Forging Manufacturing Process
Forging is a metal shaping process that involves applying localized compressive forces using a hammer or die. Forging refers to a group of processes where deformation is induced by localized compressive forces. It is considered the oldest metalworking process, often exemplified by the traditional village blacksmith. The equipment used can include manual or power hammers, presses, or specialized forging machines.
While deformation can occur in hot, cold, warm, or isothermal conditions, forging typically implies hot forging performed above the recrystallization temperature. During forging, metal can be drawn out to increase its length while decreasing its cross-section. During upsetting, metal is shrank to decrease its length and increase its cross-section. Finally metal can also be squeezed in closed impression dies to produce multidirectional flow. Common forging processes include closed die forging with flash, closed die forging without flash, coining, electro-upsetting, forward extrusion forging, backward extrusion forging, hobbing, isothermal forging, nosing, open die forging, orbital forging, powder metal (P/M) forging, radial forging, upsetting, and swaging.
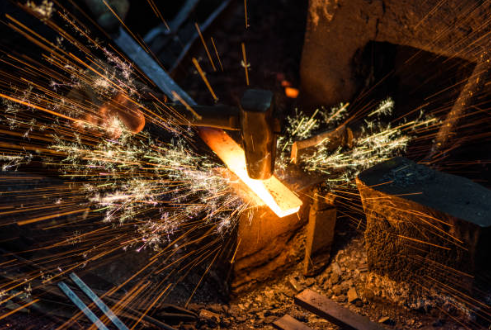
Forged parts can vary widely in weight, from under a kilogram to hundreds of metric tons. This manufacturing technique has been practiced for thousands of years by smiths, who traditionally crafted kitchenware, hardware, hand tools, edged weapons, cymbals, and jewelry. In this article, we will cover everything you need to know about forging, from its history to its different types, techniques, and applications.
When was forging first used?
Let’s start with a quick history lesson. Forging has been around for thousands of years dating back well over 6,000 years, to 4000 BC, with the earliest recorded examples dating back to ancient civilizations like Mesopotamia, Egypt, and Greece. The first metals forged were gold, bronze, and iron, which were used to create tools, jewelry, and weapons. Over time, the process evolved to include more advanced techniques.
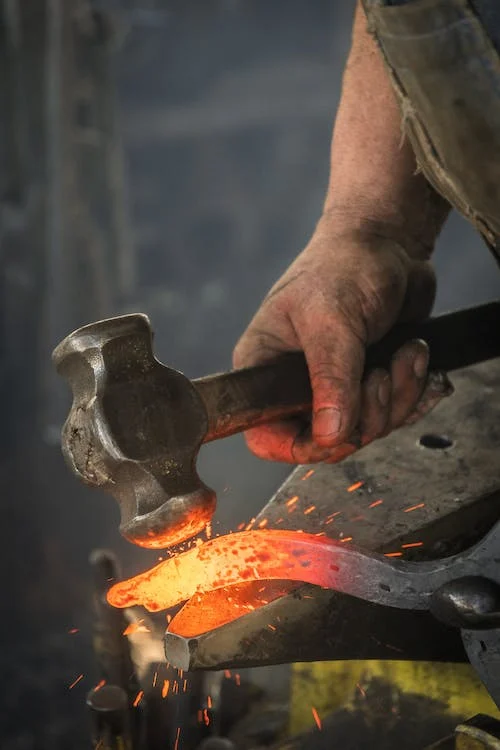
Today, forging is typically carried out using either presses or hammers that are powered by compressed air, electricity, hydraulics, or steam. These hammers can have reciprocating weights ranging into the thousands of pounds. Smaller power hammers, with reciprocating weights of 500 lb (230 kg) or less, and hydraulic presses are commonly used in artisanal workshops. While some steam hammers are still in use, they have largely become obsolete due to the availability of more convenient power sources.
What is a forging process?
Now, you might be wondering, what exactly is forging? Simply put, forging is a manufacturing process that involves the shaping and forming of metal through the use of heat and compressive forces. By heating the metal to a certain temperature and then applying force, it can be shaped into a variety of different forms. The forces are delivered using hammering, pressing, or rolling. Forging is a nonsteady state process that can be classified as:
- Open die forging (upsetting)
- Impression die forging
- Flashless forging
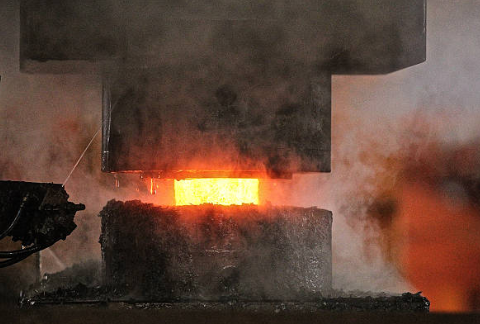
What are the 5 general characteristics of the forging process?
