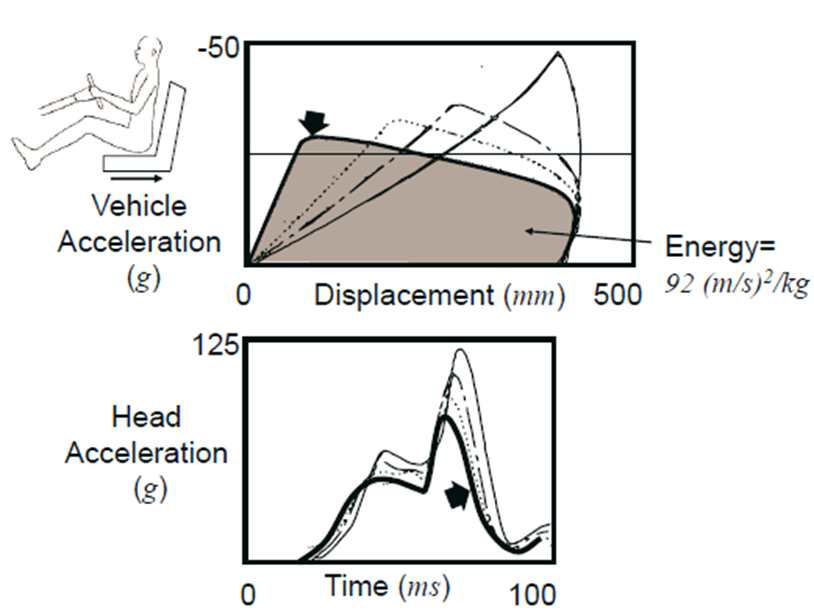
Another variable that needs to be looked at is the pitch of the vehicle during a front-end collision. It has been observed that upon impact with a fixed barrier, some vehicles rotate in a manner where the rear rises upward. This is known as a high pitch and this rotation upwards by the vehicle also increases the likelihood of neck injuries. During a front end-collision, it is also ideal for all 4 wheels to remain on the ground thus maximizing the protection for all occupants.

What are side-impact accidents?
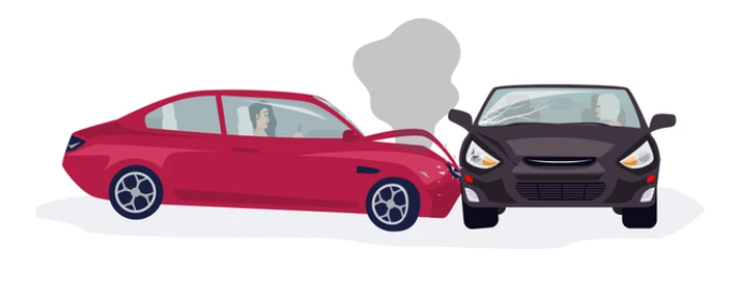
One of the deadliest types of crashes automakers must design for is the side impact collision (T-bone crash). See the figure below exploded view of a BIW and the impact load direction of a side impact. This is a result of there being very little available crush space to absorb energy without intruding on the passenger compartment [2]. As a result, all automakers who sell vehicles in the United States are expected to meet the FMVSS 214 Side Barrier Crash Safety Test.
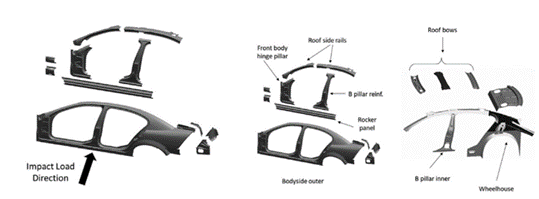
What is a side impact test?
Current FMVSS and NCAP side impact collision tests consist of a stationary target vehicle and a moving barrier impacting from the side. The FMVSS 214 is a destructive test that consists of a vehicle being hit by a moving barrier at a 27° angle and a velocity of 33.5 mph (53.6 km/h). The barrier impacts the vehicle’s lateral axis, simulating the relative velocity of a T-bone crash at an intersection. See Figure 4: FMVSS 214 Side Barrier Crash Safety Test below.
