What is metal vs metal alloy?
Why are metals important?
Metals are used virtually everywhere from paperclips to huge tractors or aircraft. A tractor uses various metals for various components, for example, copper is used to help cool off the engine because of its thermal properties. The engine block is made from cast iron because of its high strength. Finally, the electrical connectors are gold-plated because of their great electrical conductivity. The properties of metallic materials make them ideal for such a wide range of applications because of their cost-to-weight and cost-to-strength ratios. Some properties which make metals so versatile are:
- High stiffness and strength
- Toughness
- Good electrical conductivity
- Good thermal conductivity
- lower cost compared to other engineering materials
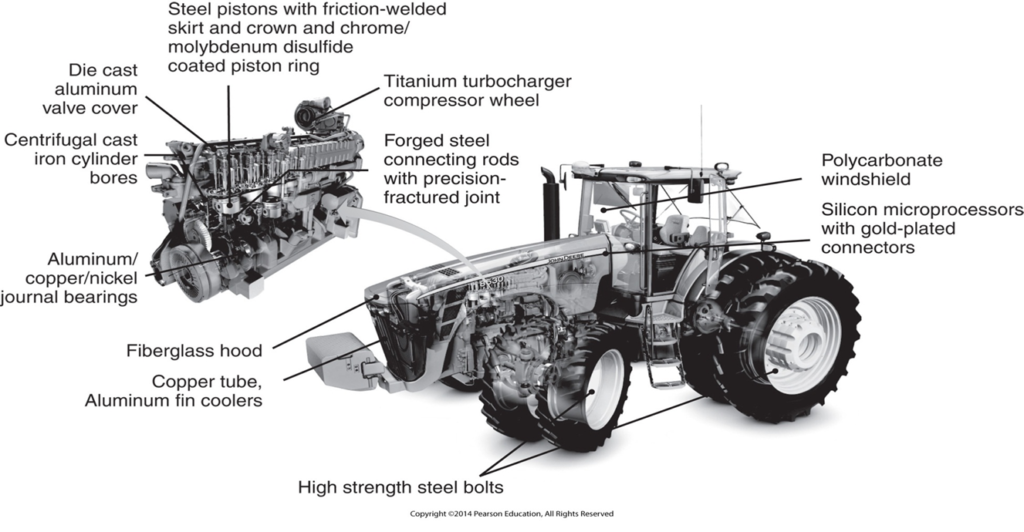
Starting Forms of Metals
- Cast metal (casting)
- Wrought metal
- Powdered metal (powder metallurgy)
Fabrication Characteristics of metal
- Machinability – the ease of machining metal
- Formability – the ease of stamping metal
- Weldingability – the ease to weld metal together
- Castability – the ease to cast metal
What is an alloy?
Metallic alloys are blends of two more metals that have been melted together. Metal alloys have been part of human history for many centuries. The first alloys which humans experimented with were brass and bronze. The invention of metal alloys was so important that it changed the course of human history, the Bronze Age (3300 BC to 1200 BC) is a time period characterized by the use of bronze.
A metal alloy is a material that consists of two or more elements, with at least one of which is metallic. The two main categories of alloys are:
- Solid solutions
- Substitutional
- Interstitial
- Intermediate phases: i.e. intermetallic compounds
Two examples of metal alloys are brass and steel. Brass is an alloy that is made from two metallic elements (copper and zinc). Steel on the other hand is an alloy of metallic element non-metallic elements (Iron and Carbon).
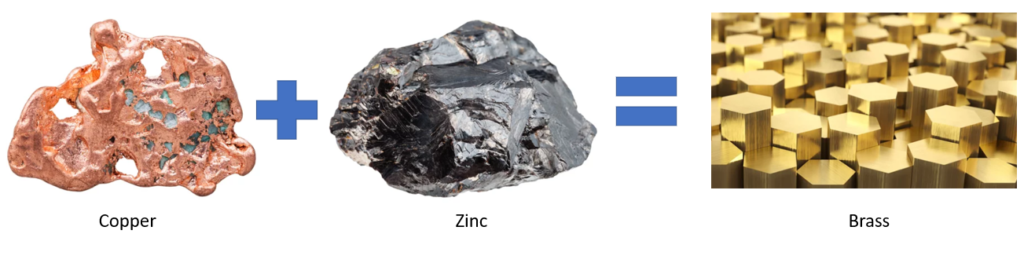
Why are metals alloyed?