There are five basic types of forging characteristics that are commonly used to shape metal parts. These processes include open die forging, closed die forging (impression die forging), blocker, conventional, and precision. Each type has its unique characteristics and applications.

What type of metals can be forged?
So, what types of metals can be forged? Well, pretty much any metal can be forged, but some are more commonly used than others. For example, metals, and alloys such as steel/stainless steel, aluminum alloy, titanium alloy, and copper alloys are often used in forging applications. As can be seen in the table below, harder metals such as tungsten require a much higher forging temperature when compared to steel or aluminum.
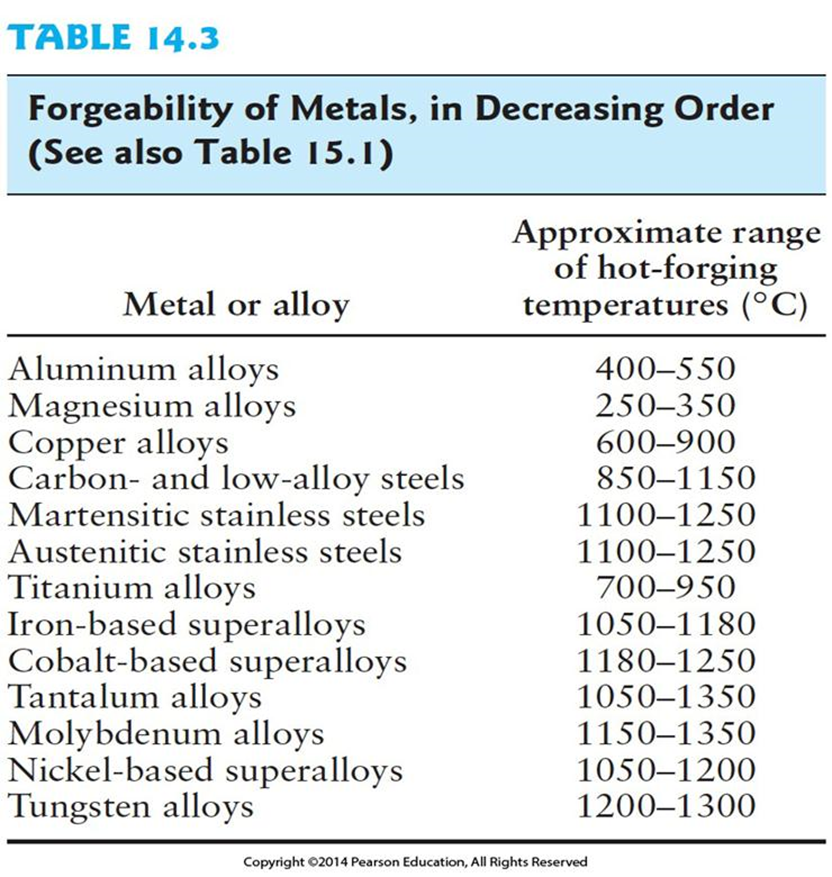
What is upsetting as a forging technique?
One specific technique that’s often used in forging is called upsetting (open-die forging). Upsetting involves deforming metal between two dies. The pressure and friction from the die result in the metal becoming shorter (reduce ho) but increases the width (increase do). Since the metal is not enclosed, barreling of the billet caused by friction forces at the billet–die interfaces is common. Upsetting is principally used for the preliminary reshaping of the workpiece.
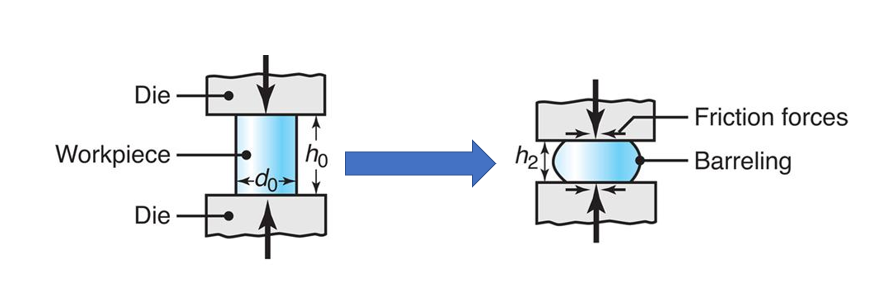
What is grain flow in the forging process?
Another important aspect of forging is something called grain flow. Grain flow is the directional orientation of metal grains and inclusions that have been altered due to the forging process. Individual grains are elongated in the direction of the metal flow (plastic deformation). When metal is forged, its grain structure is altered and by controlling the grain flow during the forging process, the strength and durability of the metal can be improved. The picture below shows a section of a forged part. Note the highly inhomogeneous deformation and barreling, and the difference in shape of the bottom and top sections of the specimen.