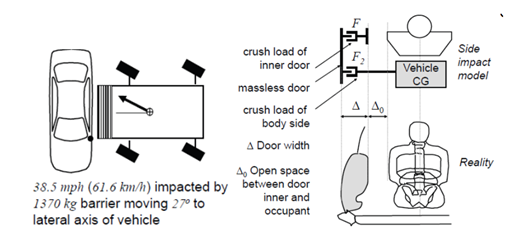
The face of the moving barrier is deformable and crushes at a uniform 45 psi (0.31 N/mm2). The impact speed for FMVSS is 33.5 mph (53.6 km/h), as with front impact, FMVSS requires a minimum injury performance.
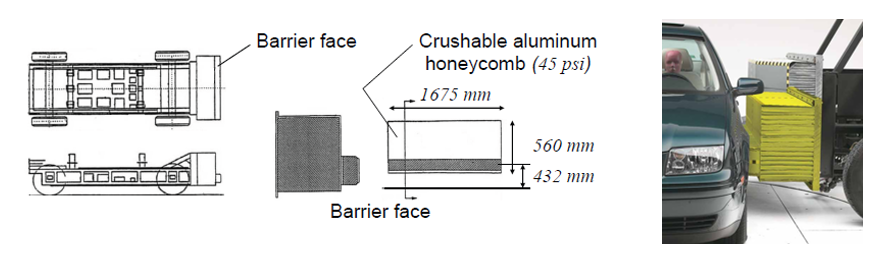
The impact speed for NCAP is 38.5 mph (61.6 km/h) and, as with front impact, NCAP reports the probability of serious injury using the star scale. The injury criterion is the Thoracic Trauma Index (TTI) with larger values of TTI indicating a more severe injury (a TTI<57 is desirable).
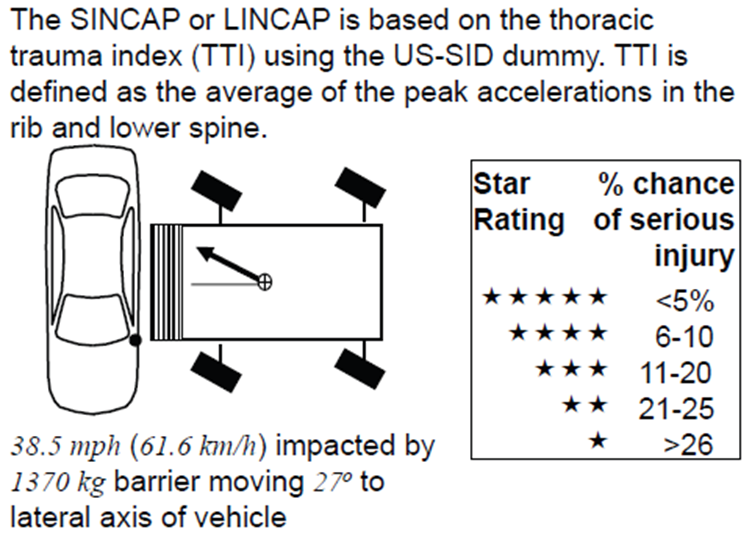
Can you survive being T boned?
Yes, you can survive a side-impact collision (T-bone collision/ broadside collision), but they are very dangerous. Broadside collision can cause an occupant anything from a concussion, and whiplash to severe traumatic brain injury caused by the forceful, back-and-forth motion of the neck. A side impact crash can also lead to a vehicle rolling over (roof crush FMVSS 216) putting additional strain and force on the body. Common T-bone injuries may include:
- Back injuries
- Broken bones
- Disfigurement
- Internal organ damage
- Neck injuries
- Paralysis
- Soft tissue injuries
- Traumatic brain injury
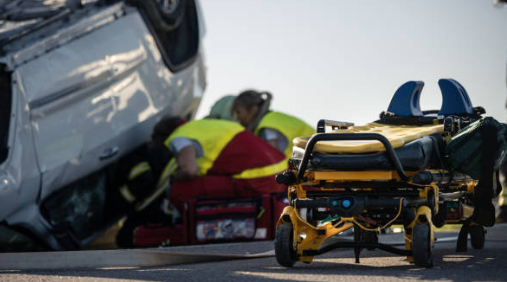
What happens to your body when you get t-boned?