Metals are usually alloyed to enhance mechanical or chemical properties to produce desirable manufacturing and service properties. Alloys consist of two or more elements, with at least one of which is metallic. The resulting metal alloy has better properties including hardness, strength, corrosion resistance, and machinability. Metal alloys are classified into two groups:
- Ferrous: 75% of world tonnage
- Steel = iron‑carbon alloy with carbon content ranging from 0.02% to 2.11%
- Cast iron = iron‑carbon alloy with carbon content ranging from 2% to 4% C
- Non-Ferrous
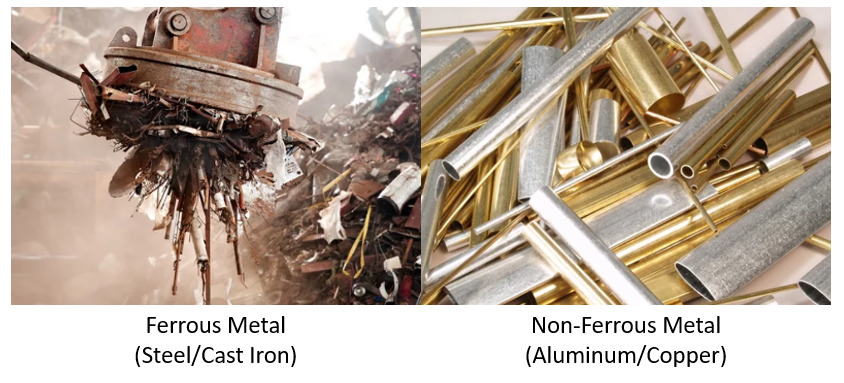
What are the two major groups of metals?
The two main groups of metals are ferrous and non-ferrous. Ferrous metals are metals that are iron-based (steel and cast iron) which makes these types of metal magnetic. Non-ferrous metals are all other irons that are not iron-based (Copper, aluminum ext.) The absence of iron means these metals are not magnetic.
What are ferrous metals’ properties and uses?
Due to the Iron in these types of metals, ferrous metals have higher tensile strength and durability when compared to non-ferrous metals. These types of metals are widely used in the automotive and construction industry.
- Iron-based Metals and Alloys
- Stainless steels
- Cast irons
- Brittle and poor impact properties.
- Lower melting point, making pouring into complex-shaped molds much easier.
- Automotive applications – Cylinder and piston.
What are non-ferrous metals’ properties and uses?
Non-ferrous metals tend to be easier to fabricate and have a higher resistance to corrosion when compared to ferrous metals. They also have good thermal/ electrical conductivity and a lower density. As a result, these metals are used in electrical cables and in cookware (pots and pans).
- Copper and its alloys
- Brass, bronze, and copper-nickels alloys.
- More expensive than steel, but ductile and easily shaped.
- High thermal and electrical conductivity.
- Automotive applications – radiator, wiring, and cabling systems.
- Brass, bronze, and copper-nickels alloys.
- Aluminum and its alloys
Why is the crystal structure of metals important?
Crystalline structures are found in some interstitial compounds and in metals and alloys. These structures are important since they contribute to the mechanical properties of a metal. The body-centered cubic (BCC) has an atom at each corner of a cube beside one atom in the center of the cube. Because of this structure, metals that have a BCC like iron are less ductile but stronger. Face-centered cubic (FCC) has atoms that are arranged at the corners and center of each cube. FCC metals such as copper and silver are usually softer and more ductile when compared to other metals.