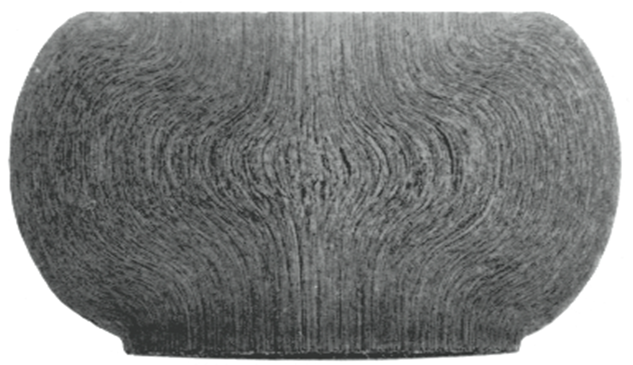
What is the advantage of open-die forging?
Open-die forging is a type of forging where the metal is not completely confined by the dies. This allows for greater flexibility in terms of the size and shape of the forged part. The main advantage of open die forging is that in addition to allowing for greater customization and flexibility in the manufacturing process, your parts are built to last.
The image below shows three different types of open-die forging:
- The picture on the left shows a cogging operation on a rectangular bar. Blacksmiths use a similar procedure to reduce the thickness of parts in small increments by heating the workpiece and hammering it numerous times along the length of the part.
- The middle picture shows how to reduce the diameter of a bar by open-die forging; note the movements of the die and the workpiece.
- The picture to the right shows the thickness of a ring being reduced by open-die forging.
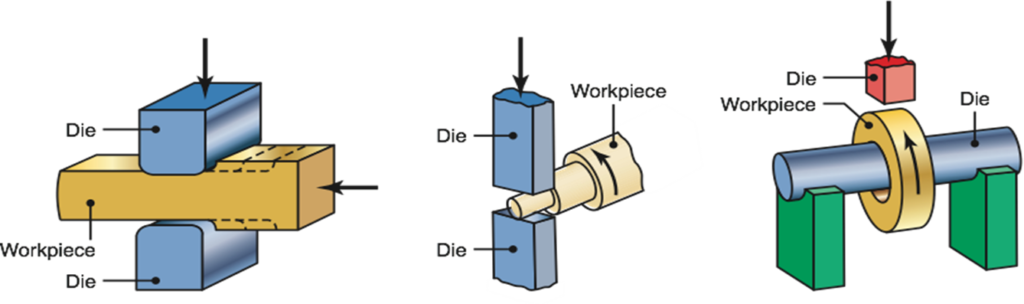
How do you calculate forging pressure?
Calculating forging pressure can be a bit complicated, but in general, it’s based on the size and shape of the part being forged, as well as the material being used. Generally, larger and more complex parts require more pressure to be forged correctly.
Open Die Forging:
The graph below shows the distribution of die pressure in upsetting with sliding friction. Its important to remember that the pressure at the outer radius is equal to the flow stress, Y, of the material. Sliding friction means that the frictional stress is directly proportional to the normal stress.
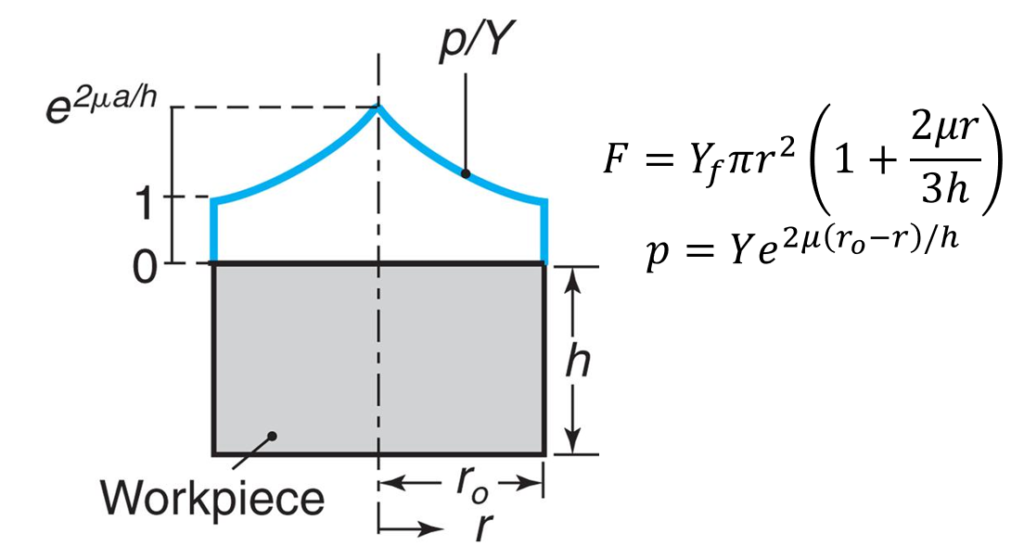
Closed Die Forging:
Typical load-stroke curve for impression-die forging. The graph below shows the sharp increase in load when the flash begins to form.
