Steel in a Car: Explained
Steel in a Car finds application in numerous of car components like the frame, body, and moving parts such as chassis and powertrain components, thanks to its adaptability in meeting safety standards, crash requirements, and design specifications. Its exceptional capability to absorb and distribute crash energy, along with its buckling characteristics, makes it excellent for improving a vehicle’s crashworthiness. Furthermore, steel’s recyclability contributes to reducing a vehicle’s environmental impact.
What kind of steel is used in the automotive industry?
The Steel in a Car ranges from stainless, high-strength, Advanced High Strength Steel (AHSS), high-carbon, and low-carbon steels, to galvanized steel, all employed in crafting different vehicle and engine parts.
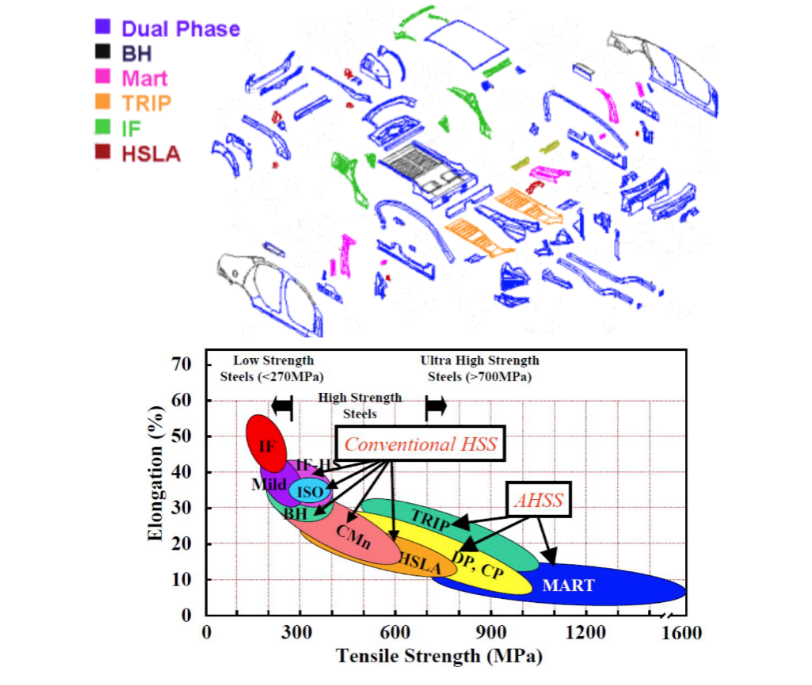
What is meant by dual-phase steel?
Developed in the 1970s, dual-phase steel (DP) is a high-strength steel that provides the
advantages of high-strength steel without losing good overall elongation. As a result of its
microstructure consisting of both ferritic–martensitic microstructure. DP steel has good fatigue resistance making it ideal for automotive-related sheet-forming operations.
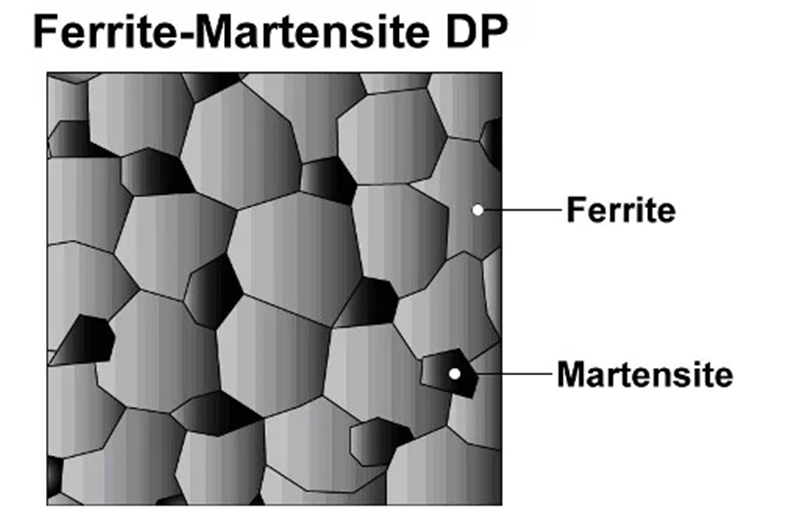
Mechanical properties of common dual-phase Steels
Grade designation | Yield strength (MPa), Minimum | Tensile strength (MPa), Minimum | % Total elongation, minimum, cold reduced | YS/TS ratio |
---|---|---|---|---|
DP600 | 340 | 590 | 21 | 0.58 |
DP800 | 420 | 780 | 14 | 0.54 |
DP1000 | 550 | 980 | 8 | 0.54 |
What is bake-hardening steel?