Initially, the impacted vehicle is at rest with zero velocity. Its velocity increases as the barrier (opposing vehicle) makes contact with the door and accelerates the impacted vehicle. A few milliseconds after the impact, the barrier has fully deformed the door (Δ0 ), and both the door panel and barrier move at the same velocity.
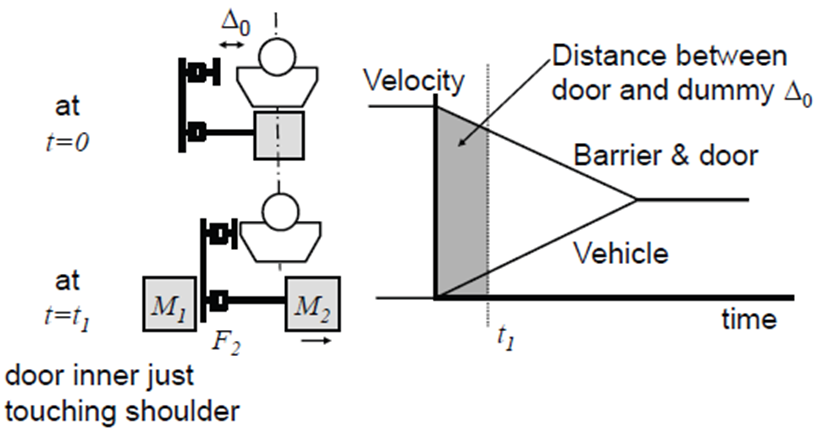
Since there is initially some open space between the crash dummy’s shoulder and the door trim panel, the crash dummy does not react immediately to the side impact. The vehicle must begin to slide laterally before the dummy is struck (this occurs at approximately 25 msec after initial impact). The figure below shows a typical velocity-time history during a side impact.
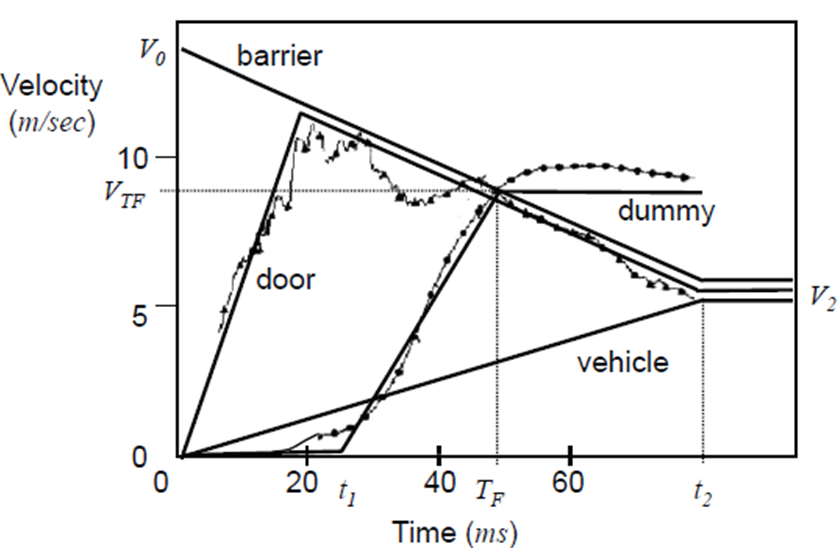
Once the occupants strike the door trim panel, both the door and occupant will reach the same speed ( this happens around 50 msec). Similar to a front-end collision, reducing the acceleration or g force that the occupant experience, lower the likelihood that the occupants will be injured.
The vehicle moves and slides laterally the distance Δ0 before the inner door strikes the occupant. The time at which the door impacts the occupant, t1, can be found by equating the area between the vehicle and occupant velocity-time histories (shaded area in Figure) with the distance Δ0,

Once the velocity of the door and occupant are equal, there will be no more relative deformation between the two, and the impact between the door and occupant is over. This occurs when the door inner has crushed through a distance of Δ.