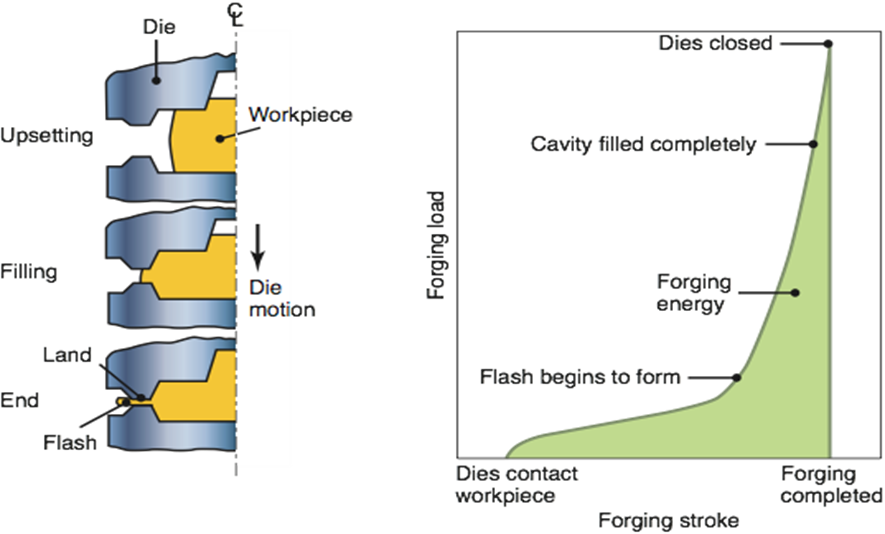
Forging force equations:
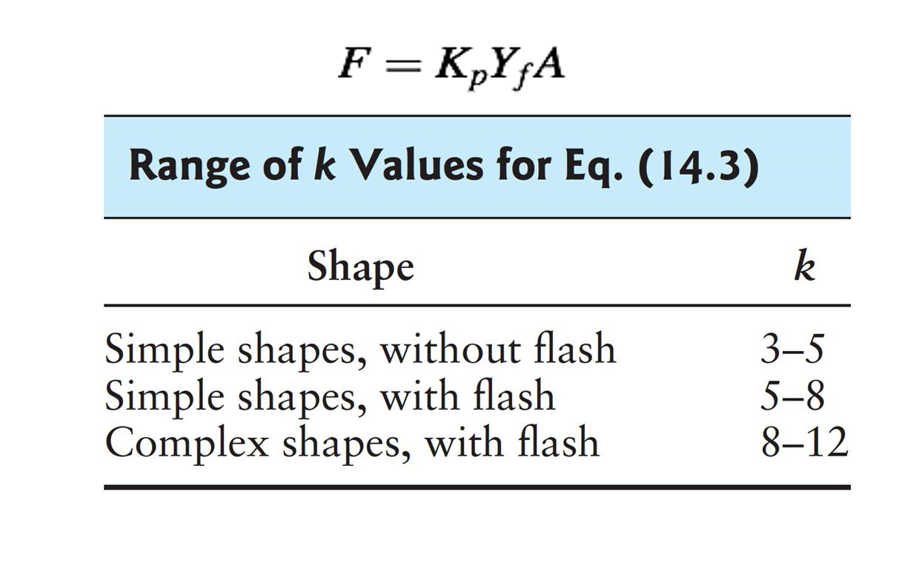
What are impression die forging processes?
Impression die forging also known as “closed-die” forging or “drop” forging is a metal deformation process that involves using enclosed dies to compress a piece of metal to the shape to match the desired final product. The metal can be shaped more precisely and accurately using these dies as a result, this technique is used to produce more complex components. Material flows in the direction of maximum applied stress; and builds in higher strength, toughness, and fatigue resistance.
The processing steps involved in impression die forging:
- Pre-forging (open-die process)
- Blocking
- Finishing
- Trimming
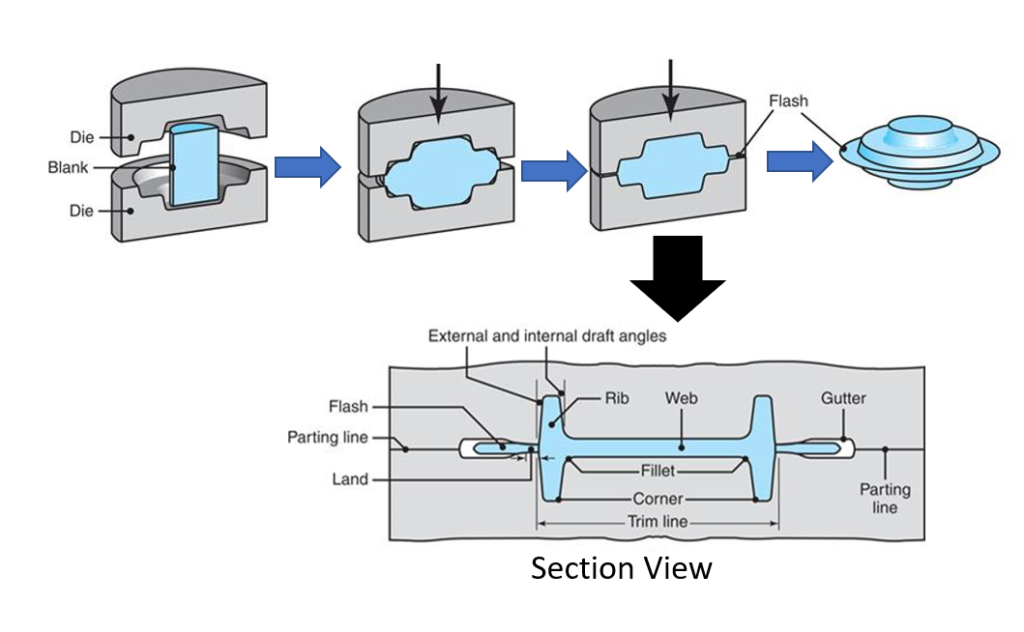
Examples of closed die forging:
Note that due to the complexity of the geometry of the crankshaft, it requires twice as many steps to make when compared to the connecting rod.