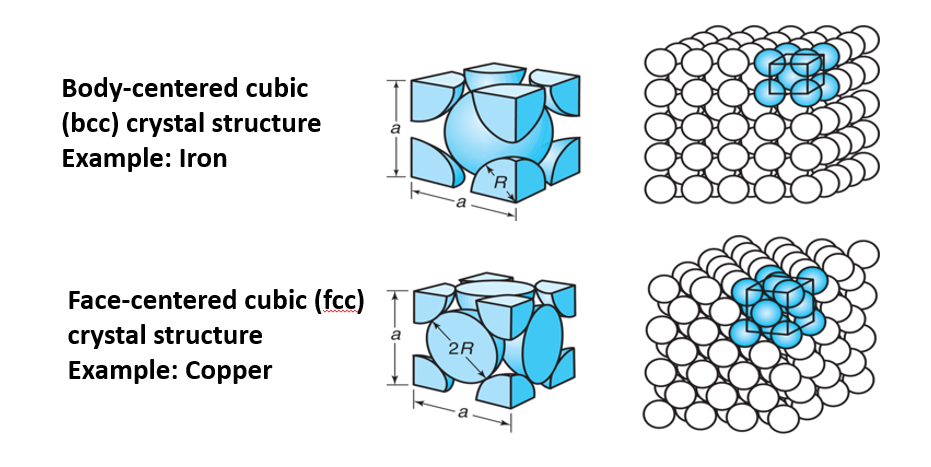
How do you define a solid solution?
A solid solution is made from a mixture of two crystalline solids that make up a different crystalline solid/ crystal lattice. The solid solution can be made from a metallic or non-metallic element dissolved in a metallic base element. A phase is a physically homogeneous material, each phase has a single crystal lattice structure for all grains within the phase.
What is the difference between a substitutional solid solution and an interstitial solid solution?
A substitutional solid solution is a composite of two elements where the solute atoms displace the solvent atoms. For this to occur, the solute atoms should be comparable in size to the solvent atoms in the lattice. When both the solvent and solute metals are heated up, the solute atoms can fuse themselves into the lattice by displacing a solvent atom. As a result, the lattice which was composed of all solvent atoms is now composed of at least one solute atom in the lattice. This substitution can occur in a random location of the lattice crystal or the solute can always occupy the same location in the crystal, this depends on the two elements being combined. An example of this would be brass which is a copper-nickel alloy. The copper atoms are slightly smaller in size than the nickel allowing for a substitutional solid state.
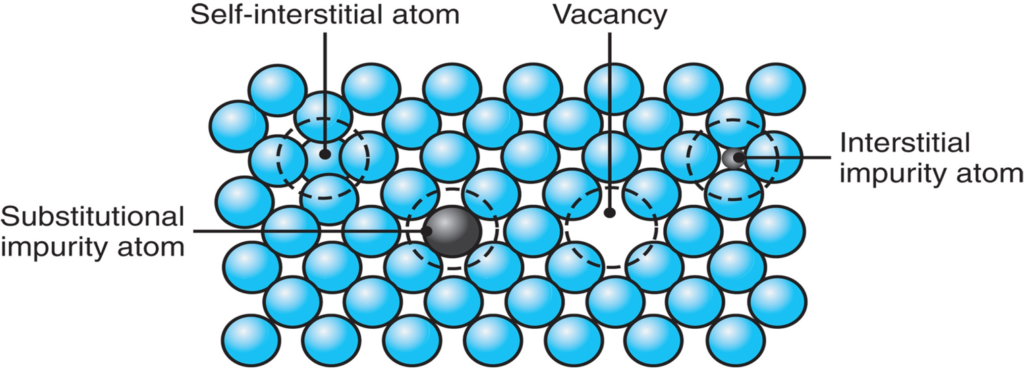
Interstitial solid solutions are formed when solute atoms enter the gaps or interstitial position between solvent atoms of the lattice. For the solute atoms to be able to fit within the interstitial location, they must be less than half the size of solvent atoms. Having such a small atom in the interstitial position causes some deformation in the lattice which can result in changing the properties of the solvent element (strain hardening). An example of this would be steel which is created with iron and carbon. The size of the carbon atoms is much smaller than iron allowing them to fit in the interstitial of the iron lattice. As a result of the addition of carbon, the strength of the iron goes up.