Side Impact Load Requirements:
A vehicle’s body side outer (BSO) is primarily comprised of very thin, low carbon, and bake-harden steels which carry very little loads. Most of the load is principally carried through the body side inner (BSI) structure. The BSI parts that comprise the main load-carrying members in a T-bone collision are the B-pillar outer reinforcement, the rocker outer, and the roof rails.
As a result, these parts are commonly made from hot-stamped boron steel to achieve a martensitic microstructure in the steel. This enables these parts to carry high loads while limiting part deformation [2]. See the figure: Body Side Inner Below.
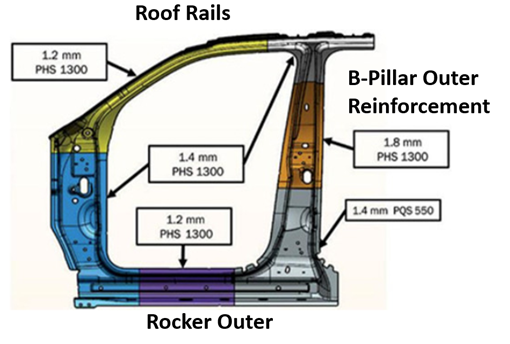
Ideally, automakers always want to transfer more load into the underbody and away from the upper side structure (roof ditch). The lower the force the further the load will be to an occupant’s head and thorax [2].
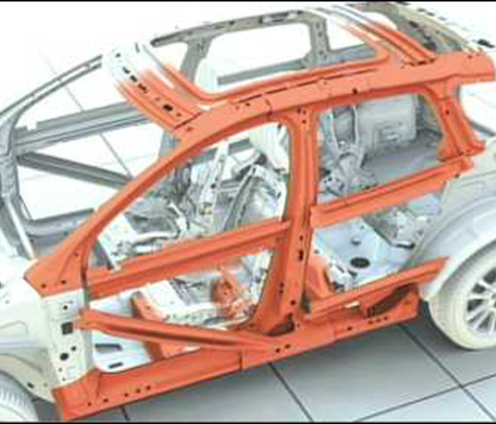
By Increasing the strength of the structural elements in the side impact load path you are able to generate deceleration forces that act upon the barrier, slowing it down quickly before the inside of the door can impact the occupant. Thus the occupant is struck by the door at a lower velocity than what the exterior of the door was hit at.
Physically this high side crush force can be achieved with rigid side-to-side structural members aligned at the barrier face height. A cross member at the B pillar location or at the front of the rear seat pan is effective. Also, the barrier face must be engaged early by aligning structural members such as the rocker, lower B, and C pillars at the height of the barrier face.
What is I-CAR car?
After an accident, you will most likely need to visit a collision center. The repair cost to fix up your vehicle can be quite steep, so your insurance will most likely get involved. When picking an auto body shop it is best to have your car worked on by a shop with is I-CAR certified. I-CAR is an international not-for-profit organization that provides certifications for both auto collision repair shops and auto body technicians.
References:
- Deb, Chapter 11 – Crashworthiness design issues for lightweight vehicles, Editor(s): P.K. Mallick, In Woodhead Publishing in Materials, Materials, Design and Manufacturing for Lightweight Vehicles (Second Edition),Woodhead Publishing, 2021, Pages 433-470, ISBN 9780128187128, https://doi.org/10.1016/B978-0-12-818712-8.00011-2.
- Horvath C.D., Chapter 2 – Advanced steels for lightweight automotive structures,
Editor(s): P.K. Mallick, In Woodhead Publishing in Materials, Materials, Design, and Manufacturing for Lightweight Vehicles (Second Edition), Woodhead Publishing, 2021, Pages 39-95, ISBN 9780128187128, https://doi.org/10.1016/B978-0-12-818712-8.00002-1. - Rocio Suarez-del Fueyo, et all. Cluster analysis of seriously injured occupants in motor vehicle crashes, Accident Analysis & Prevention, Volume 151, 2021, 105787, ISSN 0001-4575, https://doi.org/10.1016/j.aap.2020.105787.
- Fundamentals of Automobile Body Structure Design by Donald E. Malen, SAE International, 2011