Forging a connecting rod for an internal combustion engine:
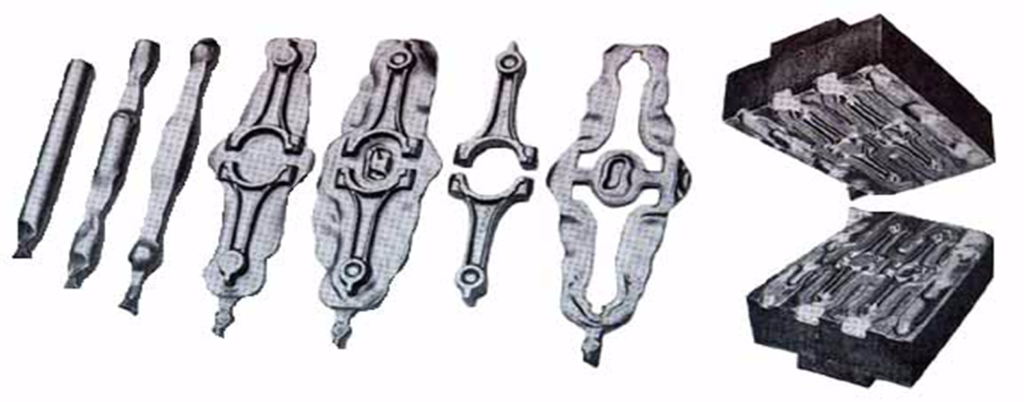
Forging a Crankshaft for an internal combustion engine:
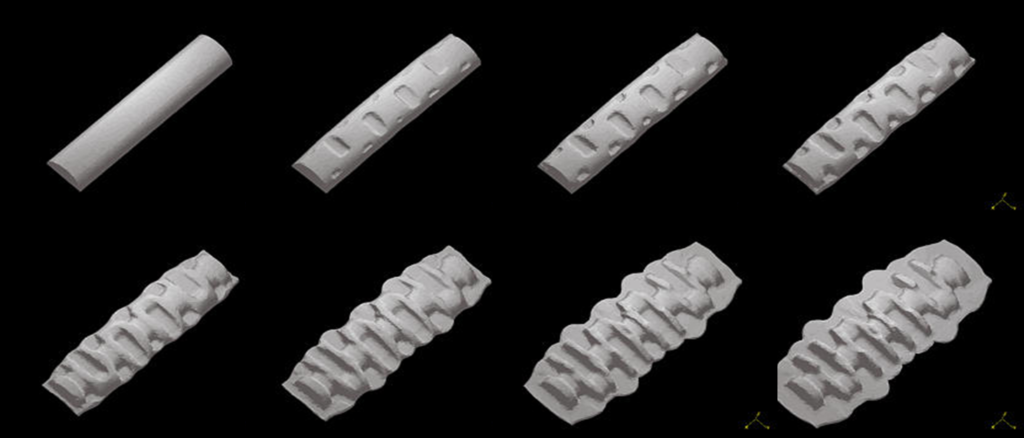
What are the advantages of flashless forging?
Flashless forging is a precise metal-forming technology. This technique eliminates the need for trimming the flash after the forging process, which can save a lot of time and money. The image below shows a comparison of closed-die forging with flash and precision or flashless forging of a round billet.