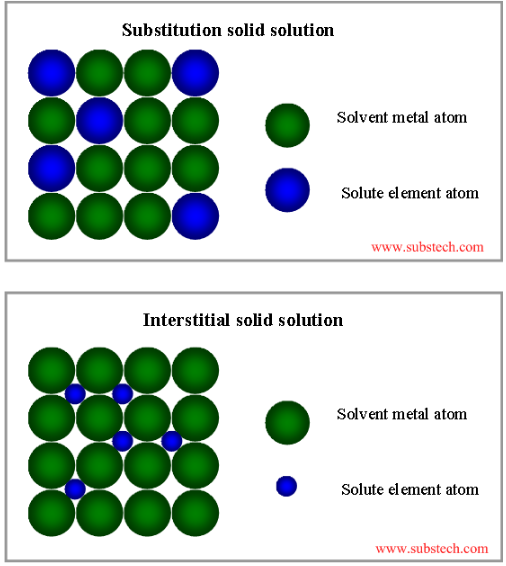
How does carbon content in steel affect its properties?
As the carbon content in steel increases the hardness and strength of the steel increase, but as a side effect the steel becomes more brittle. As a result the higher the carbon content in the steel the lower the elongation and impact load. High-carbon steel is steel with a carbon percentage greater than 0.6%, this high carbon content can cause complications or challenges due to its reduced weldability properties. The reason for this is that high-carbon steel has a tendency to form martensite.
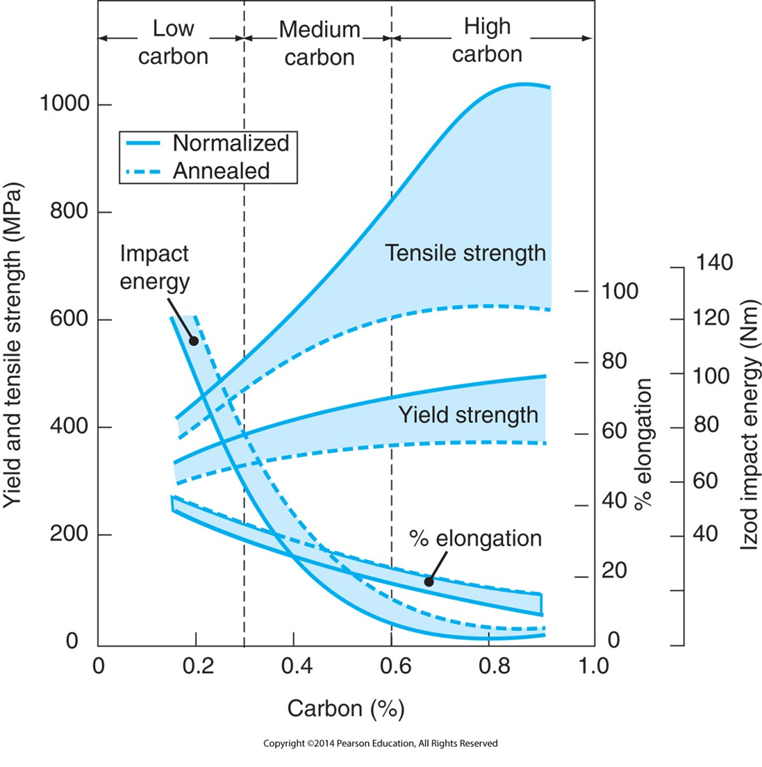
What is a slip line in metal forming?
Slip lines are planes of maximum shear stress and ultimately affect how a material will experience deformation. A slip band consists of a number of slip planes. The slip lines are oriented at 45 degrees to the axes of principal stress. The crystal at the center of the upper illustration is an individual grain surrounded by several other grains.