Bake hardening is a steel that has undergone a controlled aging process during thermal treatment which is known as the bake hardening effect. This steel is an excellent choice for class-A panels that must also be dent-resistant. Bake-hardenable steels have been used for many years to downgauge exterior panels without reducing denting performance. After stamping conventional high-strength steel into the desired shape, it is baked (thermal cycled) similar to paint curing.
What is martensite state?
Martensite is the hardest phase of steel. By rapidly cooling (quenching) high-carbon steel at very high rates from the austenite–ferrite region, you form martensite. These materials have very high tensile strength but the lowest percent elongation of all the AHSS. Martensitic stainless steels are alloys that have a body-centered tetragonal (bct) crystalline structure.
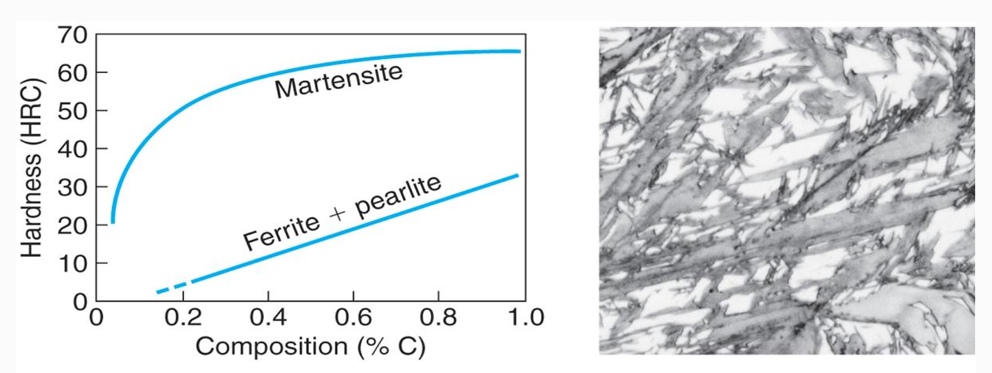
What does TRIP steel stand for?
Transformation-induced plasticity also known as TRIP steels is a class of high-strength steel alloys that uses higher quantities of carbon to obtain sufficient carbon content for stabilizing the retained austenite phase to below room temperature. The TRIP effect is the particular formation of islands of martensite which is surrounded by ferrite and bainite. As a result; these types of metals have a large uniform elongation, high strength, and high fracture toughness.