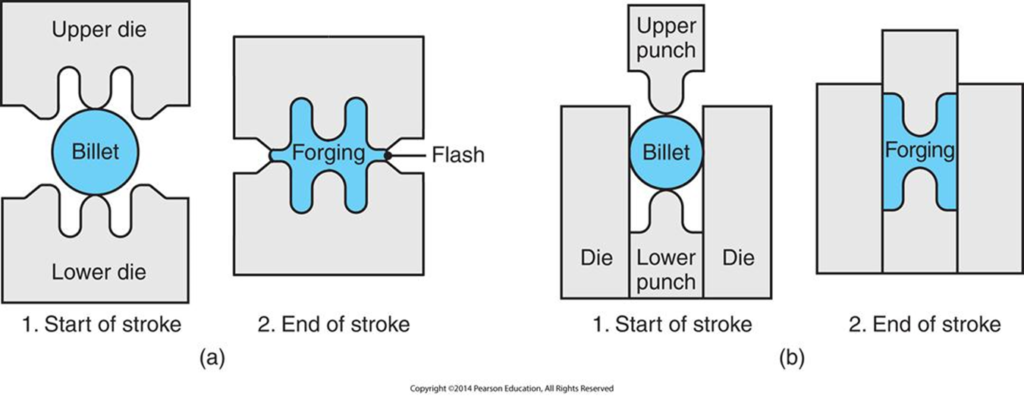
What is coining in forging?
Coining is another closed die forging process that’s used to create very precise shapes and features. It involves applying a lot of pressure to the metal in a very controlled manner to obtain closer tolerances, smoother surfaces and eliminate draft. Early coins were made by open-die forging and lacked precision and sharp details. In contrast, the modern coining operation can achieve much greater detail and superior surface finish.
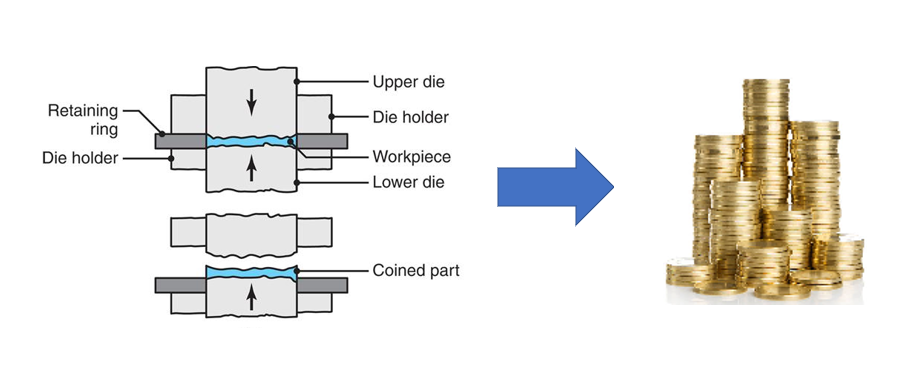
What is piercing forging?
Piercing forging is a metal forging technique performed as an auxiliary process to create holes in forged parts. This is often done by using a punch and die set to create the desired size and shape of the hole. However, piercing does not break through the metal’s surface, like a drilling operation.
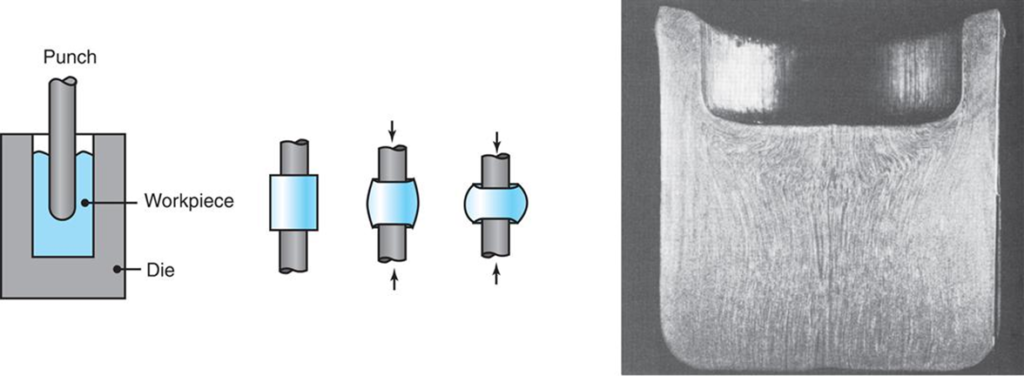
What is a heading process?
The heading is another important forging technique that’s used to create complex shapes and features. It involves using dies to shape the metal in multiple directions, often resulting in a three-dimensional shape. Heading operation is typically used to form heads on fasteners, such as nails and rivets.