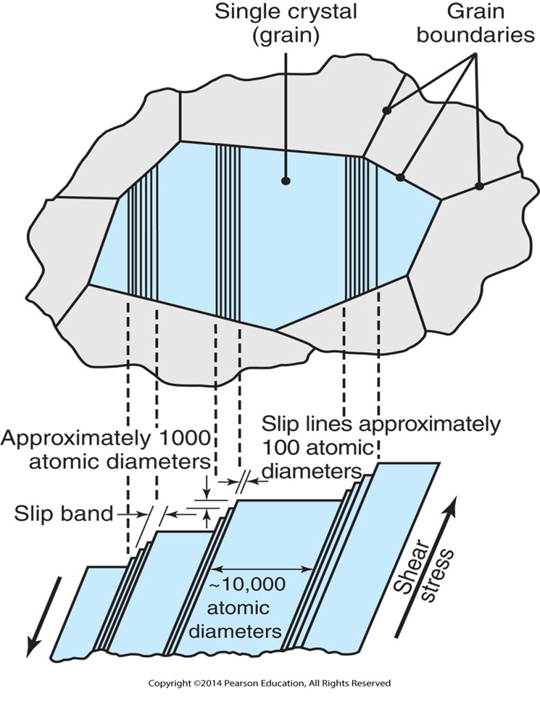
What is the difference between slip and twinning?
Slip occurs in discrete multiples of atomic spacing and happens in milliseconds while twinning is the movement of atoms that is lesser in atomic spacing and usually takes microseconds to occur.
Permanent deformation of a single crystal under a tensile load:
- the highlighted grid of atoms emphasizes the movement that occurs within the lattice.
- Deformation by slip. The b/a ratio influences the magnitude of the shear stress required to cause a slip.
- Deformation by twinning, involves the generation of a “twin” around a line of symmetry subjected to shear.
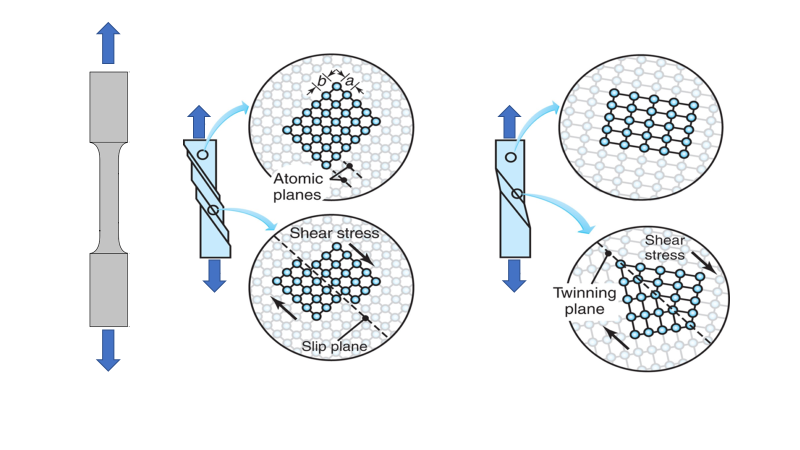
How do slip planes affect the strength of steel?
As the metal experiences internal shear stress due to external forces such as machining or metalworking, the atoms in the metal start moving along intersecting slip planes. If the metal has any dislocation (defect or irregularity within a crystal structure) then the dislocation will move with the stress causing the metal to become stronger in the process.
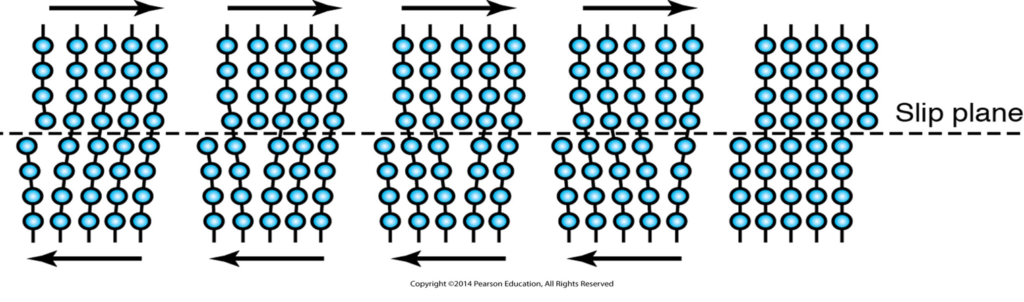