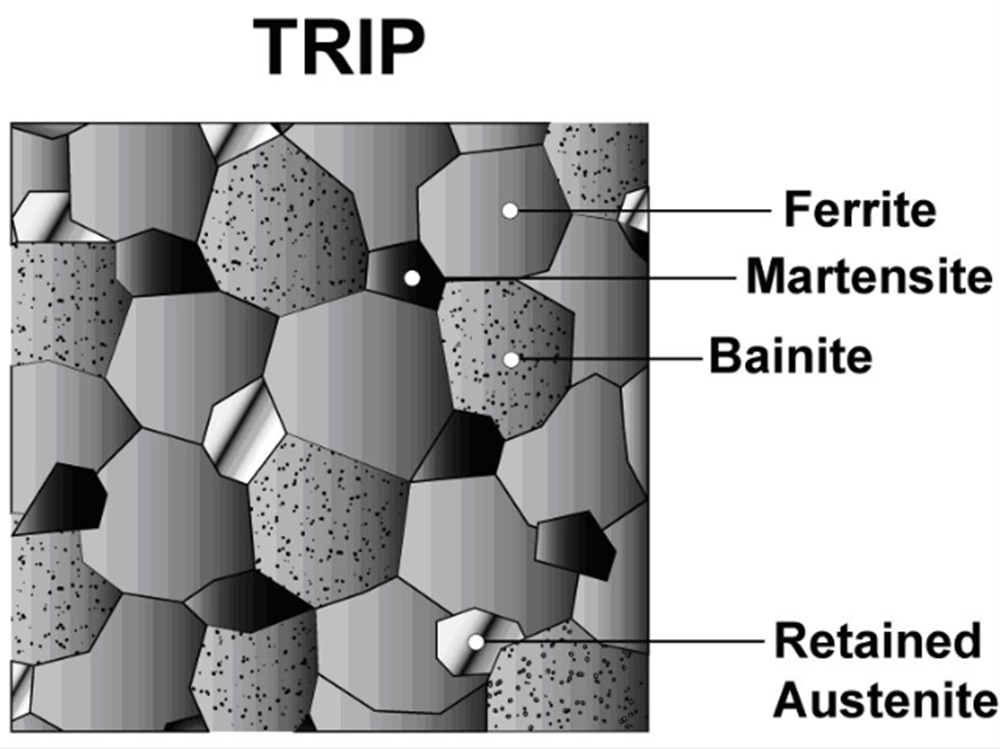
Chemistry of a typical TRIP steel (General Motors Corporation data).
%C | %Mn | %Si | %Al | %P | %Cr | %Ni | %N | %Ti |
---|---|---|---|---|---|---|---|---|
018 | 1.5 | 0.05 | 2 | 0.01 | 0.02 | 0.002 | 0.003 | 0.003 |
What is interstitial-free?
IF steel gets its name from the fact, that there are minimal interstitial solute atoms to strain the solid iron lattice. IF steels have very low carbon contents, typically in the bandwidth of 20–50 ppm (0.002%–0.005%), and commonly have manganese levels below 0.25%. As a result, they have very high elongations that can approach or even exceed 50%. They also have very high strain hardening coefficients that are advantageous when stamping very difficult-to-form parts.
High-strength low-alloy steel:
Unlike other types of conventional steels, HSLA steels are not made to meet a specific chemical composition but rather specific mechanical properties. As a result, HSLA provides better mechanical properties or greater resistance to corrosion than carbon steel.
Mechanical properties of common HSLA steels
Grade designation | Yield strength, (MPa), Minimum | Tensile strength, (MPa), Minimum | Total elongation (%)a, minimum cold rolled | Total elongation (%)a, minimum, hot rolled |
---|---|---|---|---|
300 | 300 | 400 | 27 | 27 |
340 | 340 | 410 | 25 | 25 |
380 | 380 | 450 | 23 | 23 |
420 | 420 | 490 | 18 | 22 |
550 | 550 | 620 | 16 | 18 |
Comparison of mechanical properties of various grades of steel
Elongation is 50 mm with an ISO #1 tensile bar.
Tensile strength (MPa) | Yield strength (MPa) | Total elongation (%)a | Uniform elongation (%)a | n-value | |
---|---|---|---|---|---|
Mild steel | 181 | 296 | 42.4 | 21.4 | 0.208 |
HSLA 340 | 375 | 480 | 24 | 13 | 0.15 |
Dual-Phase 600 | 355 | 623 | 26 | 19 | 0.18 |
Dual-Phase 800 | 440 | 825 | 17 | 18 | 0.13 |
TRIP800 | 503 | 831 | 27.6 | 21.5 | 0.236 |
Conclusion
In conclusion, steel plays a critical role in the automotive industry, providing the necessary strength, safety, and recyclability for modern vehicles. Its versatility allows engineers to design cars that meet stringent safety standards while also considering environmental impact. As technology advances, steel continues to evolve, ensuring that it remains a key material in the cars we drive today and into the future.
Source:
C.D. Horvath, Chapter 2 – Advanced steels for lightweight automotive structures, Editor(s): P.K. Mallick,
In Woodhead Publishing in Materials, Materials, Design, and Manufacturing for Lightweight Vehicles (Second Edition), Woodhead Publishing, 2021, Pages 39-95, ISBN 9780128187128, https://doi.org/10.1016/B978-0-12-818712-8.00002-1.