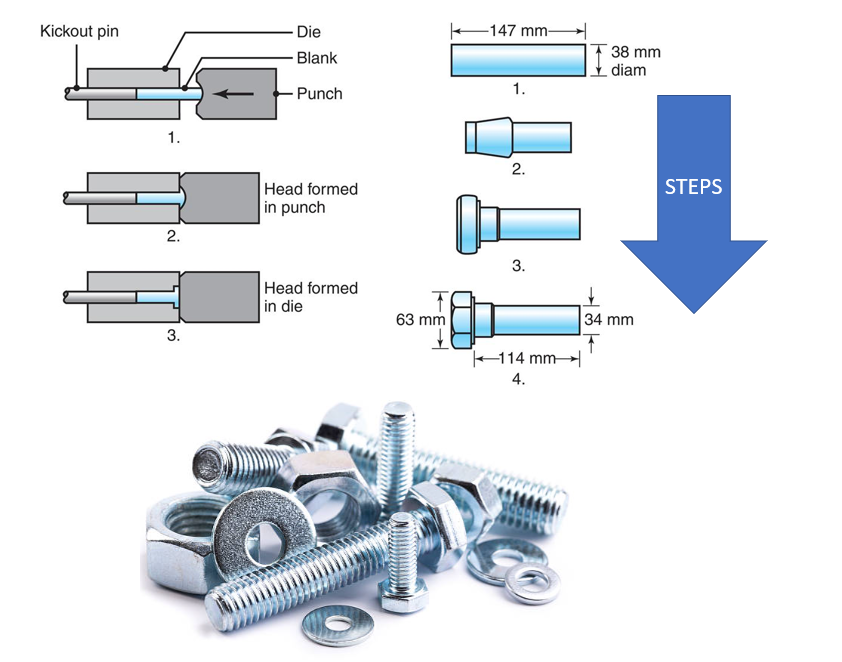
What is the difference between upsetting and heading?
You might be wondering what the difference is between upsetting and heading since the term “heading” is often used interchangeably with upsetting. While both techniques involve compressing metal, the main difference is in the direction of the compression. Upsetting involves compressing the metal in a single direction, while heading involves compressing the metal at the end of the workpiece in multiple directions.
How many types of forging defects are there?
Like any manufacturing process, forging can sometimes result in defects. There are several different types of forging defects, including cracks, porosity, inclusions, unfilled sections, cold shut, scale pits, die shafts, flakes, improper grain growth, incomplete forging penetration, surface cleaning, and residual stresses in forging. These defects can be caused by a variety of factors, including improper heating, incorrect pressure, die cavities being filled prematurely, Laps due to web buckling during forging, or issues with the dies.
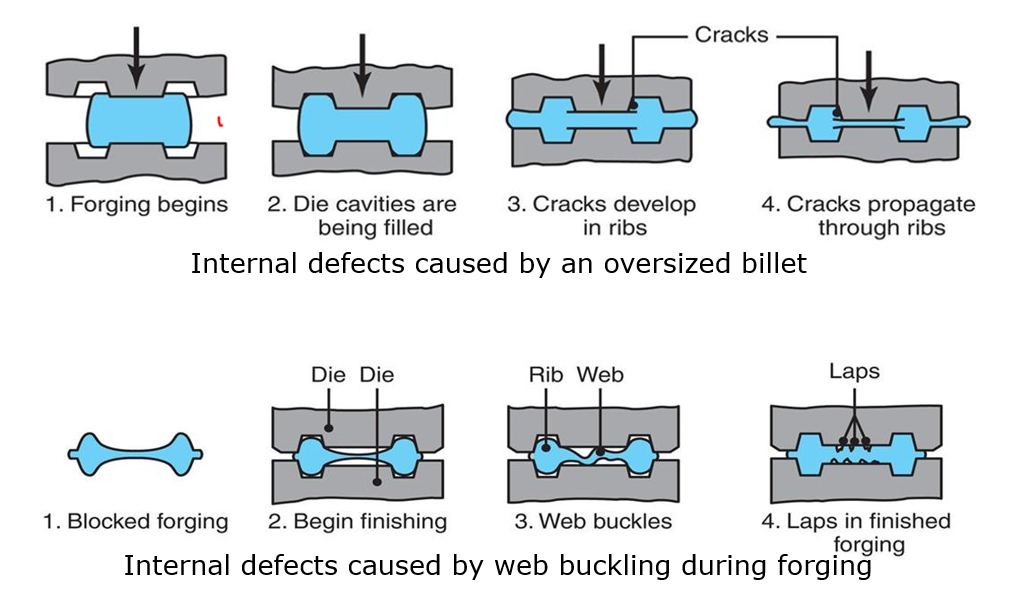
Is forging cost-effective?
Finally, you might be wondering whether forging is a cost-effective manufacturing process. While it can be more expensive than other manufacturing methods like casting or machining, it’s often the best choice for creating parts that require high strength and durability. Additionally, because forging can produce parts in a single step, it can save time and money in the long run by reducing your material costs since you can achieve near-net shapes. The graph below shows the typical cost per piece (unit cost) in forging. It’s important to remember how the setup and the tooling costs per piece decrease as the number of pieces forged increases assuming all pieces use the same die.
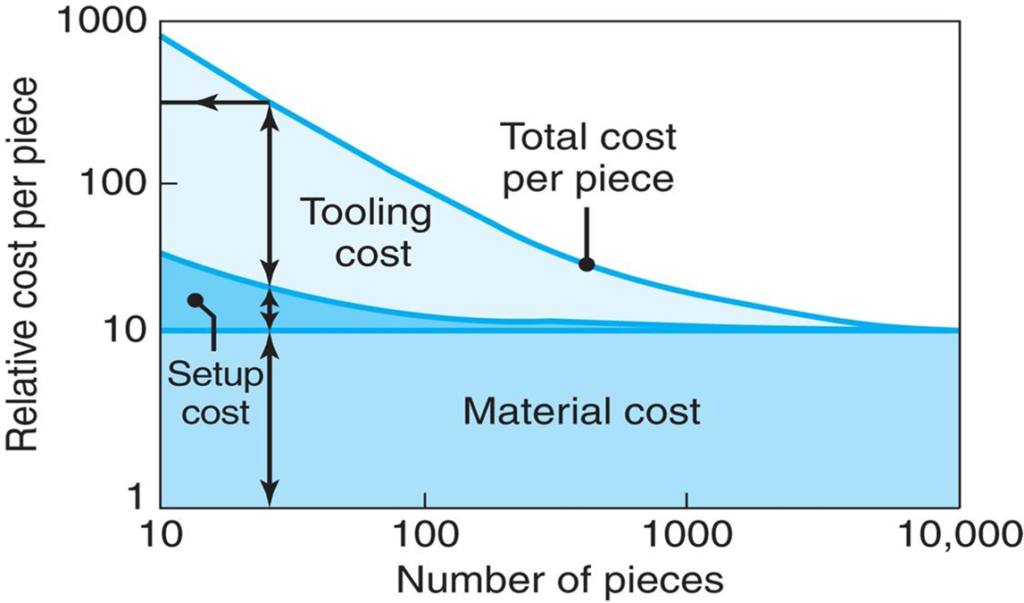
Forging Economics Example: Connecting Rod
Below is a comparison of relative costs per piece of a small connecting rod made by various forging and casting processes. Notice how for large quantities, forging is more economical, and sand casting is the most economical process for fewer than about 20,000 pieces.
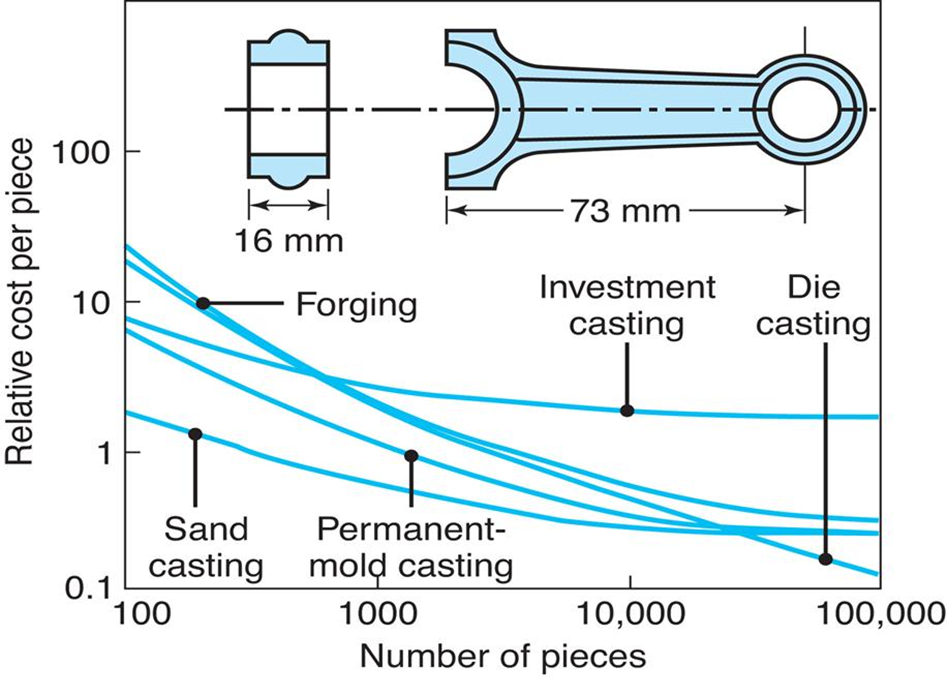
Conclusion
So there you have it, guys – a brief overview of the world of forging manufacturing processes. While it might not sound like the most exciting topic, it’s pretty fascinating when you start to dive into the details. Who knows, maybe one day you’ll even get to try your hand at forging your metal creations!
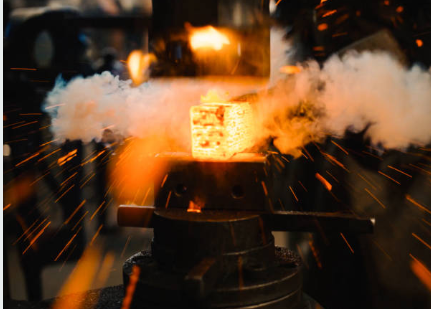
Itís hard to come by knowledgeable people about this subject, but you sound like you know what youíre talking about! Thanks